- AI In the Warehousing Market Size & Trends
- Why Warehouse Management Needed an Upgrade Anyway?
- Challenge: Pervasive Human Error and Inefficiency
- Challenge: Lack of Real-time Visibility and Data Silos
- Challenge: Suboptimal Space Utilization
- Challenge: Limited Adaptability and Scalability
- Challenge: High Operational Costs
- What are the Benefits of AI in Warehouse Management?
- Enhanced Demand Forecasting
- Real-Time Inventory Tracking and Visibility
- Optimized Inventory Replenishment
- Fraud Detection and Loss Prevention
- Scalability and Adaptability
- Integration with Supply Chain Ecosystems
- AI Use Cases in Warehouse Management
- AI-Driven Demand Forecasting
- Optimized Inventory Management & Control
- Intelligent Warehouse Layout & Space Optimization
- Predictive Maintenance for Warehouse Equipment
- Autonomous Picking & Packing
- Route Optimization for Inbound & Outbound Logistics
- Quality Control & Damage Detection
- Appinventiv: Your Best AI Partner to Automate Your Warehouse Management System
- How Appinventiv Automates Your Warehouse Management with AI?
- Why Appinventiv Stands Out in AI-Powered Warehouse Automation?
- Partnering for a Smarter Warehouse Future
- FAQs
Key takeaways:
- AI-Driven Optimization: AI enhances warehouse efficiency by automating workflows, reducing errors, and optimizing inventory with real-time data.
- Cost Reduction: AI cuts operational costs by minimizing labor, storage, and return expenses, with McKinsey noting 5-20% logistics cost savings.
- Improved Forecasting: AI-powered demand forecasting prevents stockouts and overstocking, improving customer satisfaction and cash flow.
- Space and Route Efficiency: AI optimizes warehouse layouts and logistics routes, reducing travel time and increasing storage capacity.
- Scalable Automation: AI integrates with robotics and IoT for autonomous picking, packing, and predictive maintenance, ensuring scalability.
For many enterprises, the warehouse isn’t a streamlined operation; it’s a constant battle. Companies frequently encounter numerous challenges that hinder growth and erode profitability.
Inefficient workflows lead to bottlenecks and slow order fulfillment, frustrating customers and hindering revenue growth. High operational costs, driven by excessive labor, bloated storage expenses, and a deluge of returns, eat into already thin margins. Add to this the persistent headache of inaccurate inventory, resulting in costly stockouts or wasteful overstocking, and the challenge of scaling to meet ever-growing customer demands. Manual errors abound, real-time visibility is often a pipe dream, and decision-making remains reactive rather than strategic.
These persistent issues aren’t just minor inconveniences; they directly impact a business’s ability to compete and thrive in today’s dynamic market. They hinder expansion, dampen customer satisfaction, and ultimately, undermine the very foundation of sustainable growth. The pressure to deliver faster, more accurately, and at a lower cost is immense. Yet, many warehouses find themselves trapped in outdated processes, unable to break free from the cycle of inefficiency.
But what if there were a way to move beyond these challenges? Enter artificial intelligence warehouse management– not just a buzzword, but a powerful, practical solution ready to transform your warehouse from a liability into a strategic asset. AI for warehouse management brings unprecedented levels of optimization, predictability, and automation to every corner of your warehouse, allowing you to streamline operations, cut costs, and unlock significant growth opportunities.
- AI enables reductions of 5 to 20 percent in logistics costs.
- AI can create reductions of 20 to 30 percent in inventory.
According to CDO Times, Amazon leveraged machine learning and AI to save $1.6 billion in transportation and logistics costs.
Let’s dive deep into 10 practical use cases of AI in warehouse management that can significantly enhance your business’s efficiency and bottom line.
AI In the Warehousing Market Size & Trends
The global AI in warehousing market size was estimated at USD 11.22 billion in 2024 and is expected to grow at a compound annual growth rate (CAGR) of 26.1% from 2025 to 2030. This can be attributed to the surge in e-commerce, which demands faster and more accurate order fulfillment. (Source: Grand View Research)
Why? Because the pace of innovation is relentless. Tech giants are developing some mind-blowing systems and applying them across various industries, from healthcare to finance to warehouse management. For example, Amazon’s AI-powered Sequoia system enables the company to transport inventory, storing it 75% faster.
That’s just one example, but it illustrates how AI is impacting nearly every corner of the industry, including warehouse management.
In this guide, we’ll walk you through the top 10 use cases of AI in warehouse management, providing real-world examples, statistics, and, yes, some valuable lessons from our work.
See AI in Action for Your Warehouse Operations.
Why Warehouse Management Needed an Upgrade Anyway?
A warehouse management system development (WMS) has long been the backbone of supply chain operations, ensuring that goods move efficiently from suppliers to customers. However, traditional warehouse management systems (WMS) have struggled to keep pace with the demands of modern commerce, including the growth of e-commerce, the complexities of global supply chains, and rising customer expectations.
This warehouse management system needs an upgrade to address key challenges that have exposed the limitations of legacy systems. However, AI for warehouse management solutions that address these issues can deliver transformative results.
Challenge: Pervasive Human Error and Inefficiency
Traditional warehouses heavily relied on manual processes for tasks like inventory counting, order picking, and data entry. This led to frequent human errors, such as mispicks, inaccurate inventory counts, and shipping errors, resulting in customer dissatisfaction, costly returns, and significant wasted labor hours on error correction and item retrieval.
Solution: Automated & Guided Workflows with Real-time Data Capture
Modern WMS introduces automated and guided workflows, often leveraging barcode scanning, RFID, and handheld devices to enhance efficiency. This minimizes manual data entry and provides pickers with optimized routes and precise instructions, drastically reducing errors and increasing efficiency. Real-time data capture ensures that every movement is immediately recorded, eliminating discrepancies.
Also Read: Enterprise Data Warehouse: How it Benefits Your Business?
Challenge: Lack of Real-time Visibility and Data Silos
Inventory data in traditional setups was often fragmented across paper records, spreadsheets, or disparate, unconnected systems. This created significant data silos, preventing a unified, real-time view of stock levels, product locations, and order statuses, making effective planning, forecasting, and agile decision-making nearly impossible.
Solution: Centralized, Real-time WMS Database
A modern WMS acts as a central nervous system for the warehouse, providing a single, unified, and real-time database for all inventory and operational data. Every item’s location and status are continuously updated, giving businesses immediate and accurate visibility into their entire inventory and order fulfillment process, enabling proactive management.
Challenge: Suboptimal Space Utilization
Without advanced analytical tools, traditional warehouse layouts and storage strategies were often inefficient. This resulted in wasted cubic capacity, congested aisles, and suboptimal storage locations, directly affecting storage density and throughput. Businesses struggled to maximize their significant investment in physical warehouse space.
Solution: Dynamic Slotting and Intelligent Putaway/Picking Algorithms
Modern WMS utilizes sophisticated algorithms to optimize space. It enables dynamic slotting, placing products in ideal locations based on velocity, size, weight, and pick frequency. The system guides intelligent putaway and picking, ensuring efficient use of vertical and horizontal space, reducing travel distances for pickers, and maximizing overall storage capacity and efficiency.
Challenge: Slow Throughput and Bottlenecks
Manual processes and inefficient routing created significant bottlenecks at various stages of the warehouse operation, including receiving, putaway, picking, and packing. This limited the overall throughput, making it challenging for businesses to handle increasing order volumes, particularly with the rise of e-commerce and the growing expectation for faster delivery.
Solution: Process Automation and Integration with Material Handling Equipment
WMS streamlines processes by automating decision-making and optimizing workflows (e.g., wave picking, batch picking). Crucially, it integrates seamlessly with advanced material handling equipment like conveyors, AS/RS (Automated Storage and Retrieval Systems), AGVs (Automated Guided Vehicles), and robotics. This coordination drastically reduces manual handling, speeds up item movement, and eliminates bottlenecks, significantly boosting overall throughput.
Challenge: Limited Adaptability and Scalability
Traditional warehouse systems were rigid and struggled to adapt to fluctuating demand, the introduction of new product lines, or changes in order profiles. Scaling operations to accommodate business growth often meant costly physical expansions and simply adding more labor, rather than leveraging existing resources more efficiently.
Solution: Configurable and Modular WMS Architecture
Modern WMS platforms are designed with a configurable and modular architecture. This allows businesses to easily adjust rules, workflows, and capacities to meet changing market demands, seasonal peaks, or the addition of new SKUs without extensive reprogramming. Their inherent scalability enables growth in volume and complexity without requiring fundamental system overhauls.
Challenge: High Operational Costs
The cumulative effect of inefficiencies, errors, wasted space, and slow throughput in traditional warehouses translates directly into higher operational costs. This included increased labor expenses for manual tasks and error correction, higher inventory holding costs due to inaccuracies, and expenses related to customer service issues and product returns.
Solution: Cost Reduction through Efficiency, Accuracy, and Optimization
A modern WMS directly contributes to significant cost reductions by improving efficiency, accuracy, and overall optimization. Lower labor costs result from the implementation of automated processes and optimized workflows. Reduced errors result in fewer returns and fewer customer service issues. Better space utilization avoids unnecessary physical expansions. Accurate inventory management via AI minimizes overstocking and stockouts, resulting in substantial savings and improved profitability.
What are the Benefits of AI in Warehouse Management?
Traditional inventory management methods often struggle to keep up with the complexities of modern supply chains, fluctuating demand, and vast datasets. This is where artificial intelligence warehouse management steps in, revolutionizing inventory management with unprecedented accuracy, efficiency, and adaptability.
Let’s explore the transformative benefits of AI for warehouse management and how it empowers businesses to thrive in a dynamic market.
Enhanced Demand Forecasting
One of the most significant challenges in inventory management is accurately predicting customer demand. Overstocking ties up capital and increases storage costs, while understocking leads to missed sales opportunities and dissatisfied customers. AI-powered demand forecasting utilizes machine learning algorithms to analyze historical sales data, market trends, seasonality, and external factors, including weather and economic conditions.
Benefits:
- Reduced Stockouts and Overstocks: AI minimizes the risk of having too much or too little inventory by providing precise demand predictions.
- Improved Customer Satisfaction: Ensuring products are available when customers want them enhances the shopping experience.
- Cost Savings: Accurate forecasting reduces excess inventory, lowering storage and handling costs.
Real-Time Inventory Tracking and Visibility
AI enables real-time inventory tracking by integrating with Internet of Things (IoT) devices, such as RFID tags and smart sensors. These technologies provide real-time updates on inventory levels, locations, and conditions, enabling businesses to maintain complete visibility into their supply chain.
Benefits:
- Improved Accuracy: Real-time tracking reduces errors associated with manual inventory counts.
- Faster Decision-Making: Leveraging data analytics for inventory optimization enables managers can respond quickly to stock shortages or supply chain disruptions, ensuring timely and effective action.
- Enhanced Transparency: Businesses gain a clear view of inventory across multiple locations, enabling better coordination.
Optimized Inventory Replenishment
AI automates and optimizes the replenishment process by determining the ideal time and quantity for restocking. This ensures that inventory levels are maintained without tying up excessive capital or risking stockouts.
Benefits:
- Reduced Manual Effort: Automation eliminates the need for manual reorder calculations, freeing staff to focus on strategic tasks.
- Cost Efficiency: AI ensures just-in-time inventory practices, minimizing holding costs.
- Supply Chain Resilience: AI can adjust replenishment plans in response to disruptions, such as delayed shipments or supplier issues, thereby enhancing overall supply chain resilience.
Fraud Detection and Loss Prevention
Inventory shrinkage—caused by theft, fraud, or administrative errors—can significantly impact profitability. AI helps detect and prevent these issues by analyzing patterns and anomalies in inventory data.
Benefits:
- Reduced Losses: Early financial fraud detection with ML of shrinkage minimizes financial losses.
- Improved Security: AI enhances oversight of inventory processes, deterring theft and fraud.
- Data Integrity: AI ensures accurate inventory records, reducing administrative errors.
Scalability and Adaptability
AI systems are highly scalable, making them ideal for businesses of all sizes. Whether a small retailer or a global enterprise, AI can adapt to changing business needs and handle growing volumes of data.
Benefits:
- Flexibility: AI systems grow with the business, supporting expansion without requiring significant infrastructure changes.
- Resilience: AI adapts to disruptions, such as supply chain delays or sudden demand spikes.
- Cost-Effective Scalability: Cloud-based AI reduces the need for costly on-premises hardware.
Integration with Supply Chain Ecosystems
AI seamlessly integrates with other supply chain technologies, such as Enterprise Resource Planning (ERP) systems, Warehouse Management Systems (WMS), and Customer Relationship Management (CRM) platforms. This creates a unified ecosystem for managing inventory and related processes.
Bonus Read: Guide to ERP System Integration
Benefits:
- Unified Operations: Integration eliminates data silos, improving coordination across departments.
- Enhanced Decision-Making: A comprehensive view of operations facilitates more informed strategic planning.
- Streamlined Processes: Automation across systems reduces manual work and improves efficiency.
AI Use Cases in Warehouse Management
Manual processes lead to human error, unexpected breakdowns halt critical operations, and the sheer volume of data makes informed decision-making feel like an impossible task. This isn’t just about moving boxes; it’s about the very arteries of your business, and when they’re clogged, growth grinds to a halt. But thanks to AI in Warehouse management, which intelligently optimizes every single function, while turning every chaotic complexity into streamlined efficiencies.
Let’s explore different AI use cases in warehouse management, illustrating how this powerful technology can enhance your workflows and drive business growth.
AI-Driven Demand Forecasting
Predicting future product demand with high accuracy to optimize inventory levels and prevent stockouts or overstocking.
How AI Works:
- Traditional demand forecasting often relies on historical sales data and simple statistical models, which struggle to cope with volatile market conditions or unforeseen events.
- AI, powered by advanced algorithms for machine learning in warehouse management (such as neural networks and time series analysis), processes vast and diverse datasets. This includes not only historical sales figures but also external factors like seasonality, promotional activities, economic indicators, weather patterns, and even social media sentiment.
- By analyzing these complex interdependencies, AI identifies intricate patterns and correlations that are invisible to human analysts or conventional methods, leading to significantly more precise and responsive demand predictions.
Tangible Benefits for Businesses:
- Reduced Inventory Holding Costs: By precisely matching supply with demand, businesses avoid overstocking, freeing up capital tied in excess inventory and reducing storage expenses.
- Minimized Stockouts and Lost Sales: Accurate forecasts ensure products are available when customers want them, preventing missed sales opportunities and improving customer satisfaction.
- Improved Cash Flow: Optimized inventory means less capital is tied up in warehouses, thereby improving liquidity.
- Better Resource Allocation: Enhanced predictability allows for more efficient planning of labor, equipment, and storage space.
Real Example: Walmart’s AI-Driven Demand Forecasting
Challenge: Walmart faced issues with traditional forecasting and inventory management, resulting in frequent stockouts, overstocking, increased costs, and lost sales. This resulted in a staggering $1.7 trillion in annual losses for retailers due to poor inventory management (including overstocking, understocking, and deadstock).
Solution: Walmart leverages AI and machine learning to optimize its inventory system in several ways:
- Predictive Analytics: AI models analyze purchasing patterns, weather data, and seasonal trends to forecast product demand accurately. This ensures stores are stocked with the right quantity of products, reducing overstocking and stockouts.
- Real-time Inventory Tracking and Automation: AI systems provide real-time visibility into inventory levels across the supply chain, enabling quick replenishments and automating restocking processes.
- Supply Chain Optimization: Walmart’s proprietary machine learning platform, Element, allows for rapid and scalable AI deployment. The “Self-Healing Inventory” system automatically reroutes supplies to address overstocks.
- Dynamic Pricing: AI helps determine optimal pricing strategies based on demand, competition, and inventory levels. (Source: Walmart)
Optimized Inventory Management & Control
Maintaining optimal inventory levels, reducing waste, and ensuring accurate stock counts across the warehouse.
How AI works:
- AI continuously monitors every inventory movement, from inbound shipments to outbound orders. It leverages real-time data from various sources, including RFID tags, IoT sensors in retail stores, and computer vision systems, to provide highly accurate, live inventory counts, drastically reducing the need for time-consuming manual audits.
- AI algorithms identify slow-moving or obsolete items, recommending strategic actions like targeted promotions or disposal.
- Furthermore, predictive analytics within AI systems can anticipate potential shrinkage, discrepancies, or quality issues, alerting managers proactively.
- AI also optimizes reorder points and quantities by considering lead times, supplier reliability, and dynamic demand forecasts, automating the replenishment process.
Tangible Benefits For Businesses:
- Significant Reduction in Carrying Costs: Minimizes expenses associated with storing, insuring, and managing excess inventory.
- Elimination of Dead Stock and Obsolescence: Proactive identification and management of slow-moving items prevent financial losses.
- Improved Cash Flow: Capital is not unnecessarily tied up in inventory, allowing for better working capital management.
- Higher Inventory Accuracy: Leads to more reliable planning, fewer picking errors, and enhanced operational efficiency.
Real Example: Coca-Cola AI-Powered Supply Chain Optimization
Challenge: Coca-Cola’s global operations require managing a complex supply chain across production, distribution, and inventory in numerous countries. The company faced challenges in accurately forecasting demand, minimizing waste, reducing operational costs, and maintaining equipment uptime, all while aligning with its sustainability goals. (Source: VentureBeat)
Solution:
- Coca-Cola leverages AI algorithms and machine learning to analyze data from production facilities, distribution centers, and retail locations. Real-time analytics assess historical sales, weather patterns, and events to forecast demand, optimize inventory, and allocate resources efficiently.
- In warehouses, AI-driven automation, including computer vision and robotics, streamlines sorting, packing, and inventory tracking.
- AI optimizes delivery routes to reduce costs and emissions, while predictive maintenance utilizes AI-powered sensors to monitor vending machines and equipment, identifying issues before they lead to downtime. Additionally, AI evaluates supplier reliability, transportation costs, and geopolitical risks to optimize the sourcing of raw materials.
Intelligent Warehouse Layout & Space Optimization
Dynamically designing and continuously optimizing warehouse layouts for maximum efficiency, storage capacity, and operational flow.
How AI works:
- Dynamic Storage Layout Optimization: AI can reconfigure warehouse storage layouts in real-time based on demand fluctuations, inventory patterns, and product characteristics, enabling more efficient use of storage space. This ensures that high-demand items are placed in easily accessible locations, minimizing picking times and travel distances.
- Predictive Analytics for Inventory Placement: By analyzing historical sales data, seasonal trends, and external factors such as weather or marketing campaigns, AI can accurately forecast demand for specific products. Predictive Analytics in manufacturing enables businesses to strategically position popular items closer to shipping or packing areas, thereby reducing the time it takes for workers to travel and enhancing the speed of order fulfillment.
- Optimal Picking Route Generation: AI algorithms can analyze product placement, order priorities, and real-time aisle congestion to generate the most efficient picking routes for both human workers and autonomous mobile robots (AMRs). This minimizes unnecessary movement and maximizes the number of orders fulfilled per shift.
- Space Utilization Maximization: AI-driven tools analyze storage needs, product dimensions, and turnover rates to recommend optimal shelving configurations and storage strategies, including the effective use of vertical space. This prevents wasted space and allows for higher inventory volume.
- Simulations and Virtual Twins: Digital twins in Retail, allowing businesses to test the impact of different layout changes or operational strategies in a virtual environment before implementing them physically. This reduces risk and helps identify the most optimal designs.
Tangible Benefits For Businesses:
- Increased Storage Capacity Utilization: Maximizes every square foot of warehouse space, potentially delaying or avoiding costly expansions.
- Reduced Travel Time: Minimizes the distance warehouse personnel and Automated Guided Vehicles (AGVs) or Autonomous Mobile Robots (AMRs) need to travel, accelerating picking and putaway.
- Faster Order Fulfillment Cycles: Streamlined movement of goods directly contributes to quicker order processing and dispatch.
- Improved Safety: Optimized traffic flow and clear pathways reduce the risk of accidents.
Amazon: Robotics and Automation in Fulfillment Centers
Challenge: Amazon faced significant challenges in scaling its logistics operations to meet growing customer demand while maintaining efficiency and accuracy. Manual processes for inventory retrieval, sorting, and packing were time-consuming and prone to errors, particularly during peak periods such as Black Friday or the holiday season.
Solution: Amazon implemented a robust robotics and automation strategy to address these challenges:
- Robots and Autonomous Navigation: Deployed AI-powered robots for Robotic Process Automation (RPA) to automate inventory retrieval, using advanced sensors and mapping algorithms to navigate warehouses efficiently and reduce human effort in repetitive tasks.
- AI-Driven Sortation Systems: Introduced automated sortation systems to organize packages by destination and shipping method, streamlining last-mile logistics.
- Automated Quality Checks: Integrated computer vision and AI to perform real-time quality assurance, identifying damaged or mislabeled items to minimize errors.
- Dynamic Resource Allocation: Utilized AI algorithms to dynamically assign tasks between robots and human workers, optimizing workflows based on demand.
- Collaborative Robots (Cobots): Developed cobots to work safely alongside human employees, addressing safety concerns and creating new roles for system oversight and maintenance.
Results: The integration of robotics and automation yielded significant benefits for Amazon and its customers:
- Increased Efficiency: Robots and AI-driven systems reduced order processing times, enabling same-day and next-day deliveries, even during peak demand periods.
- Cost Reduction: Automation decreased reliance on manual labor for repetitive tasks, lowering operational costs and allowing Amazon to scale its logistics network efficiently.
- Improved Accuracy: Automated quality checks and sortation systems minimized errors, ensuring that customers received accurate and undamaged orders, which boosted satisfaction and loyalty. (Source: Amazon)
Predictive Maintenance for Warehouse Equipment
AI in manufacturing anticipates and prevents critical equipment breakdowns (e.g., forklifts, conveyors, sorting machines, robotic systems) before they lead to costly downtime.
How AI works:
- AI leverages data collected from an array of sensors integrated into warehouse machinery. These sensors monitor various parameters, including vibration, temperature, pressure, motor performance, energy consumption, and operating hours.
- Machine learning models continuously analyze this real-time data, comparing it against historical performance benchmarks and known failure signatures.
- When anomalies or subtle deviations indicating potential wear and tear are detected, the AI system triggers automated maintenance alerts or schedules proactive servicing. This shifts maintenance from a reactive “fix-it-when-it-breaks” approach to a proactive, “prevent-it-before-it-breaks” strategy.
Tangible Benefits For Businesses:
- Reduced Downtime and Operational Disruptions: Prevents unexpected equipment failures that halt operations, ensuring continuous workflow.
- Lower Maintenance Costs: Transitioning from costly emergency repairs and parts replacement to scheduled, efficient, and targeted maintenance results in significant savings.
- Extended Lifespan of Assets: Proactive care prolongs the operational life of expensive warehouse machinery.
- Improved Safety: Malfunctioning equipment can pose a significant safety hazard; predictive maintenance helps mitigate this risk.
Real Example: DHL and Automated Warehouse Systems
DHL’s vast network of sorting centers and warehouses relies heavily on complex automated systems, including miles of conveyor belts, high-speed sorters, and robotic arms, to process millions of parcels daily.
DHL invested in an AI-powered predictive maintenance solution for its core automated warehouse equipment, with a particular focus on conveyor belts and sorting machinery. The solution involved:
Sensor Deployment:
- Vibration Sensors: Monitor motors, bearings, and conveyor rollers for changes in vibration patterns indicating wear, misalignment, or potential failure.
- Temperature Sensors: Monitor the temperatures of motors, gearboxes, and electrical components to detect potential overheating.
- Current Sensors: Measure motor electrical current draw to identify increased resistance or strain.
- Acoustic Sensors: Detect unusual noises (e.g., grinding, squealing) signaling mechanical issues.
- Vision Systems: Use cameras for visual inspection of components to identify wear, cracks, or damage.
Real-time Data Integration: Streams data from thousands of sensors across warehouses to a central platform, combining it with historical maintenance records, equipment specs, and operational data (e.g., throughput, peak hours).
Bonus Read: What is Data Integration & Why Does it Matter to Your Business?
Machine Learning Models:
- Anomaly Detection: Trained to recognize normal equipment operation; deviations trigger alerts.
- Failure Prediction: Supervised models predict specific failure modes (e.g., bearing failure, belt tear) by utilizing historical sensor data to inform their predictions.
- Remaining Useful Life (RUL) Estimation: Estimates the lifespan of a component for optimized maintenance scheduling.
- Proactive Alerting & Workflow: Automatically generates alerts with diagnostic info and recommended actions, integrating with DHL’s CMMS to create work orders and schedule technicians.
Results: By predicting failures weeks or even months in advance, DHL could schedule maintenance during planned downtime (e.g., overnight, weekends) or during periods of low activity, virtually eliminating sudden, costly breakdowns.
We estimate that up to 30% of our global material-handling equipment fleet will use some form of robotic automation by 2030.
Markus Voss, Global CIO & COO at DHL Supply Chain
Autonomous Picking & Packing
The intersection of IoT and robotics is automating the complex processes of identifying, retrieving, and preparing items for shipment with high speed and accuracy.
How AI works:
- AI is the brain behind advanced robotic systems, including robotic arms and Autonomous Mobile Robots (AMRs). For picking, computer vision and deep learning algorithms enable robots to accurately identify specific items, regardless of their orientation or position on shelves.
- These robots can then grasp a diverse range of products with varying shapes, sizes, and fragility using specialized grippers. For packing, AI optimizes the choice of packaging materials, carton size, and item arrangement within the package to minimize space and material usage while ensuring product safety. AMRs, guided by AI, navigate the warehouse floor, dynamically calculating the most efficient paths to transport picked items to packing stations or directly to shipping, adapting to real-time obstacles and changes.
Tangible Benefits For Businesses:
- Significant Increase in Speed and Accuracy: Robots can operate continuously and with higher precision than humans, especially for repetitive tasks.
- Reduced Labor Costs and Dependency: Frees human workers from mundane, physically demanding tasks, allowing them to focus on more complex or strategic roles.
- Ability to Operate 24/7: Automation enables continuous operations, even during off-peak hours or labor shortages, ensuring uninterrupted service.
- Reduced Errors and Damages: AI-driven precision minimizes mispicks and product damage during handling.
Real Example: Amazon Deploys AI-Powered Robots
Amazon deploys AI-powered robots in two sets. The first set of robots will move to the location, search for products, pick them up, and pass them on to the packing stations. At the same time, another set of robots will pack orders and ensure they are delivered to the correct truck.
Product Retrieval and Transfer
This first set of robots focuses on retrieving the correct products from storage and delivering them to the packing stations.
- Movement and Navigation: Amazon Robotics drive units, such as Hercules and Titan, move around the vast warehouse floors. They don’t just wander aimlessly; they are guided by sophisticated AI algorithms that determine the most efficient routes and coordinate their movements to avoid collisions and congestion.
- Searching and Picking: These robots often carry “pods” or mobile shelves filled with various products. When an order comes in, the AI system identifies which pod contains the required item. The robot then travels to that pod, lifts it, and transports it to a designated workstation.
- Passing to Packing Stations: At these workstations, other robotic arms use computer vision and AI to identify and precisely pick individual items from the pods. For example, Vulcan features a “sense of touch” with force feedback sensors, allowing it to handle delicate items without damage. These picked items are then placed into totes or conveyor belts to be moved to the next stage: packing.
Order Packing and Delivery Preparation
The second set of robots takes over once the individual items for an order have been picked.
- Packing Orders: This involves robots and automated systems that can
- Sort packages: Robots like Robin sort packages by destination or size.
- Optimize packaging: AI algorithms analyze the dimensions and fragility of items to determine the most suitable and sustainable packaging, minimizing waste and ensuring product safety. Some automated systems can even custom-build paper bags or boxes to fit individual orders.
- Apply labels: Automated systems, including SLAM (Scanning, Labeling, and Manifesting) lines, scan the items, generate shipping labels with destination and tracking information, and apply them to the packages.
- Ensuring Correct Delivery to Trucks: Once packed and labeled, another set of robots is involved in staging and loading the items onto the trucks.
- Internal Transport: Robots like Proteus, Amazon’s fully autonomous mobile robot, can navigate open areas of the fulfillment center to move heavy carts filled with customer orders. They might work in tandem with other robotic systems, for instance, loading packages destined for the same zip code into specific carts.
- Loading Trucks: The AI system ensures that the correctly packed orders are directed to the right outbound docks and eventually loaded onto the corresponding delivery trucks. This is crucial for efficient last-mile delivery.
Route Optimization for Inbound & Outbound Logistics
Optimizing the most efficient internal routes for putaway and picking within the warehouse, as well as external routes for delivery vehicles.
How AI works:
AI in logistics considers a multitude of dynamic variables simultaneously for route planning.
- For internal logistics, AI analyzes the location of incoming goods, optimal storage slots, picking order sequences, warehouse traffic, and equipment availability to generate the most efficient putaway and picking paths.
- For outbound logistics, AI processes real-time data, including traffic conditions, weather, delivery windows, vehicle capacity, order urgency, and delivery locations. Using sophisticated algorithms (like genetic algorithms or deep reinforcement learning), AI generates the shortest, fastest, and most fuel-efficient routes, dynamically adjusting to real-time disruptions or new orders, ensuring seamless flow from warehouse to customer.
Tangible Benefits For Businesses:
- Reduced Transportation Costs: Optimized routes result in lower fuel consumption and reduced vehicle wear and tear.
- Faster Delivery Times: Efficient routing accelerates both internal movement and external last-mile delivery.
- Improved Productivity: Maximizes the number of deliveries or picks per shift.
- Reduced Carbon Footprint: Driving fewer miles translates to lower emissions.
Real Example: Tata Steel – Inbound & Outbound Logistics
Challenge: Tata Steel faced issues such as poor visibility of in-plant operations, resulting in loading delays, traffic congestion, and parking problems for trucks. In-transit challenges included overspeeding, route diversions, theft, and unexpected stoppages, resulting in high transportation costs and delayed deliveries of both raw materials and finished goods.
Solution: Tata Steel leveraged an AI-powered predictive logistics platform for:
- Real-time visibility: Leveraging IoT devices and sensors for 100% visibility of in-plant and in-transit transportation.
- AI-based auto-allocation: Automatically allocating orders to transporters when their engines are running.
- Predictive analytics: Machine learning algorithms analyze historical data to identify the best routes and accurately predict delivery ETAs (Estimated Time of Arrival) – whether early, on time, or delayed.
- Automated compliance checks: Digital checks of vehicle details are performed before entry into the plant, restricting the entry of non-compliant vehicles.
- End-to-end tracking: Real-time tracking capabilities provide a 360-degree view of shipments.
Result: It improved on-time delivery by proactively identifying and mitigating potential delays. (Source: Analytics India Mag)
Quality Control & Damage Detection
Automatically inspecting incoming goods, goods in storage, and outgoing shipments for defects, damage, or inconsistencies.
How AI works:
- Computer vision systems in logistics, equipped with high-resolution cameras, are deployed at various inspection points (e.g., receiving docks, packing stations, shipping lanes).
- Machine learning and deep learning models are trained on vast datasets of images, including examples of perfect products and various types of defects (such as scratches, dents, mislabeling, packaging damage, and missing components).
- The AI system can rapidly scan items, detect even minute flaws that the human eye might miss, compare products against specifications, and flag discrepancies or damaged goods in real-time, often before they are even stored or shipped.
As a form of Physical AI, these systems combine visual perception and intelligent action to ensure quality control in high-speed, real-world environments.
Tangible Benefits For Businesses:
- Reduced Returns and Customer Complaints: Prevents damaged or incorrect products from reaching customers, enhancing satisfaction.
- Improved Product Quality: Ensures only high-quality items proceed through the supply chain.
- Faster Identification of Issues: Enables quick corrective actions, minimizing downstream impacts.
- Reduced Manual Inspection Labor: Frees up human resources from repetitive, visually taxing inspection tasks.
Real Example: BMW’s AI-Powered Visual Inspection Systems
Challenge: Traditionally, inspecting car body panels and components for defects, such as scratches, dents, and paint imperfections, has relied heavily on human inspectors, who are prone to errors and inconsistencies.
Solution: BMW deployed high-resolution cameras to capture detailed images of car parts in real-time. AI algorithms, specifically machine learning models, are trained on vast datasets of images to identify and differentiate between acceptable and defective parts. This system can detect even minute surface defects with greater precision than manual inspections.
Result: This AI integration has led to improved defect detection rates, reduced false positives (minimizing unnecessary rework), and ultimately enhanced product quality with lower rework costs in BMW’s manufacturing processes. (Source: BMW Group)
Appinventiv: Your Best AI Partner to Automate Your Warehouse Management System
The modern warehouse is a dynamic, complex ecosystem, often stretched to its limits by soaring customer expectations, fragmented supply chains, and the relentless demand for speed and accuracy. Many enterprises find themselves trapped in a cycle of manual errors, inefficient inventory management, and reactive decision-making, resulting in significant cost overruns and missed growth opportunities.
AI is not just an incremental improvement; it’s a paradigm shift that allows warehouses to move from operational challenges to strategic assets. However, harnessing the full power of AI requires more than just off-the-shelf solutions. It demands a partner with deep expertise, a proven track record, and a holistic approach to integrating AI into the very fabric of your warehouse operations.
This is where Appinventiv distinguishes itself as an ideal AI partner for automating your Warehouse Management System (WMS).
How Appinventiv Automates Your Warehouse Management with AI?
Our expertise translates directly into automating and optimizing the critical aspects of your warehouse management system, addressing key pain points:
AI-Powered Demand Forecasting and Inventory Optimization
We develop artificial intelligence warehouse management models that analyze extensive datasets, including historical sales, market trends, promotional data, seasonality, and external factors, to predict demand with remarkable accuracy. This enables their developed WMS to:
- Prevent Stockouts & Overstocking: Ensure optimal inventory levels, reduce carrying costs, and maximize product availability.
- Dynamic Reordering: Automating purchase orders based on real-time data and predictive insights, improving cash flow.
- Waste Reduction: Identifying slow-moving or obsolete inventory early and minimizing losses.
Intelligent Warehouse Layout and Slotting
Leveraging AI in warehouse management, we help design WMS functionalities that dynamically optimize your warehouse layout. Our solutions can:
- Minimize Travel Time: Algorithms analyze picking patterns and product popularity to strategically place items, thereby reducing travel distances for both pickers and robots.
- Maximize Space Utilization: Optimizing storage density and flow to make the most of existing warehouse space, potentially delaying or avoiding costly physical expansions.
- Adaptive Layouts: Enabling the WMS to suggest micro-adjustments to item placement based on changing demand or product characteristics.
Autonomous Operations with Robotics and Computer Vision
We integrate cutting-edge AI-powered robotics and computer vision systems into your WMS for automation of core tasks:
- Automated Picking & Putaway: Implementing AI-driven Autonomous Mobile Robots (AMRs) and robotic arms for precise and rapid handling of goods, reducing reliance on manual labor for repetitive tasks.
- Real-time Inventory Tracking: Utilizing computer vision and IoT sensors for highly accurate, real-time inventory counts, significantly reducing manual cycle counting efforts and errors.
- Automated Quality Control: Deploying AI vision systems to inspect incoming and outgoing goods for defects, damage, or mislabeling, ensuring only high-quality products proceed through the supply chain.
Predictive Maintenance for Equipment
Through IoT-AI integration, we build solutions that prevent costly equipment downtime. Their WMS enhancements can:
- Monitor Equipment Health: Collect data from sensors on forklifts, conveyors, and sorting machines (vibration, temperature, performance metrics).
- Predict Failures: AI algorithms analyze this data to identify anomalies and predict potential breakdowns before they occur.
- Automate Maintenance Scheduling: Triggering proactive maintenance alerts and scheduling repairs, minimizing operational disruptions, and extending asset lifespan.
Optimized Logistics and Route Planning
Appinventiv develops AI modules for your WMS that optimize both internal and external logistics:
- Intelligent Internal Routing: Guiding pickers and robots along the most efficient paths within the warehouse for putaway and retrieval.
- Dynamic Delivery Route Optimization: For outbound logistics, AI considers traffic, weather, delivery windows, and vehicle capacity to generate the most efficient routes, reducing fuel costs and delivery times.
- Real-time Adaptability: Solutions can dynamically re-optimize routes in response to unforeseen events or new orders, ensuring optimal performance.
Why Appinventiv Stands Out in AI-Powered Warehouse Automation?
Appinventiv isn’t just another software development company; it is a digital transformation agency with a strong focus on cutting-edge technologies, including AI, Machine Learning (ML), and IoT. Their AI development services for warehouse automation are rooted in a comprehensive understanding of enterprise-level challenges and a commitment to delivering tangible ROI.
- Our dedicated team of certified AI and ML experts possesses specialized knowledge in developing and deploying complex AI models for diverse industrial applications, including logistics and supply chain.
- With a history of delivering over 3,000 solutions and mastering more than 35 industries, we have a proven track record of successfully implementing digital transformation initiatives, including those involving advanced AI.
- Our high client satisfaction ratings on platforms like Clutch, combined with transparent development processes and a commitment to data security and compliance (including GDPR and HIPAA), build strong trust with our partners.
Partnering for a Smarter Warehouse Future
For enterprises struggling with the complexities of warehouse management, AI-powered Retail Software Development Services offer a clear path to unprecedented efficiency and growth. However, the journey to an AI-automated warehouse requires a strategic partner with the technical prowess and industry insight to deliver tangible results.
FAQs
Q. How is AI used in inventory warehouse management?
A. AI is used in inventory warehouse management to optimize operations and improve efficiency. It powers demand forecasting by analyzing historical data and market trends to accurately predict inventory needs. AI-driven systems automate inventory tracking using technologies like RFID and computer vision to monitor stock levels in real-time.
AI also enhances warehouse robotics, enabling automated tasks such as picking, packing, and sorting. Additionally, AI optimizes warehouse layouts and picking routes to minimize travel time and costs. It can detect anomalies, such as stock discrepancies, and improve supply chain coordination by integrating data across systems.
Q. Which is the best AI for warehouse management?
A. There isn’t a single “best” AI solution for warehouse management, as it depends on specific needs, budget, and warehouse scale. However, leading solutions include those from companies such as Blue Yonder, Manhattan Associates, and SAP, which offer AI in warehouse management systems (WMS) with features like predictive analytics, integration with automation, and real-time inventory tracking.
Cloud-based platforms, such as Locus Robotics and GreyOrange, are also popular for their AI-driven robotics and scalability. The best choice aligns with your warehouse’s size, complexity, and integration requirements—evaluating demos and case studies is key.
Q. What are the applications of AI in warehouse management?
A. AI applications in warehouse management include:
- Demand Forecasting: Predicting stock requirements using historical and real-time data.
- Inventory Optimization: Automating stock replenishment and reducing overstock or stockouts.
- Robotics and Automation: Powering robots for picking, packing, and moving goods.
- Route Optimization: Determining efficient picking paths to reduce time and labor costs.
- Real-Time Tracking: Using AI with IoT or computer vision for accurate inventory monitoring.
- Anomaly Detection: Identifying errors like misplaced items or theft.
- Warehouse Layout Planning: Optimizing space utilization based on data analysis.
- Supply Chain Integration: Enhancing coordination with suppliers and logistics partners.
Q. What are the key features of AI warehouse management for business systems?
A. Key features include real-time inventory tracking, predictive analytics for demand forecasting, automated picking and packing, route optimization for warehouse robots, and integration with supply chain systems for seamless operations.
Q. What role does AI play in warehouse management?
A. AI plays a transformative role in warehouse management by automating repetitive tasks, improving decision-making, and enhancing operational efficiency. It analyzes large datasets to forecast demand, optimize inventory levels, and streamline workflows.
AI enables real-time monitoring and error detection, thereby reducing the need for manual oversight and intervention. It powers autonomous robots and vehicles for faster, safer material handling. By optimizing routes and layouts, AI cuts costs and boosts productivity. Ultimately, AI drives smarter, data-driven operations, enabling warehouses to adapt to dynamic market demands.
Q. Can AI in warehousing integrate with existing systems?
A. Yes, AI in warehousing can integrate with existing warehouse management systems (WMS) and enterprise resource planning (ERP) software to enhance functionality and provide data-driven insights.
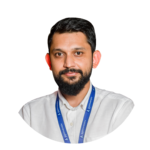
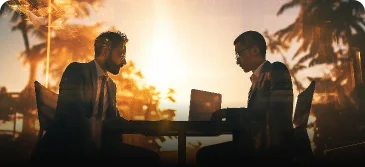
- In just 2 mins you will get a response
- Your idea is 100% protected by our Non Disclosure Agreement.
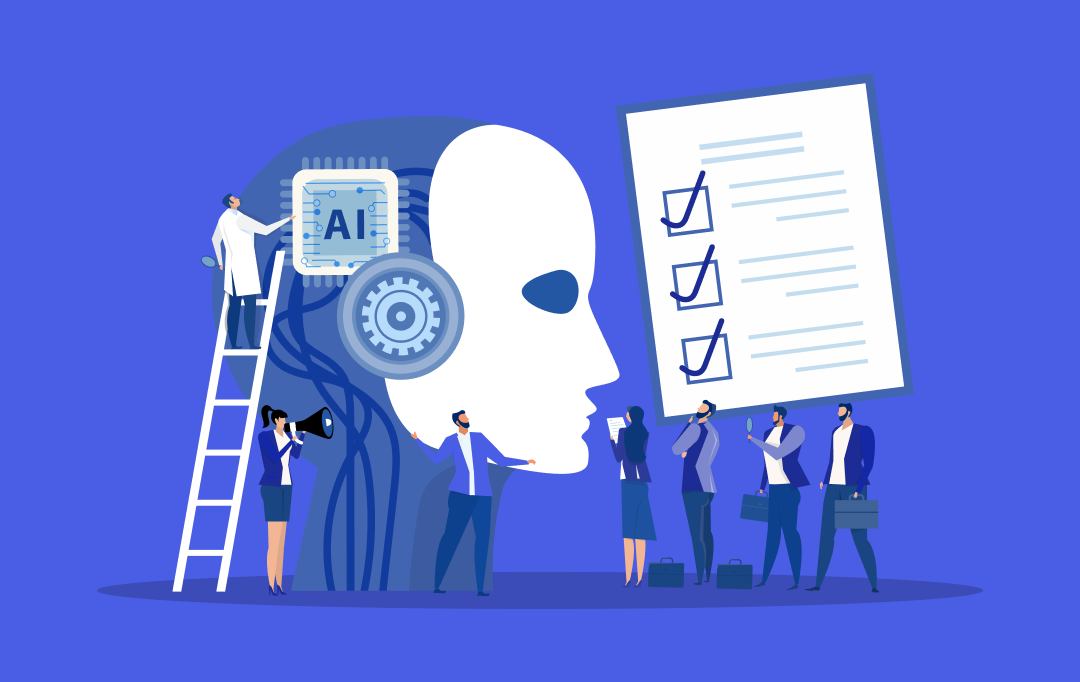
Key takeaways: Generative AI is a double-edged sword. It offers immense opportunities for growth and innovation. However, it also carries risks related to bias, security, and compliance Proactive governance is not optional. A responsible Generative AI deployment checklist helps leaders minimize risks and maximize trust. The checklist for Generative AI compliance assessment covers everything, including…
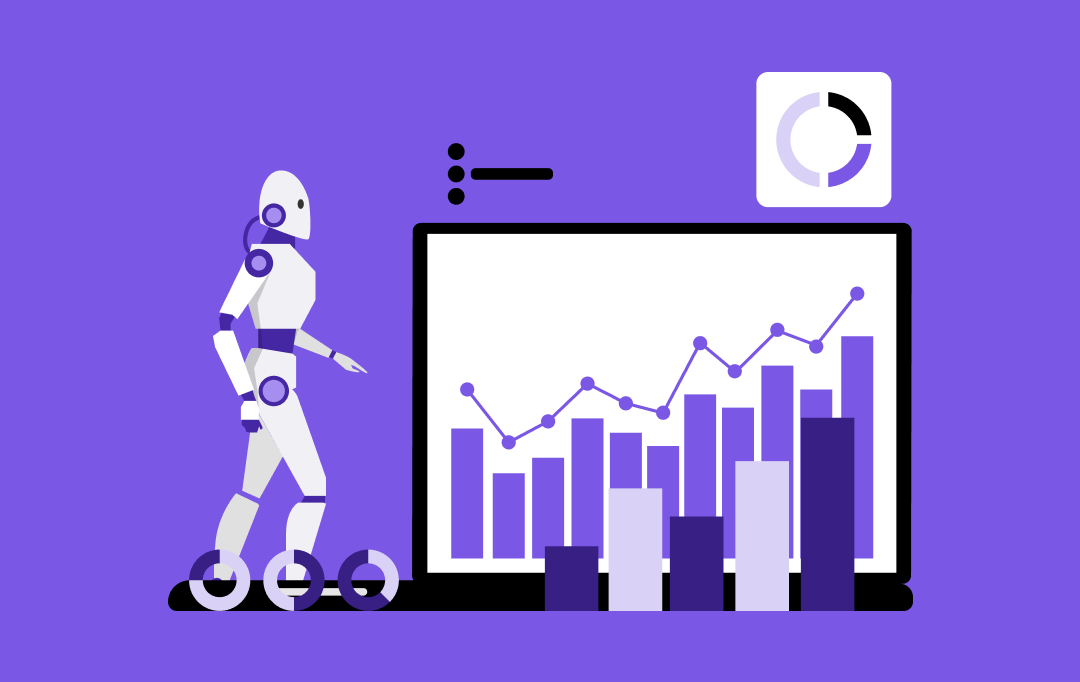
How to Scale Your AI Project without Overspending?
Key takeaways: Only 11% of enterprises have scaled AI successfully. Scaling AI improves productivity, predictions, and personalization. Major barriers include data silos, talent gaps, and rising costs. Governance and business alignment are critical for success. Real-world leaders like JPMorgan and Netflix showcase the impact. Generative AI scaling offers big rewards but carries higher risks. Scaling…
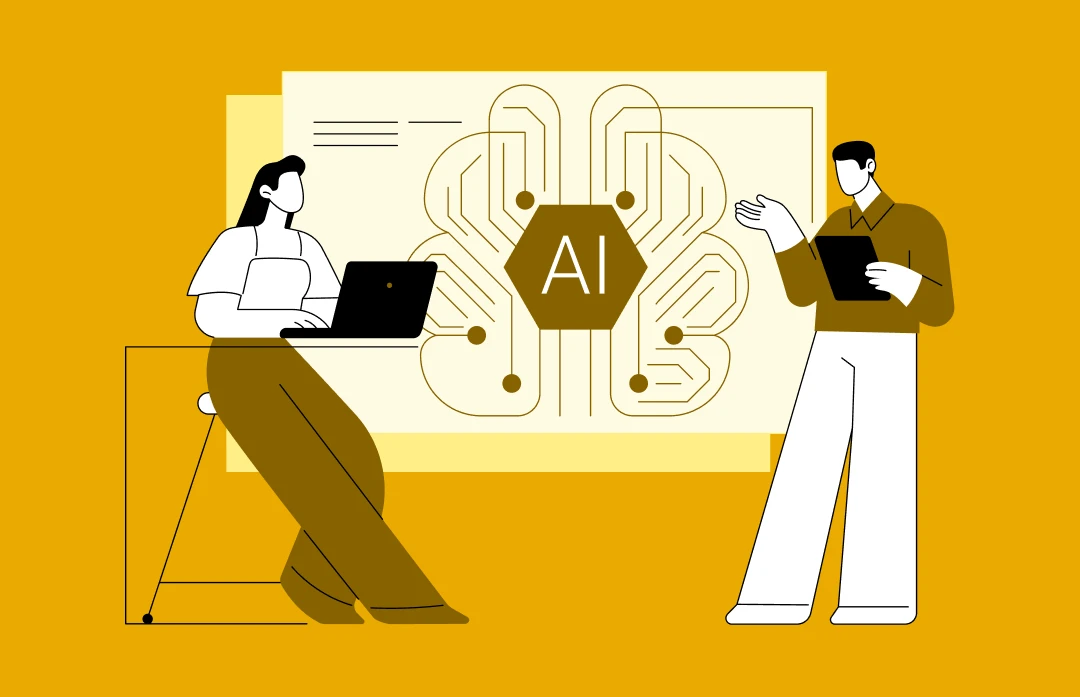
How to Reduce Bias in AI Models? Key Reasons to Understand and Mitigation Strategies to Follow
Key takeaways: Bias in AI isn't just a technical concern; it affects brand reputation, compliance, and customer trust, making it a boardroom priority. AI models reflect the data they're trained on, and even small biases in training data can lead to systemic issues in decision-making, hiring, and more. Bias in AI systems can lead to…