- Factors Affecting the Cost of Automotive Supply Chain Software Development
- Complexity of Requirements
- Integration with Existing Systems
- Technology Stack
- Scope of Customization
- Project Timeline
- Size of Software Development Team
- Compliance and Security
- Maintenance and Support
- Location of Development Team
- Benefits of Automotive Supply Chain Software Development
- Better Data Management
- Improved User Experience
- Integration Capabilities
- Adaptability to Industry Changes
- Real-time Data and Analytics
- Enhanced Vendor Management
- Greater Visibility across the Supply Chain
- Streamlined Communication and Coordination
- Improved Compliance Management
- Reduced Operational Risk
- Automotive Supply Chain Software Development Use Cases
- Toyota's Inventory Management with JIT System
- BMW's Connected Supply Chain (CSC) Programme
- General Motors' Proactive Detection and Optimization in Automotive Manufacturing
- Volvo’s Comprehensive Supply Chain Risk Management Strategy
- Automotive Supply Chain Software Development Process
- Discovery and Requirement Definition
- Blueprint and Strategic Planning
- Development and Feature Implementation
- Rigorous Testing and Validation
- Seamless Deployment and Onboarding
- Ongoing Enhancement and Adaptation
- Overcoming Automotive Supply Chain Challenges with Solutions
- Lack of Agility and Resilience
- EV Supply Chain Issues
- Cybersecurity Threats
- Supply Chain Integration
- Accelerate Your Automotive Supply Chain Success with Appinventiv’s Expertise
- FAQs
As innovation in the automotive industry becomes mainstream, supply chain emerges as both a critical challenge and a key strategic asset. Automotive supply chain software development is revolutionizing how manufacturers and suppliers navigate this complex ecosystem. Integrated with advanced technologies, software development transforms the traditional supply chain, providing real-time insights, predictive analytics, and seamless automation.
As the automotive industry races towards new technological frontiers and faces ever-tightening competition, advanced supply chain software is not just a tool but a competitive differentiator. It’s the linchpin for turning potential disruptions into opportunities and maintaining a commanding edge in a market driven by rapid change and high expectations.
This has led auto manufacturers to consider investing in developing advanced automotive supply chain solutions that can optimize operations, enhance efficiency, and ensure seamless integration across the supply chain. However, the cost to build automotive supply chain software remains a significant concern. The automotive supply chain software development cost typically ranges from $50,000 to $400,000 or more, depending on factors such as the complexity of the system, the scale of implementation, the technology stack used, and the level of customization required.
As the market grows and evolves, these automotive supply chain software solutions offer substantial advantages, including reduced operational costs, improved accuracy, and faster response times. These advancements are influencing the future dynamics of the automotive supply chain by enabling companies to stay ahead in a rapidly changing industry.
In this blog, we will delve into how automotive supply chain software functions, the factors influencing its cost, its benefits, the development process, and the challenges associated with its adoption. Let’s move ahead.
Factors Affecting the Cost of Automotive Supply Chain Software Development
The automotive supply chain software development cost can be affected by multiple factors like the complexity of the supply chain processes, the level of customization required, and the scale of integration with existing systems. Additionally, the costs may vary based on the software provider’s reputation, support services, and any additional features or modules needed. Let’s have a detailed look at those.
Complexity of Requirements
The automotive supply chain software development cost is heavily influenced by the complexity of the requirements. When a business has intricate supply chain processes, such as multi-tiered supplier networks, complex logistics, or specialized workflows, the software needs to be tailored to accommodate these complexities.
This customization involves extensive development work to ensure that the software meets specific business needs. The more complex the requirements, the higher the development effort and cost, as it demands specialized knowledge, additional coding, and thorough testing to ensure functionality and reliability.
Integration with Existing Systems
Integrating new automotive supply chain software with existing systems, such as ERP, CRM, or inventory management platforms, is a major cost factor. The complexity of these integrations, including data migration, API development, and ensuring compatibility between systems, can affect the cost to build automotive supply chain software.
Custom integration work demands additional development resources and time to ensure seamless data exchange and operational harmony across different platforms. The need for robust and error-free integration can drive up the automotive supply chain software development costs due to the necessity of thorough testing and troubleshooting.
Technology Stack
The technology stack chosen for developing automotive supply chain software plays a crucial role in determining the overall development costs. Advanced technologies, including blockchain, artificial intelligence, machine learning, and Internet of Things (IoT) integration, often require specialized tools and expertise.
These technologies can enhance functionality and performance but also add to the development cost due to the need for cutting-edge infrastructure, advanced security measures, and additional development time. The selection of scalable technologies contributes to a higher total cost of developing automobile industry supply chain management software.
Scope of Customization
The extent to which the software must be customized for the specific needs of the automotive supply chain significantly impacts its cost. Off-the-shelf solutions may provide basic functionality, but custom automotive supply chain software development often requires extensive modifications to align with unique business processes and workflows.
This level of customization involves creating bespoke features, interfaces, and reports, all of which add to the development time and cost. Tailored automotive supply chain solutions also require ongoing adjustments and support, contributing to higher overall expenses compared to more standardized options.
Project Timeline
The timeline for completing the automotive supply chain software development project also affects the overall cost. Shorter project timelines often necessitate additional resources, expedited development, and potentially higher costs due to the need for faster turnaround and increased project management efforts.
Conversely, extending the timeline may lead to prolonged development costs and ongoing resource allocation. Balancing the project timeline with automotive supply chain software development cost considerations is crucial for managing overall expenses and ensuring that the software meets the desired goals.
Size of Software Development Team
The size of the software development team plays an integral role in shaping the overall cost to develop automotive supply chain software. A larger team can lead to higher upfront costs due to increased labor expenses, but it often results in faster development and quicker project completion by allowing parallel work on different tasks.
With a diverse group of specialists, the software benefits from a series of skills and expertise, enhancing its quality and effectiveness. Although a bigger team can drive up initial costs, it can potentially reduce long-term expenses by minimizing delays and errors. Balancing the team size with the project’s requirements is essential for achieving the best cost-effectiveness and quality.
Compliance and Security
Ensuring the software meets industry regulations and has strong security measures can add to the custom automotive supply chain software development. Compliance with standards such as ISO or GDPR requires extra development, validation, and testing.
Advanced security features of automotive supply chain software, like encryption and access controls, also contribute to the overall cost. Investing in compliance and security upfront helps avoid potential issues down the line but adds to the initial expense.
Maintenance and Support
Ongoing maintenance and support are crucial and overall impact the automotive supply chain software development cost. Custom software needs regular updates, bug fixes, and technical support to keep it running smoothly. Maintaining and supporting the software over its lifecycle ensures it remains effective but will add to your overall expenditure.
As technology evolves and business needs shift, future enhancements may be required, potentially affecting the overall cost. Investing in comprehensive maintenance and support services helps avoid potential disruptions and ensures long-term functionality and performance.
Location of Development Team
The location of the development team significantly impacts the cost of automotive supply chain software development. Hiring software development outsourcing services from India can offer substantial cost advantages due to its access to a large, highly skilled talent pool. India is renowned for its expertise in technology and software development, providing high-quality software solutions.
Also, development teams from Asian countries are often experienced with global projects and adept at working across different time zones, ensuring flexibility and responsiveness. Leveraging Indian developers allows companies to get access with exceptional talent, making it an attractive option for optimizing automotive supply chain software development costs.
Also Read: How to Hire a Dedicated Development Team?
Benefits of Automotive Supply Chain Software Development
The automotive supply chain software development comes with a host of advantages that enhance visibility, streamline operations, and improve efficiency throughout the automotive supply chain. Let’s have a quick look at those.
Better Data Management
The automobile industry supply chain management software enhances data management by centralizing information from multiple sources into a single, accessible system. This centralized approach improves data accuracy and accessibility, providing a detailed overview of the supply chain. Effective data management supports better planning, execution, and optimization of supply chain activities, leading to more informed and strategic decisions.
Improved User Experience
Focusing on user experience during custom automotive supply chain software development results in more intuitive and user-friendly interfaces. Custom solutions enable the creation of interfaces that are tailored to the needs and workflows of supply chain managers and other users. By incorporating stakeholder or user feedback throughout the development process, it is possible to make continuous improvements that enhance usability and reduce the learning curve.
Integration Capabilities
Effective integration is a key advantage of custom automotive supply chain software. It can be designed to seamlessly connect with existing ERP systems, CRM tools, and other enterprise applications, ensuring a unified operation across various platforms. This seamless integration ensures that all elements of the automotive supply chain process work together efficiently and accurately.
Adaptability to Industry Changes
The automotive industry frequently faces changes in regulations and market dynamics. Customized supply chain software offers the flexibility needed to adapt to these changes efficiently. Businesses can update the software to comply with new regulations and industry standards, keeping their operations streamlined. Additionally, it allows businesses to quickly respond to emerging market trends and technological advancements, ensuring they remain agile in a rapidly evolving industry.
Real-time Data and Analytics
Developing bespoke automotive supply chain software provides the advantage of real-time visibility into critical supply chain components. The custom solution enables tracking inventory levels, production statuses, and shipment progress as they happen, enhancing decision-making and responsiveness. It also helps automotive companies to identify trends, forecast demand accurately, and optimize their operations for better outcomes.
Enhanced Vendor Management
Custom software enhances vendor management by offering tools for tracking performance, automating compliance checks, and streamlining procurement. These features improve oversight, leading to better supplier reliability and optimized procurement strategies. By automating routine tasks, the software also reduces manual errors and administrative overhead, further improving vendor interactions.
Greater Visibility across the Supply Chain
Custom software enhances supply chain visibility by providing comprehensive tracking and real-time updates on all activities. This improved visibility allows businesses to monitor operations more effectively, identify issues quickly, and improve coordination. Enhanced visibility supports better decision-making and helps manage potential disruptions more proactively. It also improves transparency throughout the supply chain, benefiting all stakeholders involved.
Streamlined Communication and Coordination
Custom automotive supply chain solutions also improve communication and coordination with features like integrated messaging systems and real-time notifications. It ensures that all stakeholders stay aligned and reduce the risk of misunderstandings. Streamlined communication fosters better collaboration across the supply chain, enhancing overall operational efficiency.
Improved Compliance Management
Custom automotive software includes features for managing compliance with industry regulations, such as automated reporting and regulatory updates. These capabilities help ensure adherence to stringent automotive standards and reduce the risk of regulatory breaches. Effective compliance management avoids potential fines and legal issues while maintaining operational integrity, which even influences the automotive supply chain software development cost.
Reduced Operational Risk
Custom software includes features for risk management, such as exception alerts and scenario analysis tools. These capabilities help identify and mitigate operational risks, maintaining stability and minimizing disruptions. By proactively managing risks, the software ensures smoother operations and reduces the likelihood of significant issues. Effective risk management contributes to overall supply chain resilience and continuity.
Automotive Supply Chain Software Development Use Cases
There are numerous use cases of automotive supply chain software management that optimize inventory control, enhance supplier collaboration, and improve logistics and distribution processes. Let’s have a look at how few reputed automotive giants have utilized automotive supply chain management software for streamlining their processes.
Toyota’s Inventory Management with JIT System
Toyota utilizes its renowned Just-In-Time (JIT) system for efficient inventory management, focusing on reducing waste and lowering costs. The JIT approach ensures that components and materials arrive exactly when needed, minimizing excess inventory and storage expenses.
By integrating advanced inventory management software, Toyota aligns production schedules with supplier deliveries, boosting operational efficiency and responsiveness. This system enables Toyota to maintain a lean inventory while upholding high standards in manufacturing and supply chain management. The JIT system is a key factor in Toyota’s ability to manage its complex automotive supply chain effectively.
BMW’s Connected Supply Chain (CSC) Programme
BMW’s Connected Supply Chain (CSC) programme leverages real-time tracking systems to oversee the movement of parts and vehicles across its global supply network. This advanced technology enhances supply chain visibility, allowing BMW to swiftly address disruptions and optimize efficiency.
The CSC programme updates material controllers and logistics specialists every 15 minutes on the location and estimated delivery time of goods. This high level of transparency enables prompt responses to potential delays, helping BMW avoid costly emergency measures and maintain smooth operations.
General Motors’ Proactive Detection and Optimization in Automotive Manufacturing
General Motors utilizes predictive analytics with its proprietary AI system to better forecast demand and streamline supply chain operations. By examining historical data and market trends, GM can anticipate future requirements and adjust its production and procurement strategies.
Through AI-driven predictive analytics, GM’s manufacturing teams refine vehicle production by analyzing both historical performance and real-time data from robotics and conveyor systems. The AI system identifies unusual patterns that might indicate potential issues, allowing for early intervention to prevent unexpected downtimes and ensure an uninterrupted automotive supply chain.
Volvo’s Comprehensive Supply Chain Risk Management Strategy
Volvo Cars utilizes a thorough approach to manage supply chain risks and promote sustainability. With a global supplier base of around 8,300, Volvo applies the Responsible Business Alliance Risk Tool to assess risks and focuses on due diligence through various sustainability audits.
The company conducts regular evaluations, such as the Volvo Cars Sustainability Questionnaire and Environmental Assessments, to ensure suppliers meet high sustainability standards. Volvo also promotes participation in the Carbon Disclosure Project and has a structured process to address any supply chain issues effectively. This proactive strategy helps Volvo maintain a robust and responsible automotive supply chain process.
Automotive Supply Chain Software Development Process
The automotive supply chain software development life cycle involves several key phases, each crucial for ensuring the software meets industry standards and integrates seamlessly with existing systems. Here’s a closer look.
Discovery and Requirement Definition
The automotive supply chain software development process starts with a thorough requirement gathering phase, where stakeholders are consulted to identify their specific needs and challenges in the automotive supply chain. A comprehensive analysis is performed to ensure that the software will address these needs and integrate effectively with existing systems and processes, setting a solid foundation for the project.
Blueprint and Strategic Planning
Once requirements are clear, the system design and planning phase begins. This stage involves creating detailed design documents, defining the system architecture, and planning user interfaces.
It also includes strategizing integration with current systems and hardware used in the automotive industry. Proper design and planning ensure that the software is not only functional and user-friendly but also scalable to accommodate future needs.
Development and Feature Implementation
In the development phase, the software is built according to the design specifications, where the development team focuses on coding and implementing features like real-time tracking, automated alerts, and data analytics. The implementation of advanced features can also add to the overall automotive supply chain software development cost.
This phase emphasizes creating a robust, efficient, and reliable system that aligns with the project’s requirements and effectively manages the complexities of the automotive supply chain.
Rigorous Testing and Validation
The software is subjected to thorough testing and quality assurance processes to confirm its functionality and adherence to performance standards. This involves integration testing, unit testing, and user acceptance testing to detect and address any bugs or issues.
Thorough testing helps ensure that the software is reliable, secure, and ready for real-world application, minimizing the risk of post-deployment issues.
Seamless Deployment and Onboarding
After successful testing, the software is deployed into the production environment. This phase includes installation, configuration, and integration of the software with existing systems. Additionally, comprehensive user training is provided to ensure that all users understand how to operate the software effectively. Smooth deployment and training are crucial for maximizing the software’s impact and ensuring a seamless transition.
Ongoing Enhancement and Adaptation
Post-deployment, the software enters an ongoing maintenance phase to address any issues that arise and implement necessary updates. This involves regular bug fixes, performance optimizations, and adaptations to new industry trends and technological advancements. Continuous improvement ensures that the software remains effective and relevant, continuously enhancing its capabilities to meet evolving supply chain demands.
Overcoming Automotive Supply Chain Challenges with Solutions
Businesses frequently encounter various challenges when implementing automotive supply chain software. However, with the right strategies and solutions, these obstacles can be effectively navigated. Let’s take a closer look at those.
Lack of Agility and Resilience
Many automotive supply chains are too rigid, struggling to adapt quickly to various disruptions such as natural disasters or sudden demand changes. This inflexibility can cause significant delays and inefficiencies in business processes.
Solution: Embracing advanced technologies like AI can help predict and manage disruptions more effectively. Adopting flexible supply chain models and developing backup plans also enhance resilience. Building strong relationships with multiple suppliers can further increase adaptability.
EV Supply Chain Issues
The rise of electric vehicles (EVs) comes with various challenges, including sourcing rare materials for batteries and managing the production of these specialized components.
Solution: Automakers can build diverse supplier networks to reduce dependency risks and explore vertical integration to gain more control over the supply chain. Additionally, researching alternative materials and enhancing battery recycling efforts can help stabilize supply and reduce costs.
Cybersecurity Threats
With increasing digitization in supply chains, cybersecurity threats have become a major concern. Cyberattacks can disrupt operations, steal sensitive information, and cause financial losses.
Solution: Implementing robust cybersecurity measures, including regular system updates, encryption, and access controls, is essential. Educating employees on cybersecurity best practices and performing regular security audits can effectively protect against potential threats.
Supply Chain Integration
Integrating different components of the supply chain, from suppliers to manufacturers to distributors, can be complex and fragmented. Poor integration can lead to data inconsistencies and inefficiencies.
Solution: Implementing integrated supply chain management systems can streamline operations and improve data flow across the supply chain.
Accelerate Your Automotive Supply Chain Success with Appinventiv’s Expertise
The automotive supply chain is constantly transforming, driven by advancements in technologies and increasing demand for efficiency and innovation. As supply chains become more complex, leveraging innovative solutions will be crucial for staying competitive.
Appinventiv, being an industry leader in automotive supply chain software development services, is at the forefront of this transformation, having successfully executed a range of automotive projects. For instance, we developed Moo, an e-scooter app that bagged a Series A funding; ActiDrive, a gesture-recognition app using optical technology to enable touch-free control, ensuring driver safety and convenience; TrackMyShuttle, a real-time shuttle tracking system; and Visitor Parking Platform, which optimizes parking management.
As a leading automotive software development company, we bring extensive expertise to the table, specializing in innovative software solutions that transform and streamline automotive supply chains. Our team is dedicated to understanding your specific needs and delivering solutions that drive efficiency, enhance functionality, and position you at the edge of the automotive industry.
Partner with a dedicated software development company like ours and leverage our deep industry knowledge and technical skills. Our experts will also share the precise automotive supply chain software development cost estimation per your project needs and help you confidently and precisely navigate the future of automotive technology.
FAQs
Q. How much does it cost to develop an automotive supply chain software?
A. Developing automotive supply chain software can range from $50,000 to $400,000, depending on the project’s scope and complexity. Key factors influencing cost include the degree of customization, the technology stack used, and the extent of integration with existing systems.
Additionally, ongoing maintenance, support, and potential scalability features can impact the total expenditure. For an accurate automotive supply chain software development cost estimate tailored to your specific needs, it’s best to consult with our software development experts and get a detailed proposal.
Q. How long does it take to develop an automotive supply chain software?
A. Developing automotive supply chain software typically takes between 6 to 18 months. The timeline depends on the project’s complexity, level of customization, and integration needs. A larger or more complex system will require more time for design, development, and testing. Additionally, integrating with existing systems and ensuring robust testing can extend the timeline. To know more about the timeline, get in touch with a top-rated software development company in Sydney.
Q. What are some of the top automotive supply chain trends?
A. Here are some of the vital automotive supply chain trends to watch for:
Greater accountability: There’s an increasing push for greater supply chain visibility, with technologies like blockchain being implemented to track products and enhance accountability, reducing fraud.
Eco-Friendly Measures: The automotive industry is embracing eco-friendly practices, such as lowering emissions, using sustainable materials, and enhancing energy efficiency to cut environmental impact and adhere to regulations.
Reshoring: To minimize reliance on international suppliers and mitigate risks, companies are relocating manufacturing and supply chain operations back to their home countries.
Autonomous Vehicles: Advances in AI in automotive and sensor technology are driving the development of self-driving cars, which aim to improve transportation safety, efficiency, and convenience.
Q. How does automotive supply chain management work?
A. Managing an automotive supply chain involves a series of critical steps to ensure vehicles are built efficiently and meet high-quality standards. From sourcing raw materials to acquiring the finished product to dealerships, each stage plays a vital role. Here’s how the process works:
1. Sourcing Raw Materials: The supply chain kicks off with sourcing raw materials like aluminum, plastic, rubber, and glass. Manufacturers choose suppliers based on their ability to deliver quality materials on time and at a good price.
2. Manufacturing of Parts and Components: Tier 3 suppliers first process raw materials into basic parts. These parts are then sent to Tier 2 suppliers, who create sub-assemblies. Finally, Tier 1 suppliers assemble these into complex systems like engines, which are provided directly to the OEMs.
3. Assembly and Production: At OEM plants, these parts are put together in a step-by-step process to form the final vehicle. Many manufacturers use Just-In-Time (JIT) techniques to keep inventory low and ensure parts arrive exactly when needed, which requires careful coordination.
4. Quality Control: Throughout the assembly process, every part undergoes thorough inspections and tests. This rigorous quality control ensures that each vehicle meets safety and performance standards before it reaches the market.
5. Distribution and Logistics
Once completed, vehicles are shipped to dealerships using well-planned logistics. This involves selecting the most efficient routes and methods, tracking shipments, and ensuring compliance with import regulations to prevent delays and damage.
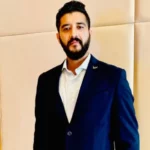
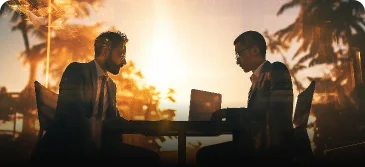
- In just 2 mins you will get a response
- Your idea is 100% protected by our Non Disclosure Agreement.
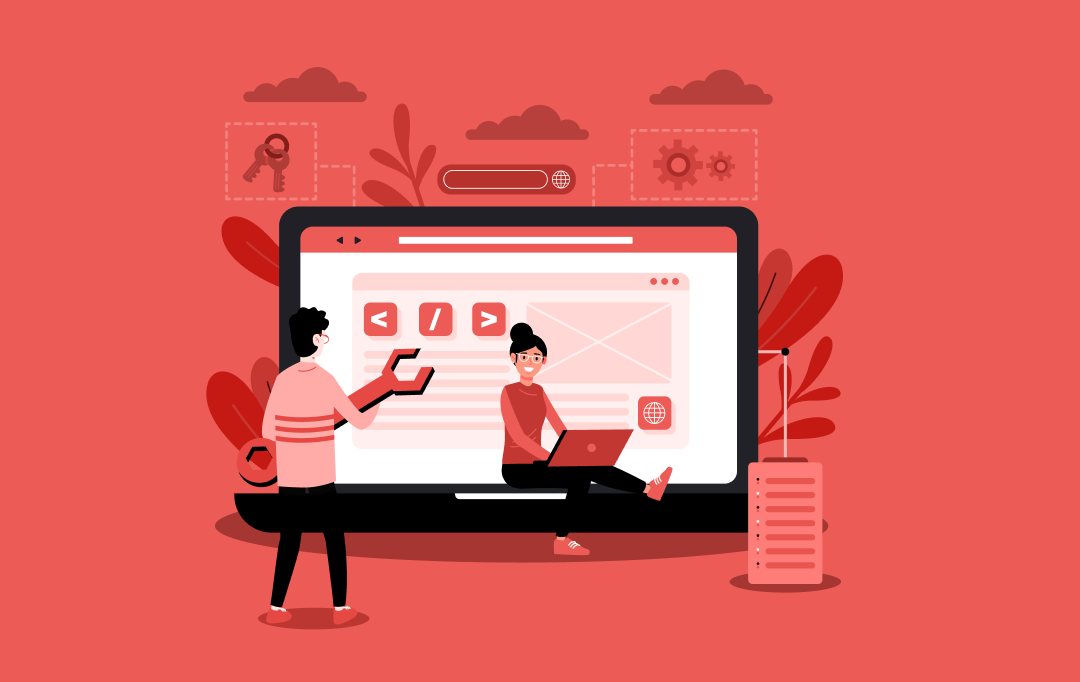
Custom Development or White Label Solutions: Which is Right for Your Business?
Key takeaways: 77% of companies are prioritizing digital transformation; the right tech approach is crucial for staying competitive. Custom development offers tailored solutions for unique needs, flexibility, and long-term scalability. Whereas, white-label solutions provide quick market entry, cost-efficiency, and easy customization for standard needs. Appinventiv’s expertise helps you navigate custom development vs white-label to choose…
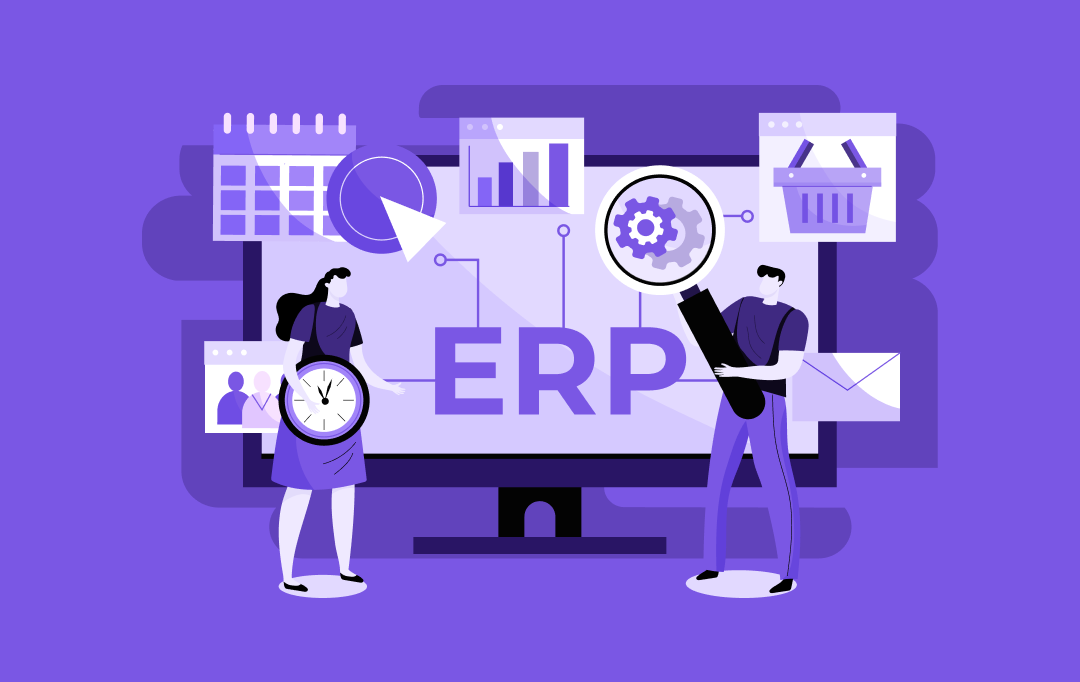
ERP Integration in Australia - Why It Is Essential and How to Do It Right
Key takeaways: ERP integration enables operational efficiency, reduced costs, and enhanced decision-making. Healthcare, finance, manufacturing, retail, and all the other sectors are benefiting from ERP integrations in Australia. While ERP integration can be costly, ranging from AUD 45,000 - AUD 450,000, it leads to significant long-term savings and scalability. Compliance with Australian regulations is critical,…
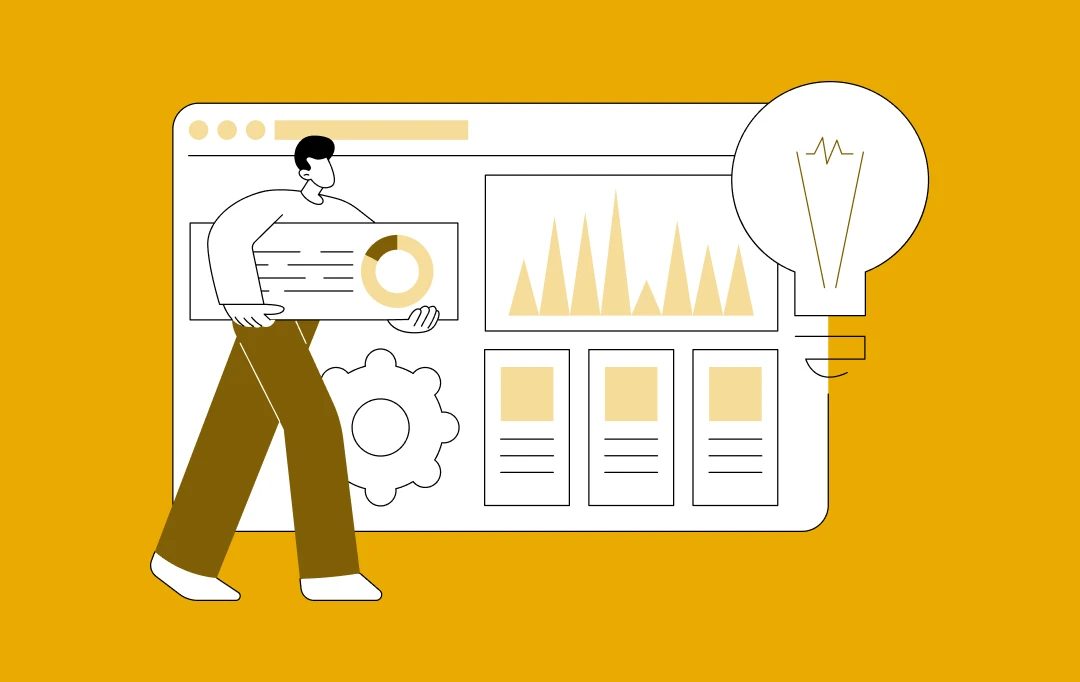
Predictive Analytics Software Development - Features, Benefits, Use Cases, Process, and Cost
Key Takeaways Predictive analytics helps businesses shift from “what has happened” to "what will happen," enabling proactive strategies rather than reactive ones. Real-time analytics and AI integration are driving the growth of predictive analytics, making it more accurate, accessible, and critical for business success. Custom predictive analytics solutions can enhance customer satisfaction, reduce costs, and…