- Game-Changing Applications of Predictive Analytics in the Oil and Gas Industry
- Assets Monitoring
- Predictive and Preventive Maintenance
- Supply Chain Management
- Safety and Risk Management
- Emission Predictions
- IT/OT Process Optimization
- Production Optimization
- Emission Predictions
- Prediction of Distillation Products
- Drilling Corrosion Detection and Prevention
- Benefits of Predictive Analytics in the Oil and Gas Business
- Increase Assets Availability and Reliability
- Improve Decision Making
- Enhance Operational Efficiency
- Gain Competitive Edge in the Market
- Adhere to Regulatory Compliance and Reporting
- Optimize Resource Allocation
- Real-World Examples of Companies Using Predictive Analytics in Oil and Gas
- Shell
- British Petroleum
- Chevron
- How to Implement Predictive Analytics in Your Oil and Gas Business
- Define Your Goals
- Assess Current Assets and Systems
- Collect Relevant Data
- Choose the Right Tools
- Develop Predictive Analytics Models
- Integrate Predictive Analytics Software
- Continuously Review and Refine Models
- Challenges of Predictive Analytics in the Oil and Gas Industry
- Data Quality Issues
- Integration with Existing Systems
- Resistance to Change
- Implement Predictive Analytics in Oil and Gas with Appinventiv’s Expertise
- FAQs
The oil and gas industry has always been at the forefront of technological advancements, constantly seeking innovative solutions to improve efficiency and maximize output. It is where predictive analytics emerges as a game-changing solution, transforming how companies manage operations, optimize production, and mitigate risks.
In the oil and gas sector, where even the smallest oversight can result in significant financial losses or operational risks, the ability to forecast future outcomes has never been more critical. Predictive analytics in oil and gas allows companies to leverage sheer volumes of data to foresee equipment failures before they occur, schedule repairs, optimize resource allocation, and anticipate market fluctuations, turning uncertainties into opportunities.
For instance, an unexpected leak in the pipeline can lead to costly damage and production halts. However, with predictive analytics in place, companies can monitor pipelines in real time, detecting early signs of corrosion or pressure anomalies. This allows them to address potential issues before they turn into big failures, reducing the risk of sudden breakdowns, minimizing repair costs, and preventing extended downtime.
In short and simple terms, the oil and gas industry is entering a new era of predictive and responsive operations. From optimizing drilling operations to preventing costly equipment failures, predictive analytics is proving to be the key to unlocking new levels of efficiency, safety, and profitability.
Let’s explore the 10 powerful oil and gas predictive maintenance use cases and benefits, along with some real world examples, challenges, and implementation strategies.
Game-Changing Applications of Predictive Analytics in the Oil and Gas Industry
The oil and gas industry has been adopting cutting-edge technologies like artificial intelligence (AI), machine learning (ML), Internet of Things (IoT), and predictive analytics to drive innovations. By leveraging the power of predictive analytics in oil and gas, companies can turn raw data into actionable insights. Let’s take a look at the top 10 applications of predictive analytics in the oil and gas industry:
Assets Monitoring
Predictive analytics provides real-time insights into the performance and condition of critical assets, such as pipelines, rigs, and refineries. This proactive monitoring allows companies to address potential issues early before they turn into costly failures, ensuring smooth operations and improving asset reliability. By identifying problems early, companies can maintain efficiency and change disruptions in production.
Predictive and Preventive Maintenance
In the oil and gas industry, diverse assets such as offshore pumping stations, drilling rigs, and pipelines are essential across upstream, midstream, and downstream operations. Predictive analytics in upstream operations enables companies to monitor these complex assets by using historical and real-time data and forecasts when equipment is likely to fail.
Similarly, predictive analytics in downstream processes helps track refinery equipment and pipeline integrity, allowing for timely maintenance interventions. This empowers companies to shift from reactive to preventive maintenance, minimizing unexpected downtimes, improving safety, and lowering repair costs.
Supply Chain Management
Predictive analytics transforms supply chain management by analyzing demand patterns, market trends, and supplier data to anticipate disruptions and optimize operations. By leveraging data from various sources, companies can accurately forecast demand, reduce inventory costs, and streamline logistics. It ensures efficient resource allocation, minimizes stockpiling, and prevents delays, leading to smoother operations and improved customer satisfaction.
Safety and Risk Management
By analyzing historical incident data, weather patterns, and equipment performance, predictive analytics identifies potential hazards before they occur. This proactive approach enables companies to comply with safety regulations, minimize infrastructure risks, and implement robust safety measures that predict and prevent possible accidents, creating a safer work environment.
Related Article: Leverage the Power of AI for Enhanced Risk Management in Business
Emission Predictions
With growing environmental regulations, predictive analytics helps oil and gas companies forecast their emissions levels based on current operations and future production plans. This enables them to take timely action in reducing emissions, ensuring compliance with environmental standards, and contributing to global sustainability goals.
You may like reading: How Do Green AI Applications Support Sustainability?
IT/OT Process Optimization
Predictive models are instrumental in revamping IT (Information Technology) and OT (Operational Technology) systems. By integrating data from both, companies can anticipate system failures, optimize technology workflows, and bridge the gap between traditional and modern processes, leading to smarter, more responsive operations.
Production Optimization
One of the most notable use cases of predictive analytics in oil and gas is optimizing fuel production. By analyzing real-time drilling data, reservoir conditions, and historical production patterns, predictive analytics fine-tunes extraction processes, maximizing output while reducing operational risks. This data-driven approach enhances resource utilization, improves equipment performance, and ensures more reliable production outcomes.
Emission Predictions
Oil companies are increasingly turning to predictive analytics to implement Predictive Emission Monitoring Systems (PEMS) as a cost-effective alternative to traditional Continuous Emission Monitoring Systems (CEMS). By analyzing real-time operational data, PEMS can accurately forecast greenhouse gas emissions, allowing companies to take proactive measures to reduce emissions and support global sustainability efforts by promoting cleaner operations and minimizing environmental impact.
Prediction of Distillation Products
Predictive analytics, combined with soft sensors, enhances refinery operations by forecasting the yield and purity of distillation products like gasoline and diesel. Soft sensors utilize algorithms such as Principal Component Regression (PCR) and Partial Least Squares (PLS) to assess distillation components at varying temperatures, comparing these with hard sensor data. This empowers operators to analyze raw material quality and optimize production processes, ensuring higher efficiency, reduced waste, and improved product quality.
Drilling Corrosion Detection and Prevention
Corrosion in drilling equipment is a major operational risk that can cause serious damage to machinery and lead to expensive repairs. Hence, the oil and gas industry must use robust corrosion detection and prevention techniques. Predictive analytics detects early signs of corrosion by monitoring various parameters such as temperature, pressure, and chemical composition in real time. This data helps operators prevent damage, optimize drilling practices, and improve equipment longevity, ensuring smooth operations and reducing maintenance costs.
Also Read: Role of Predictive Analytics in Closing Business Gaps
Benefits of Predictive Analytics in the Oil and Gas Business
Predictive analytics in oil and gas delivers powerful insights that help enhance decision-making and operational efficiency. Here are some of the most common benefits of predictive analytics in the oil and gas sector:
Increase Assets Availability and Reliability
Predictive maintenance in the oil and gas industry helps identify potential equipment failures before they escalate, allowing for timely maintenance and adjustments. This proactive approach significantly minimizes unexpected downtime and maximizes operational lifespans while improving the reliability and availability of assets.
Improve Decision Making
One of the most notable benefits of predictive analytics in oil and gas is its ability to drive strategic decision-making. By providing actionable insights, it enables companies to make well-informed choices regarding exploration, investment, and operational adjustments.
Enhance Operational Efficiency
Predictive analytics in the oil and gas industry refines operations by analyzing data to optimize processes and resource use. This leads to more efficient workflows and reduced waste, helping companies achieve their production goals more effectively.
Gain Competitive Edge in the Market
Staying ahead of market trends and competitor moves becomes easier with predictive analytics. Advanced analytics in oil and gas empowers companies to anticipate market changes, adapt strategies quickly, and gain competitive advantages in the industry.
Adhere to Regulatory Compliance and Reporting
Predictive analytics helps companies adhere to regulatory compliances by forecasting potential adherence issues and facilitating accurate reporting. This helps avoid hefty penalties and ensures that the companies meet all necessary legal requirements.
Optimize Resource Allocation
By forecasting future needs and performance, predictive models help better allocate the available resources. It ensures that the companies’ investments and efforts are spent in the right direction where they will be most effective.
Real-World Examples of Companies Using Predictive Analytics in Oil and Gas
There are many business giants that are already leveraging the use cases of predictive analytics in oil and gas to transform their operations and boost efficiency.
Shell
Shell utilizes predictive analytics to enhance equipment reliability and optimize maintenance schedules. It helps reduce downtime and improve operational efficiency across its oil rigs and refineries.
British Petroleum
British Petroleum is a global oil and gas company that leverages predictive analytics in oil and gas exploration to monitor drilling operations in real-time. This approach helps BP enhance safety and improve the efficiency of its exploration activities.
British Petroleum is a global oil and gas company that uses predictive analytics to monitor drilling operations in real-time, ensuring enhanced safety and improving the efficiency of its exploration activities.
Chevron
Chevron uses predictive analytics to optimize its upstream and downstream operations, from drilling to refining. It helps monitor and maintain machinery performance at a local and centralized level.
You may like reading: Cost to Build An Oil and Gas Data Management Software
How to Implement Predictive Analytics in Your Oil and Gas Business
Implementing a predictive maintenance strategy in your oil and gas business involves a structured approach combining several key steps.
Define Your Goals
The first step of implementing advanced analytics in oil and gas starts with identifying your goal — what do you want to achieve with predictive analytics? Whether it is reducing unplanned downtime, lowering maintenance costs, improving operational efficiency, or extending equipment lifespan, having well-defined goals will pave the way for the steps ahead.
Assess Current Assets and Systems
Evaluate the condition of your existing assets and identify areas for improvement in your maintenance practices. Identify which equipment is most critical to your operations, which deals with recurring breakdowns that require repair or replacement, and where predictive maintenance can have the greatest impact.
Collect Relevant Data
Gather historical and real-time data related to equipment performance, maintenance history, and operational conditions. Ensure that this data is comprehensive and relevant, as it forms the foundation for accurate predictive analysis model development.
Choose the Right Tools
Now, the next step is to choose the right predictive analytics tools that best fit your needs. Look for a tech stack that can handle large data volumes, offer advanced analytics capabilities, and integrate seamlessly with your existing systems.
Develop Predictive Analytics Models
It is indeed one of the most integral steps of the entire implementation strategy. At this stage, you need to use Artificial Intelligence, ML, and other advanced technologies to create advanced analytics models that can provide actionable insights for preventive maintenance.
Integrate Predictive Analytics Software
Now, it is time to integrate your developed predictive analytics model with your existing operational systems, such as enterprise asset management (EAM) systems, computerized maintenance management systems (CMMS), etc. This integration allows seamless data exchange, real-time analysis, and workflow management.
Continuously Review and Refine Models
Once developed and deployed with the existing systems, you need to regularly review and refine your predictive models to ensure their uninterrupted and high performance. Continuous update and improvement ensures that your models remain accurate and effective over time, adapting to new patterns and trends.
Challenges of Predictive Analytics in the Oil and Gas Industry
Adopting predictive analytics in oil and gas exploration presents several key challenges that can impact its effectiveness. Addressing these challenges with effective solutions is crucial to leverage the maximum benefits and use cases of oil and gas predictive analytics.
Data Quality Issues
Challenge: One of the most common challenges of predictive analytics in the oil and gas industry is poor data quality. Inconsistent or inaccurate data from various sources can lead to unreliable forecasts and inaccurate decisions.
Solution: Regularly audit and clean data to ensure accuracy and consistency in data formats. Implement automated data validation tools to enhance data integrity and reliability.
Integration with Existing Systems
Challenge: Integrating new predictive analytics tools with legacy systems can be difficult and may disrupt current operations. Incompatibilities and interoperability challenges between new and old systems can hinder smooth data exchange.
Solution: To address this issue, you can use middleware and APIs. It will facilitate smooth data exchange and ensure interoperability between different platforms.
Resistance to Change
Challenge: Employees may resist adopting new predictive analytics technologies due to unfamiliarity or fear of new processes. This resistance can slow down implementation and limit the applications of predictive analytics in the oil and gas industry.
Solution: You can address the resistance challenge by clearly communicating the benefits of predictive analytics in oil and gas. Also, you should provide thorough training to facilitate the smooth adoption of technology.
Implement Predictive Analytics in Oil and Gas with Appinventiv’s Expertise
Predictive analytics in the oil and gas industry is not just a buzzword; it is a transformative approach, redefining the way the industry operates and handles maintenance. Driven by the power of advanced technologies like AI, ML, computer vision, digital twin, and IoT, this predictive strategy empowers businesses to leverage their diverse datasets, ensuring that you are always a step ahead of your competitors.
However, developing and deploying these advanced analytics solutions can be complex, presenting challenges in deriving actionable insights from large volumes of data. Appinventiv offers a solution to this challenge.
As a leading oil and gas software development company, we specialize in developing and implementing predictive analytics that turn complex data into actionable insights. Our advanced data analytics consulting services help oil and gas companies efficiently address the challenges of this complex industry.
In our almost a decade of industry experience, we have delivered 3000+ successful projects for many reputed brands like Adidas, IKEA, and KFC, helping them address their operational challenges, expand their digital wings, and set new standards in their respective industries.
With a skilled team of 1600+ tech evangelists and proven expertise in AI, ML, IoT, Cloud, and data analytics, we deliver cutting-edge analytics solutions tailored to address your unique needs, optimize operations, reduce risks, and support growth across the oil and gas sector.
Partner with us and see how we can transform your raw data into strategic assets, driving success in your oil and gas operations.
FAQs
Q. How does predictive maintenance work in the oil and gas industry?
A. Oil and gas predictive analytics uses advanced sensors and data analytics techniques to monitor the real-time condition of equipment. By analyzing data such as temperature, pressure, and vibration, predictive models forecast potential equipment failures before they occur, allowing companies to perform maintenance at the optimal time. This approach reduces unplanned downtime, extends the lifespan of critical assets, and improves overall operational efficiency.
Q. What is predictive analytics in the oil gas industry?
A. Predictive analytics in oil and gas applies advanced data analysis techniques, such as machine learning and statistical algorithms, to forecast future events based on historical and real-time data. These analytics are applied across the three primary operational areas: upstream (exploration and production of crude oil), midstream (storage and transportation), and downstream (conversion of crude oil into final products).
By analyzing data from equipment and processes in each of these areas, predictive analytics helps companies anticipate equipment failures, optimize production, enhance safety, and make more informed decisions, ultimately improving efficiency and reducing costs throughout the entire value chain.
Q. How is predictive analytics changing the oil and gas industry?
A. Predictive analytics is revolutionizing the oil and gas industry through its diverse applications that enhance operational efficiency and decision-making across various domains. Some of the most remarkable applications of predictive analytics in the oil and gas industry are:
- Supply Chain Management
- Safety and Risk Management
- Emission Predictions
- Prediction of Distillation Products
- IT/OT Process Optimization
- Assets Monitoring
- Predictive and preventive maintenance
- Production Optimization
- Performance efficiency
- Drilling Corrosion Detection and Prevention
To gain an in-depth understanding of these applications and how they impact the industry, please refer to the above blog.
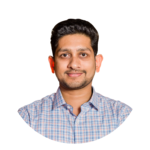
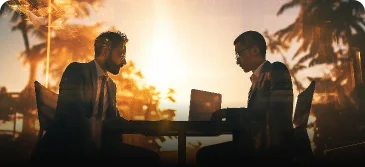
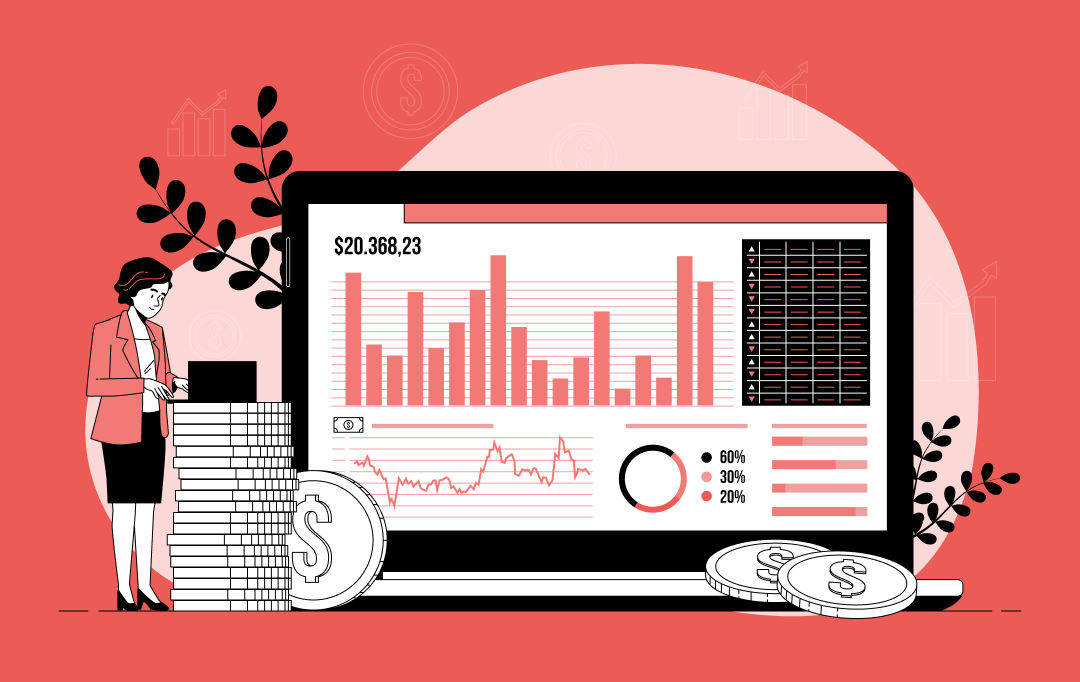
Unleashing the Role of Data Analytics in Driving Smarter Banking Decisions
The use of data analytics in banking is transforming how this data is interpreted and applied. Banks are using this data to make decisions that matter—fraud checks, loan approvals, or marketing campaigns. The focus has shifted: from storing data to using it smartly, and from pushing products to understanding people—being customer-centric. This shift is also…
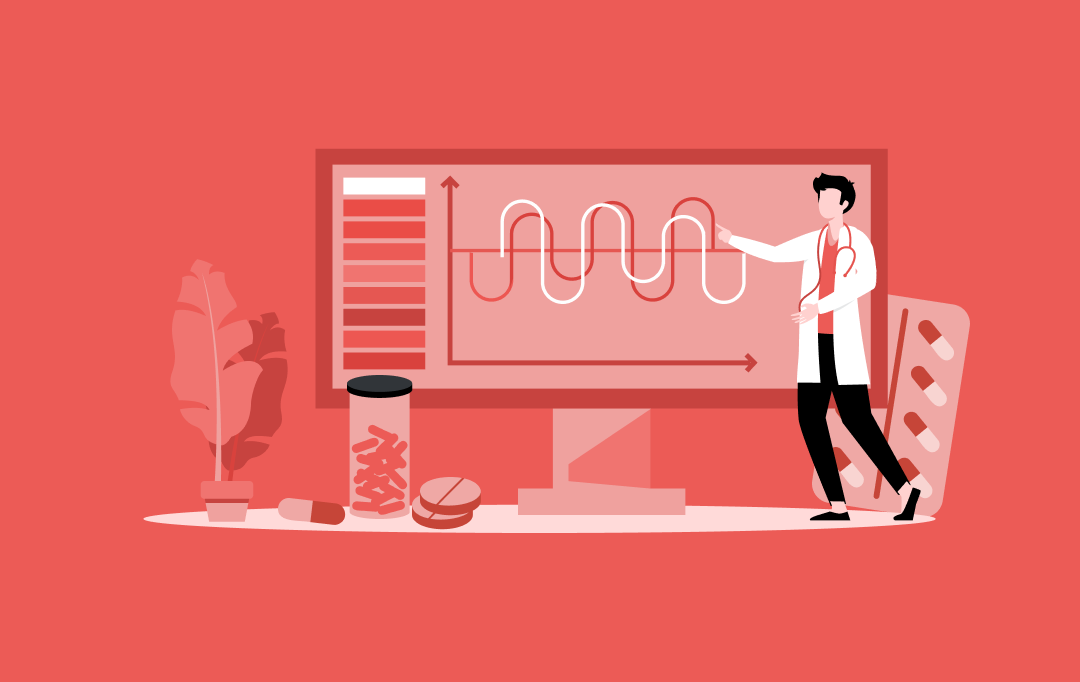
10 Use Cases and Examples of How Pharmacy Data Analytics is Transforming Operations and CX
Data has become the currency of modern business, and the pharmacy sector is no exception. From inventory optimization to regulatory compliance, pharmacies today face many challenges that demand precision and agility. Well, pharma data analytics is solving all these conundrums as the main lead, a transformative approach that now empowers businesses to get actionable insights…
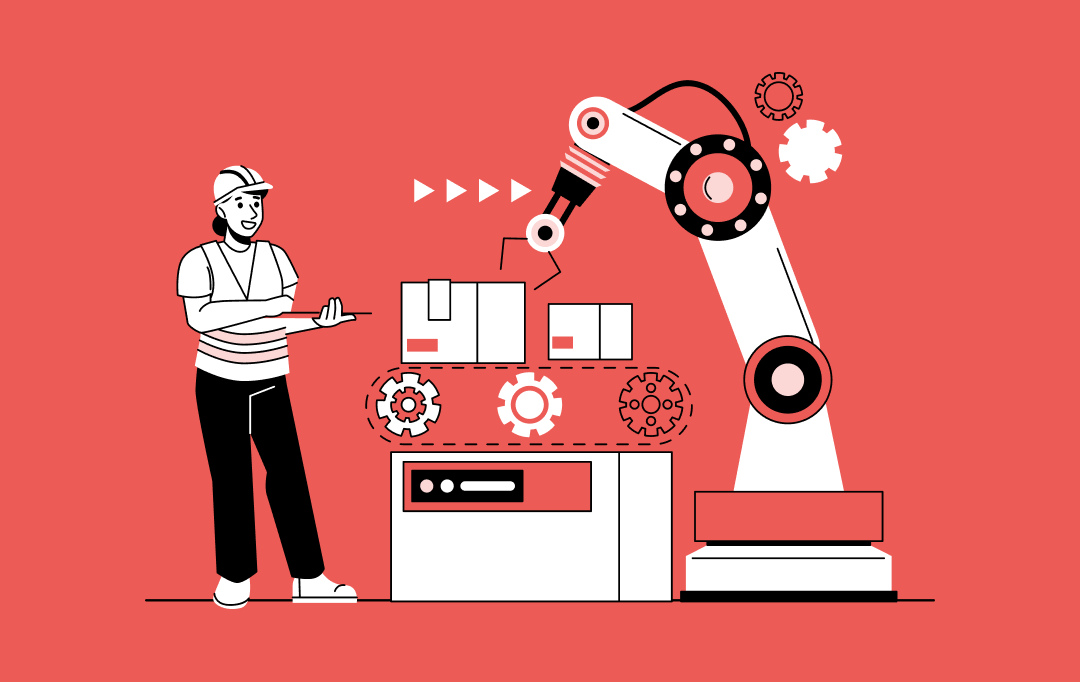
10 Use Cases and Benefits of Predictive Analytics in Manufacturing
Are you trying to stay in today’s manufacturing game with that old-school data analytics approach? Not gonna happen, buddy! Think about that old-school grind: manufacturing plant techies had to hustle around, scribbling notes and logging maintenance records by hand. All that manual intervention and hassle led to nothing more than messy data and bad calls.…