- Understanding Manufacturing Analytics Software Functionality and Market Dynamics
- Factors Affecting Manufacturing Analytics Software Development Cost
- Scope and Complexity
- Implementation Costs
- Technology Stack
- User Interface and Experience
- Security and Compliance
- Size and Location of the Development Team
- Scalability and Performance
- Innovative Manufacturing Analytics Solution Features
- Manufacturing Analytics Software Development Process
- Requirements Collection and Evaluation
- Design Software Architecture
- Develop the Software
- Ensure Thorough Testing
- Deploy the Software
- Ensure Continuous Maintenance and Support
- Tackling Implementation Challenges for Manufacturing Analytics Software
- Complexity and Customization
- Data Integration and Quality
- Change Management
- Data Security and Privacy
- Integration with Existing Systems
- How Appinventiv Can Help You Build Robust Manufacturing Analytics Software
- FAQs
Staying competitive in the manufacturing landscape today demands more than just advanced machinery; it requires leveraging the full potential of data. Manufacturing analytics software is a game-changer in this regard, designed to transform production processes by integrating real-time data from multiple sources. This comprehensive approach allows manufacturers to enhance efficiency, minimize downtime, and boost product quality.
The significance of manufacturing analytics software is profound: it delivers actionable insights that transform decision-making from speculative to strategic. It drives precision and boosts productivity by accurately forecasting maintenance needs, optimizing supply chains, and refining resource management.
In an industry marked by complexity and rapid change, the software is essential for overcoming challenges and fostering innovation, thereby sustaining a competitive edge.
This is why many leading enterprises are now investing in robust manufacturing analytics software to gain actionable insights and streamline operations. However, a common concern is analyzing the cost of developing such software.
The manufacturing analytics software development cost can range from $40,000 to $500,000, influenced by various factors, which we will explore later in this blog. We will first delve into how manufacturing analytics software functions, what are its market dynamics, and then discuss the factors affecting costs. We will also cover its features, development process, and implementation challenges with their solutions. Let’s explore these aspects in detail.
Understanding Manufacturing Analytics Software Functionality and Market Dynamics
Manufacturing analytics software operates by collecting data from diverse sources, including sensors, machinery, and production systems. It gathers and integrates this data in real-time or near-real-time, then applies advanced algorithms and statistical techniques for processing and analysis. The software generates actionable insights via dashboards and reports, emphasizing trends, performance metrics, and potential issues.
Utilizing prescriptive and predictive analytics, it enables manufacturers to anticipate challenges, optimize operations, and make informed decisions. This holistic perspective facilitates real-time monitoring, quality control, and process enhancements, ultimately driving increased productivity and cost efficiency.
According to a report by Market Research Future, the global manufacturing analytics market is expected to reach $19.1 billion by 2032, growing at a CAGR of 15.7% during the forecast period 2024- 2032.
The global manufacturing analytics software market is experiencing robust growth, driven by the rise of Industry 4.0 technologies and a heightened focus on data-driven decision-making. As manufacturers seek to optimize operations and maintain a competitive edge, the demand for advanced analytics solutions continues to surge.
The expansion is also supported by the widespread use of IoT devices, advancements in artificial intelligence, and a focus on predictive maintenance. Furthermore, the need for real-time insights and improved supply chain management is driving further adoption of analytics software in the manufacturing industry.
Factors Affecting Manufacturing Analytics Software Development Cost
Understanding the manufacturing analytics software cost breakdown involves considering a range of elements that influence pricing. By evaluating these aspects, businesses can make informed decisions that align with their budget and needs, ensuring a successful investment in analytics solutions.
Let’s have a look at some of the common factors influencing the overall cost to build manufacturing analytics software.
Scope and Complexity
The two main factors influencing manufacturing analytics software development cost are its scope and complexity. More time and technological know-how are required to build a more advanced system with sophisticated capabilities including real-time data processing, specialized reporting, and predictive analytics features.
Due to the integration complexity with multiple data sources and existing systems, the development process becomes more intricate and resource-intensive. Consequently, the total cost to build manufacturing analytics software increases with the scope and complexity of the features.
Implementation Costs
The overall manufacturing analytics software pricing depends on its implementation process. This encompasses deployment, setup, and user training. Deployment involves installing the software in a production environment, customizing it to meet specific business needs, and ensuring smooth integration with existing systems.
User training is another significant factor that impacts the total cost, as educating staff on effectively using the new technology requires time and resources. While this stage demands careful planning and investment, it is vital for ensuring a smooth transition and successful adoption of the manufacturing analytics software.
Technology Stack
The cost analysis of manufacturing analytics software is determined by the selection of programming languages, databases, frameworks, and analytics tools. Development costs may rise for advanced technologies due to increased licensing fees or the need for more specialized skills. While choosing high-performance and scalable technologies may result in higher upfront expenses, it may also promote efficiency and growth over the long run.
The custom manufacturing analytics software costs can also be impacted by how well these technologies integrate with current systems, as a smooth integration may require more testing and development. If you invest in a strong technology stack, the software will be reliable and future-proof, but you must carefully weigh the short and long-term expenses.
User Interface and Experience
Building a sophisticated and user-friendly interface involves significant design and development efforts. Significant resources are needed for custom dashboards, interactive visuals, and user-friendly navigation. Although it increases user satisfaction and engagement, an excellent UI/UX design raises the initial manufacturing analytics software development cost.
Additionally, investing in user experience testing and research can yield insights that improve design decisions and streamline workflows, possibly lowering the need for later, expensive redesigns and user training. In addition to increasing user engagement, a well-designed UI/UX facilitates easier software adoption and lowers the need for ongoing maintenance.
Security and Compliance
Putting strong security measures in place and ensuring adherence to industry regulations can influence the overall manufacturing analytics software cost estimation. This covers audit trails, user authentication, and data encryption. Costs associated with development and maintenance may increase if extra functionality and frequent audits are needed to comply with industry standards.
Moreover, continuous investment is required to integrate sophisticated security mechanisms and frequent updates to handle new threats. Ensuring long-term trust and stability for the software is achieved by investing in complete security and compliance, which not only safeguards sensitive data but also reduces the likelihood of expensive data breaches and legal penalties.
Size and Location of the Development Team
The skills and size of the development team are pivotal in shaping costs. Specialists, such as data scientists and software architects, typically charge higher fees. The location of the team also plays a vital role in cost variations, as development rates differ across regions. Opting for development teams based in India can be particularly advantageous, given the country’s extensive pool of talented IT professionals.
India’s IT sector is well-regarded for its proficiency in software development, data science, and analytics, offering access to highly skilled experts adept in advanced technologies. Utilizing this talent pool can help manage manufacturing analytics software development costs while ensuring high-quality outcomes. Nonetheless, effective project management and coordination remain crucial to achieving a seamless integration and successful project delivery.
Also Read: How to Hire a Dedicated Development Team?
Scalability and Performance
Software designers need robust architectures and potentially scalable cloud infrastructure to create applications that can manage massive data volumes and scale effectively. Optimizing infrastructure and algorithms is necessary to provide excellent performance, which raises the initial costs of implementing manufacturing analytics.
On the other hand, scalability investments fund future expansion and user demands. Furthermore, scalable solutions enable seamless upgrades and connections by preventing expensive system overhauls as the system grows. By adopting a proactive scalability strategy, the software is guaranteed to be efficient and flexible in a changing business environment.
Innovative Manufacturing Analytics Solution Features
Manufacturing analytics solutions, to work seamlessly, must be integrated with high-performing features that enhance data accuracy, streamline operations, and deliver actionable insights. However, it’s important to note that both the complexity and number of features can impact the overall cost to build manufacturing analytics software.
Here are some of its top features: Here are some of its top features:
Quality Management: This feature encompasses tools for identifying and analyzing quality issues to ensure improved product standards and enhanced manufacturing processes.
Integration Capabilities: This feature facilitates smooth data exchange with ERP systems and provides real-time process control through SCADA systems, integrating seamlessly into existing operations.
Real-Time Data Collection: This feature involves the continuous gathering of data from production sensors and IoT devices, offering immediate insights into operational status and performance.
Collaboration Tools: This feature supports enhanced teamwork through reporting and sharing functionalities and provides alerts and notifications to keep teams informed about critical issues.
Data Visualization: Converts complex datasets into clear charts, graphs, and heatmaps for straightforward analysis. Customizable dashboards and reports enable quick comprehension of key insights and trends.
Quality and Performance Monitoring: Monitors and evaluates product quality and equipment performance to detect issues and enhance manufacturing processes. Offers in-depth analysis to ensure high standards and operational efficiency.
Advanced Analytics and Reporting: Employs predictive, descriptive, and prescriptive analytics to reveal trends, forecast outcomes, and provide actionable insights. Delivers detailed reports to support informed strategic decisions.
Performance Monitoring: This feature tracks key metrics like throughput and downtime, and includes benchmarking tools to compare performance against historical data or industry standards.
Advanced Data Analytics: This feature offers capabilities such as predicting future trends, recommending actionable process improvements, and analyzing data to uncover patterns and anomalies.
Data Storage & Processing: Handles and stores large amounts of data efficiently, enabling rapid access and processing. Supports effective data management practices to ensure data integrity and availability.
Asset Analytics: Assesses the performance and utilization of physical assets to optimize their value and extend their lifespan. It also identifies maintenance needs and operational inefficiencies for cost savings.
Production Analytics: Analyzes production data to track output, efficiency, and downtime. Helps optimize production schedules, minimize waste, and improve overall manufacturing performance.
Supply Chain Analytics: Evaluates supply chain data to enhance inventory management, improve supplier performance, and boost overall efficiency. Offers insights into logistics, procurement, and demand forecasting.
Manufacturing Analytics Software Development Process
The development of manufacturing analytics software involves creating tailored solutions that meet specific business needs and objectives. By leveraging advanced technologies and industry expertise, the process ensures that the final product delivers actionable insights and drives operational efficiency. Here are the key steps of manufacturing analytics software development:
Requirements Collection and Evaluation
To completely comprehend the demands and goals of the manufacturing organization, a thorough requirements collection and analysis is the first step in the development process. In order to identify the software’s key features, functionalities, and data sources, stakeholders must be involved at this stage.
The development team examines current workflows and systems to ensure the software meets business objectives and solves current problems. The outcome is a comprehensive requirements document that serves as a roadmap for the design and development stages.
Design Software Architecture
During the design process, a thorough blueprint for the manufacturing analytics software is created. This includes generating wireframes of user interfaces for manufacturing professionals, designing data models specifically for manufacturing processes, and creating system architectural diagrams.
The design of the software outlines how it will manage production data, perform analytics, and present insights. These wireframes guide the development team, ensuring that the software meets user needs and integrates seamlessly with production processes.
Develop the Software
The development phase involves converting design specifications into fully functional software, impacting the overall manufacturing analytics software development cost. This includes writing code, integrating data sources from the manufacturing industry, and implementing basic analytics functions like real-time monitoring and predictive maintenance.
Iterative testing and improvement are part of the development process, which addresses problems as they appear. The end product is software that offers fundamental analytics functions, laying the foundation for extensive testing and optimization.
Ensure Thorough Testing
Testing is an essential step to ensure the manufacturing analytics software operates reliably and satisfies all requirements. Unit, integration, system, and user acceptance tests (UAT) must be carried out to verify the software’s functionality and performance.
The aim is to find and fix errors, performance problems, and deviations from the original specifications. Thorough testing guarantees that the software is reliable and efficient, offering insightful information and assistance for production processes.
Deploy the Software
Deployment involves moving the manufacturing analytics software from a development environment to an operational manufacturing setting. This includes moving pertinent manufacturing data, installing and configuring the software in the production setting, and ensuring it integrates with the current machinery and systems.
User training and documentation are supplied to ensure a seamless transition and that users can utilize the software to its full potential. A successful deployment guarantees that the software is functional and prepared to assist with manufacturing processes.
Ensure Continuous Maintenance and Support
Maintaining the effectiveness and accuracy of the manufacturing analytics software requires post-deployment, continuous maintenance, and support. This entails executing routine updates, resolving issues, and offering users technical support.
Other aspects of maintenance include updating the software to reflect evolving production requirements and integrating user feedback. Maintaining the software’s functionality and data guarantees that it will continue to provide insightful analysis and assistance for changing production processes. It is also crucial to note that the manufacturing analytics software development cost is also influenced by maintenance expenses that include ongoing updates, bug fixes, and technical support.
Tackling Implementation Challenges for Manufacturing Analytics Software
Implementing manufacturing analytics software requires careful planning and strategic execution to ensure success. Organizations can streamline the deployment process by addressing key considerations, employing effective strategies, and fully leveraging the benefits of advanced analytics solutions.
Let’s check out some of the common implementation challenges of manufacturing analytics software and solutions to overcome those:
Complexity and Customization
Manufacturing analytics software often requires intricate configuration and customization to match specific manufacturing processes, which can result in longer implementation periods and increased costs.
Solution: Build a solution with adaptable customization features and partner with technical partners like Appinventiv, that offer personalized implementation support. Provide comprehensive training and ongoing assistance to help users effectively leverage and tailor the software to their needs.
Data Integration and Quality
Integrating data from diverse sources like sensors, ERP, and MES systems can be complex and time-consuming. Ensuring the data’s accuracy and consistency is vital for generating reliable insights.
Solution: Utilize advanced data integration tools and establish strong data governance practices to standardize and clean data across different systems. Implement ETL (Extract, Transform, Load) processes and conduct regular data quality assessments to ensure data integrity and uniformity.
Change Management
Resistance to change within an organization can hinder the successful adoption of new analytics solutions. If not managed effectively, this resistance might lead to implementation issues and lower software usage.
Solution: Create a detailed change management plan that incorporates effective communication, active involvement of stakeholders, and strategies to handle resistance. Emphasize the advantages of the new software and engage key stakeholders to secure their support and encourage a positive outlook on the transition.
Data Security and Privacy
Keeping your sensitive manufacturing data safe from breaches and complying with privacy laws is crucial. If data isn’t properly protected, it can lead to serious risks and legal trouble.
Solution: Secure your information with solid security practices, such as data encryption, strict access controls, and regular security audits. Ensure the software meets data protection standards and regulations.
Integration with Existing Systems
Making new software work with your current IT setup and old systems can be tricky and might need some major tweaks. A poor integration process can mess with your daily operations.
Solution: Build software that offers strong integration features and good API support to make the connection smooth. Team up with your IT department to plan, test, and roll out the integration, and consider doing it in phases to avoid any major disruptions.
How Appinventiv Can Help You Build Robust Manufacturing Analytics Software
Manufacturing analytics software is essential for converting raw data into actionable insights, allowing businesses to boost efficiency, cut costs, and foster innovation. As industries advance in digital transformation, the importance of analytics grows in refining production processes, forecasting maintenance requirements, and enhancing overall operational performance.
The future of manufacturing analytics is set for expansion, driven by advancements in artificial intelligence, machine learning, and real-time data processing, which promise more advanced and predictive analytics capabilities.
Appinventiv, as a leading software development services company, can be instrumental in developing robust manufacturing analytics software tailored to your specific needs. With our extensive expertise in the manufacturing sector and advanced technologies, we provide end-to-end services that ensure seamless integration, precise data accuracy, and actionable insights.
As an expert manufacturing software development company, we specialize in crafting customizable analytics platforms that align with your operational demands, using the latest technologies to enhance efficiency and drive innovation.
Our approach encompasses detailed planning, agile development, and continuous support to resolve any challenges during implementation. Partnering with us means you benefit from our vast experience and proven success in delivering impactful analytics solutions that improve decision-making and operational performance. This partnership not only helps you navigate the complexities of manufacturing analytics but also sets your business up for sustained growth and success.
To know more about the manufacturing analytics software development cost and discuss other project requirements, connect with our team today!
FAQs
Q. How much does it cost to develop a manufacturing analytics software?
A. The cost to develop manufacturing analytics software generally ranges between $40,000 and $500,000. This variance depends on the software’s complexity, feature set, customization requirements, and integration with existing systems. Advanced capabilities, such as real-time data processing and predictive analytics, can also impact the total cost.
Furthermore, the manufacturing analytics software development cost may increase with ongoing maintenance, support, and user training. Investing in a comprehensive development process can enhance long-term value and operational efficiency.
Q. How long does it take to develop a manufacturing analytics software?
A. The timeline for developing manufacturing analytics software typically ranges from 6 to 18 months. This period can vary based on the complexity of the software, the number of features, and the effectiveness of the development team.
Key factors influencing the timeline include data integration, user interface design, and iterative testing. Additionally, changes in project requirements or technical challenges may extend the development time. Efficient project management and clear communication are crucial for minimizing delays and ensuring timely completion.
Q. What are some of the latest manufacturing analytics trends?
A. Here are some of the latest trends in manufacturing analytics:
Digital Twins: Adopting digital twins to create virtual replicas of physical assets, allowing for real-time simulation, monitoring, and optimization of manufacturing systems.
Big Data Analytics: Leveraging big data to scrutinize large volumes of production data, uncover performance insights, and identify trends that drive informed decision-making.
Artificial Intelligence and Machine Learning: Using ML and AI in manufacturing to enhancepredictive analytics, automate decision-making processes, and improve detection of anomalies in manufacturing.
IoT Integration: Connecting Internet of Things (IoT) devices to gather and analyze data from machinery and sensors, providing a comprehensive view of manufacturing processes.
Edge Computing: Employing edge computing to analyze data near its source, minimizing delays and enabling real-time insights for more agile manufacturing operations.
Q. What are some of the top benefits of developing manufacturing analytics software?
A. Here are some of the top advantages of implementing manufacturing analytics software:
Predictive Maintenance: By monitoring equipment performance and detecting wear patterns, analytics tools can predict failures before they happen, allowing for timely maintenance and reducing unexpected downtime.
Enhanced Quality Assurance: Data analysis helps identify patterns and anomalies in production lines, leading to improved product quality and fewer defects.
Informed Decision Making: Detailed data analysis provides accurate, real-time information for decision-makers, facilitating more strategic and effective business decisions.
Boosted Operational Efficiency: Real-time insights from analytics software help pinpoint inefficiencies, streamline processes, and reduce downtime, enhancing overall productivity.
Improved Safety and Compliance: Analytics assist in monitoring compliance with safety standards and regulations, while also identifying potential hazards and suggesting preventive measures.
Accurate Demand Forecasting: Analytics tools enable better predicting of future demand based on historical data and trends, leading to more accurate production planning and inventory management.
Strategic Growth Insights: Insights into market trends, customer preferences, and competitive benchmarks help in crafting effective growth and innovation strategies.
Cost Savings: Analytics software uncovers opportunities for cost reduction, such as cutting waste, improving energy efficiency, and optimizing supply chain management, resulting in significant savings.
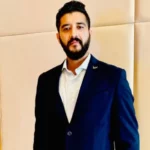
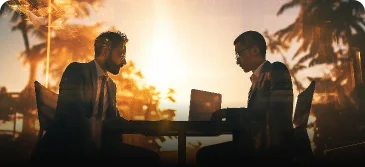
- In just 2 mins you will get a response
- Your idea is 100% protected by our Non Disclosure Agreement.
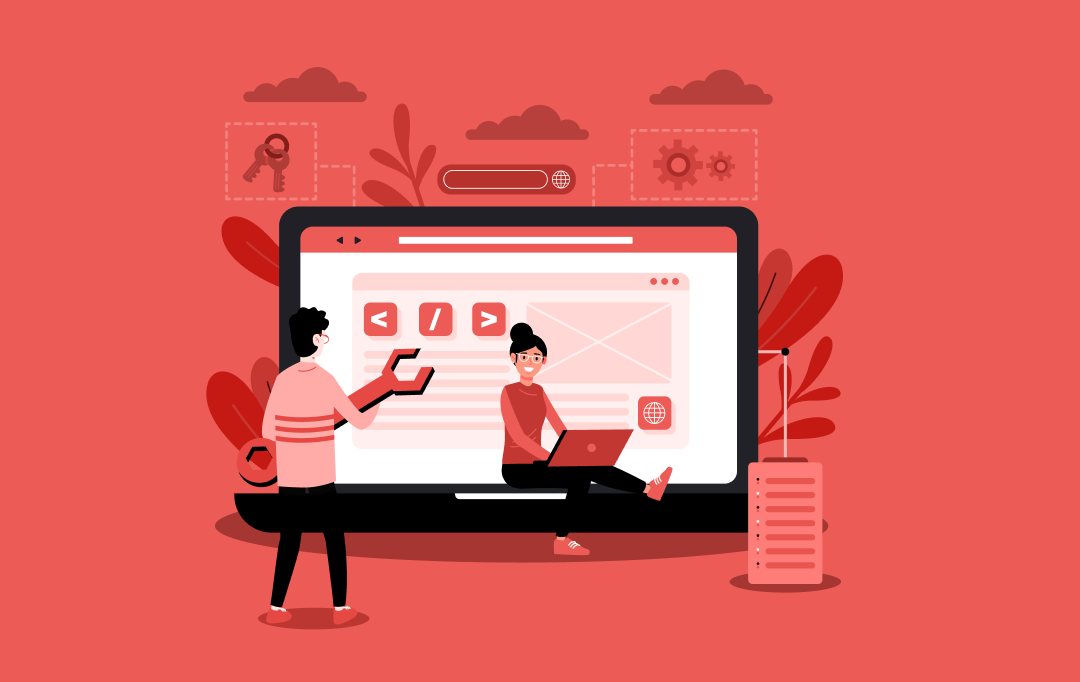
Custom Development or White Label Solutions: Which is Right for Your Business?
Key takeaways: 77% of companies are prioritizing digital transformation; the right tech approach is crucial for staying competitive. Custom development offers tailored solutions for unique needs, flexibility, and long-term scalability. Whereas, white-label solutions provide quick market entry, cost-efficiency, and easy customization for standard needs. Appinventiv’s expertise helps you navigate custom development vs white-label to choose…
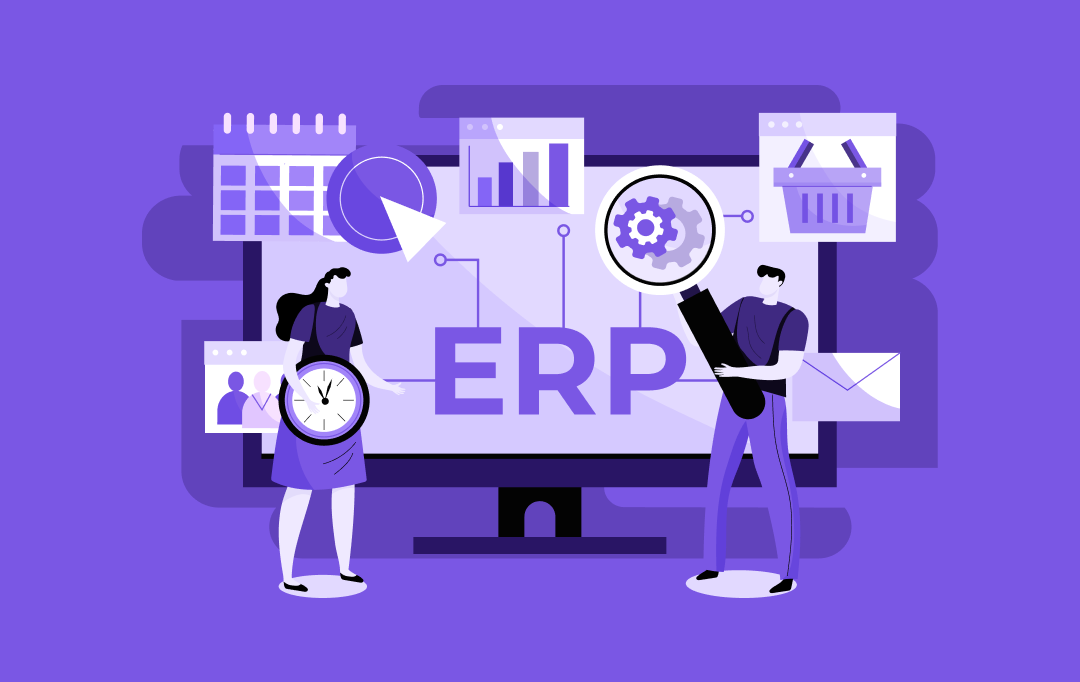
ERP Integration in Australia - Why It Is Essential and How to Do It Right
Key takeaways: ERP integration enables operational efficiency, reduced costs, and enhanced decision-making. Healthcare, finance, manufacturing, retail, and all the other sectors are benefiting from ERP integrations in Australia. While ERP integration can be costly, ranging from AUD 45,000 - AUD 450,000, it leads to significant long-term savings and scalability. Compliance with Australian regulations is critical,…
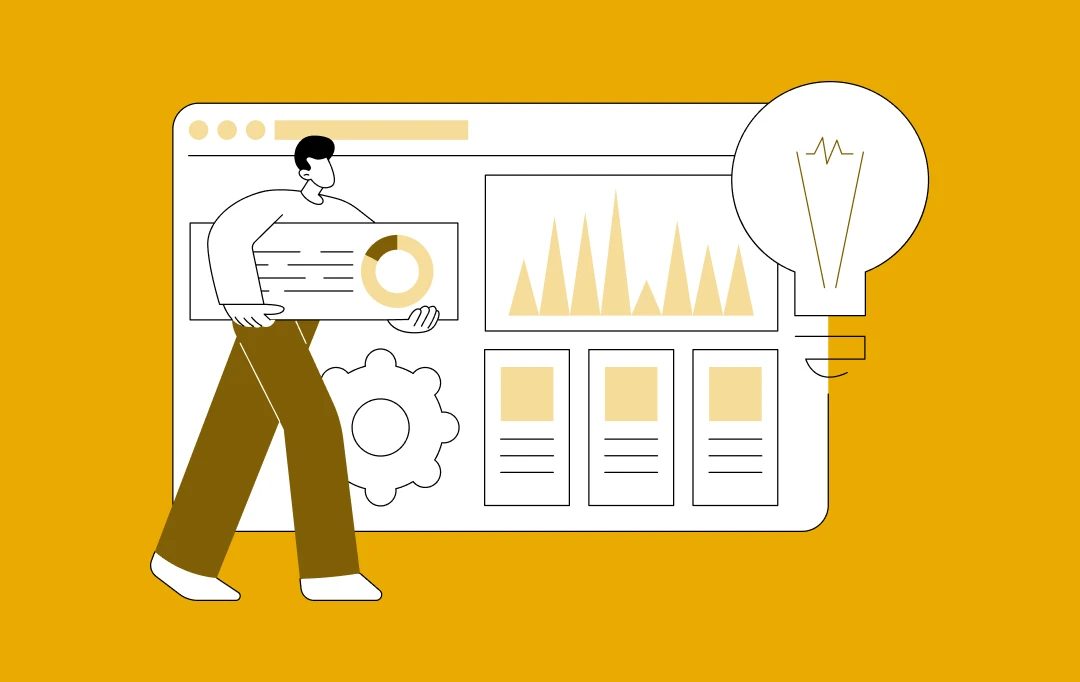
Predictive Analytics Software Development - Features, Benefits, Use Cases, Process, and Cost
Key Takeaways Predictive analytics helps businesses shift from “what has happened” to "what will happen," enabling proactive strategies rather than reactive ones. Real-time analytics and AI integration are driving the growth of predictive analytics, making it more accurate, accessible, and critical for business success. Custom predictive analytics solutions can enhance customer satisfaction, reduce costs, and…