- Benefits of Digital Twin in the Automotive Industry: Empowering Autonomous Vehicle Testing and Real-Time Performance Adjustments
- Enhanced Prototyping Efficiency
- Predictive Maintenance and Lifecycle Management
- Improved Vehicle Performance Optimization
- Supply Chain and Manufacturing Optimization
- Cost-Effective Customization
- Data-Driven Quality Control
- Sustainability and Energy Efficiency
- Top 10 Applications of Digital Twins in the Automotive Industry: Enhancing Design, Manufacturing, and Performance
- Real-Time Vehicle Monitoring
- Smart Factory Integration
- Lifecycle Management
- Design Optimization for Extreme Conditions
- Assembly Line Optimization
- Vehicle Customization Testing
- Crash Simulation and Safety Testing
- Supply Chain Resilience
- Post-Production Analysis
- Revolutionizing Automotive with Digital Twin Technology: How Businesses are Leading the Change
- How to Implement Digital Twin for Automotive Design and Manufacturing
- Define Objectives and Scope
- Collect and Integrate Data
- Develop a Digital Twin Model
- Implement Real-Time Analytics
- Test and Validate
- Deploy the Digital Twin
- Iterate and Improve
- Challenges in Adopting Digital Twin in the Automotive Industry
- Future of the Digital Twin in Automotive Industry
- Appinventiv's Expertise in Digital Twin Technology for Automotive Design and Manufacturing
- FAQs
The automotive industry is rife with complexities—whether it’s navigating intricate supply chains, maintaining rigorous quality control standards in manufacturing, or driving innovation in an ever-evolving market. These challenges aren’t just operational—they also pose significant risks to human safety, particularly in areas like real-world testing and optimization.
The growing need to enhance efficiency, reduce costs, and meet rising consumer expectations for personalization and sustainability has only magnified these issues.
Amid these pressures, companies are turning to an innovative solution: digital twins in the automotive industry. By creating virtual replicas of physical systems, this technology mitigates potential hazards by allowing businesses to test, optimize, and simulate various processes in a risk-free environment.
It not only streamlines operations but also enables proactive problem-solving and data-driven decision-making, transforming how businesses approach automotive challenges while unlocking new avenues for growth.
The global market for digital twins in the automotive industry was valued at $2.2 billion in 2022 and is expected to surge to $34.6 billion by 2032, with a compound annual growth rate (CAGR) of 32.6% from 2023 to 2032.
Benefits of Digital Twin in the Automotive Industry: Empowering Autonomous Vehicle Testing and Real-Time Performance Adjustments
Digital twin technology is revolutionizing the auto industry by creating virtual replicas of the vehicles and their environments. The digital twin platform in the automotive industry allow businesses to simulate real-world driving conditions and test scenarios without physical prototypes, speeding up development and improving safety.
By integrating digital twin platform in the automotive industry, businesses can monitor performance in real-time, predict failures, and optimize maintenance, ensuring reliable and efficient operations. This technology is key to advancing autonomous systems and maintaining a competitive edge in the automotive industry.
The benefits of digital twins in the automotive industry also include enhancing vehicle safety, reducing downtime, and improving overall design efficiency. Let’s comprehend in detail!
Enhanced Prototyping Efficiency
Digital twins streamline the prototyping process by creating virtual representations of vehicles, minimizing the reliance on physical models. This accelerates the design phase, enabling engineers to simulate and test various designs in real-time under different operating conditions, which helps in identifying potential flaws early on. The result is reduced development costs and shorter time-to-market for new vehicle models.
Predictive Maintenance and Lifecycle Management
Integrated with IoT sensors, digital twins enable real-time monitoring of vehicle components, predicting failures and maintenance needs before they occur. By analyzing data from connected vehicles, manufacturers can optimize maintenance schedules, reduce unplanned downtimes, and prolong the operational life of vehicles, offering significant cost savings and increased reliability throughout the vehicle’s lifecycle.
Improved Vehicle Performance Optimization
With digital twins, designers can conduct advanced simulations to optimize vehicle performance, such as fuel efficiency, aerodynamics, and crash testing. Virtual tests allow engineers to make design adjustments in a risk-free digital environment, leading to better-performing, safer vehicles. This technology ensures that only the most optimized versions of the design move into the physical testing phase.
Also read: Automotive Digital Transformation – Benefits, Use Cases and Challenges for Modern Businesses
Supply Chain and Manufacturing Optimization
In manufacturing, digital twins simulate the entire production process, offering real-time visibility into operations, logistics, and machine performance. Manufacturers can predict bottlenecks, optimize material flows, and adjust processes on the go. This results in more efficient production lines, reduced waste, and minimized production downtime.
Cost-Effective Customization
Digital twins in the automotive industry enable cost-effective customization by allowing manufacturers to simulate the effects of custom vehicle features and configurations. With this technology, automotive companies can offer personalized vehicles at a mass-production scale, as the twin helps assess manufacturing feasibility, costs, and production times for each unique configuration without incurring additional prototyping expenses.
Data-Driven Quality Control
During production, digital twin technology in the automotive industry tracks every component’s journey through the assembly line, monitoring quality in real-time. Any deviations from design specifications or manufacturing errors are immediately flagged for correction. This real-time monitoring reduces defects and enhances the overall quality of the vehicles, ensuring consistent performance and reliability.
Sustainability and Energy Efficiency
By simulating the environmental impact of materials, manufacturing processes, and vehicle operation, digital twins in the automotive industry support businesses in developing more sustainable vehicles. They enable the testing of energy-efficient designs and materials without the environmental costs of physical trials, helping manufacturers meet sustainability goals while reducing carbon footprints across the entire product lifecycle.
Also read: How AI, IoT, and AR/VR Technologies are Helping Companies Achieve their Sustainability Goals
These benefits underscore how digital twins transform automotive design and manufacturing, delivering efficiency, innovation, and sustainability throughout vehicle development.
Top 10 Applications of Digital Twins in the Automotive Industry: Enhancing Design, Manufacturing, and Performance
Let’s examine how digital twin technology in the automotive industry empowers businesses to optimize operations, boost productivity, and foster innovation in both manufacturing and automotive design. Here are the top applications of digital twins in the automotive industry:
Real-Time Vehicle Monitoring
Real-time vehicle monitoring is one of the most popular use cases of digital twins in automotive. Through automotive digital twins, IoT sensors embedded in vehicles provide real-time data on the performance and wear of individual components. This data helps manufacturers predict and prevent potential failures by adjusting designs or maintenance schedules accordingly, ensuring vehicles stay on the road longer with minimal unexpected downtime.
Smart Factory Integration
In the manufacturing process, digital twins in the automotive industry help simulate operations, offering insights into machine performance, production line flow, and logistics. This technology optimizes factory operations, predicting when machinery needs servicing and avoiding costly downtime, ultimately leading to increased productivity and reduced operational costs.
Lifecycle Management
Digital twin technology in the automotive industry extends beyond the factory floor, providing a detailed simulation of the vehicle’s entire lifecycle. Manufacturers and owners can track vehicle performance, usage, and potential repair needs, ensuring better maintenance planning and prolonging the vehicle’s lifespan while minimizing unexpected repairs.
Design Optimization for Extreme Conditions
Digital twins allow automotive engineers to test vehicle designs under extreme weather conditions, such as high heat, cold, or humidity, without having to build expensive prototypes. This makes it easier to identify weaknesses and refine designs for various climates, resulting in vehicles that can perform reliably in diverse environments. This is a prime example of the use cases of digital twins in automotive.
Assembly Line Optimization
By simulating the entire production line, digital twins in automotive engineering help manufacturers identify potential bottlenecks, reduce material waste, and optimize the placement of robots or human workers for maximum efficiency. This ensures faster production cycles, better resource management, and improved product quality with fewer delays.
Vehicle Customization Testing
A digital twin in the automotive industry enables manufacturers to simulate customer-specific customizations. They can assess the impact of personalized features, like different interior layouts or technology integrations, on production times and costs before implementing the changes physically, providing a seamless way to offer tailored vehicles at scale without compromising on efficiency.
Crash Simulation and Safety Testing
Engineers use digital twins in automotive manufacturing designs to run virtual crash tests, helping them improve safety features like airbags, seatbelts, and crumple zones. These simulations save time and resources, ensuring safety standards before physical tests are conducted, thereby enhancing vehicle safety and regulatory compliance.
Supply Chain Resilience
Implementation of digital twins in the automotive Industry offers a complete overview of the supply chain, from raw materials to finished products. Manufacturers can track parts in transit, simulate potential delays, and make adjustments to ensure timely production, improving supply chain transparency and reducing the risk of disruptions.
Post-Production Analysis
After vehicles are sold, the Implementation of digital twins in the automotive industry provides ongoing feedback from real-world data. This helps automakers understand how vehicles perform over time, which can inform future design improvements or guide recalls if common issues arise, offering valuable insights for continuous innovation and customer satisfaction.
These enhancements make the use cases more comprehensive, showcasing the full potential of digital twins in automotive manufacturing.
Revolutionizing Automotive with Digital Twin Technology: How Businesses are Leading the Change
Here are some prominent examples of digital twin technology in the automotive industry, enabling real-time monitoring, simulation, and optimization of vehicle design and manufacturing processes. Let’s explore how automotive companies are leveraging digital twin technology to streamline operations, enhance product quality, and achieve their business goals.
Ford
Ford utilizes its digital twin in the automotive industry to create virtual replicas of vehicles, allowing engineers to simulate and test different designs before manufacturing physical prototypes. This significantly reduces development time and costs while enabling precise optimizations. By incorporating real-time feedback from digital simulations, Ford enhances vehicle performance and accelerates time-to-market.
Tesla
Tesla leverages digital twins in automotive design for real-time monitoring of its electric vehicles, capturing data such as battery health, performance, and potential faults. This technology enables predictive maintenance by identifying issues before they occur, reducing downtime and enhancing vehicle reliability. Tesla also uses these insights to continuously improve the design and efficiency of future models.
BMW
BMW employs digital twin technology across its smart manufacturing plants, enabling real-time simulations of production processes. This allows the company to detect bottlenecks, streamline workflows, and optimize factory operations. By integrating IoT data from machines, BMW enhances production efficiency, reduces waste, and ensures higher-quality output, providing one of the best examples of digital twin technology in the automotive industry.
Daimler
Daimler uses automotive digital twins to manage the entire lifecycle of their vehicles, from initial design to post-sales services. By creating virtual models that track real-time vehicle data, Daimler ensures continuous monitoring and optimization of performance. This results in improved product quality, faster problem resolution, and a more personalized customer experience throughout the vehicle’s lifespan.
How to Implement Digital Twin for Automotive Design and Manufacturing
Implementing Digital Twin Technology in automotive design and manufacturing involves several strategic steps. Let’s comprehend each step holistically and strategically.
Define Objectives and Scope
Whether you’re in automotive, construction, or another technology-driven industry, begin by clearly defining what you aim to achieve with Digital Twin technology. Outline the specific areas where digital twins will be applied, such as improving vehicle performance, optimizing production processes, or enhancing project planning. Establishing clear objectives ensures that the technology addresses your specific needs and aligns with overall business goals.
Collect and Integrate Data
The process involves integrating data from multiple sources such as CAD designs, simulations, and physical measurements. This data fusion enables the digital twin to precisely mirror the physical entity’s geometry, behavior, and interactions.
Develop a Digital Twin Model
Once the data is integrated, utilize specialized digital twin tools to construct and visualize the model, and regularly update it with new data to maintain its accuracy.
Implement Real-Time Analytics
Utilize advanced analytics and machine learning algorithms to process data from the digital twin. This enables real-time insights into the vehicle’s performance, manufacturing processes, and potential issues. Real-time analytics facilitate the prediction of failures, enhancement of designs, and informed decision-making by utilizing the most current data.
Test and Validate
Conduct thorough testing and validation of the digital twins in automotive engineering model to ensure its accuracy and reliability. Compare the virtual model’s predictions with actual physical outcomes to identify discrepancies and refine the model accordingly. Continuous validation helps in maintaining the model’s precision and effectiveness over time.
Deploy the Digital Twin
After testing and validating the digital twin, the next step is to deploy it into the real automotive manufacturing environment. This involves setting up the digital twin to work alongside existing systems to monitor vehicle performance and production processes in real-time. Make sure the digital twin is fully integrated, continuously updated with live data from the production line and vehicle systems to offer actionable insights. This integration ensures that the digital twin helps optimize design and production effectively, adapting easily to new data and operational feedback.
Iterate and Improve
Use insights gained from the digital twin to iteratively improve both the design and manufacturing processes. Implement feedback loops where data from real-world usage informs design enhancements and process optimizations. This iterative approach ensures that the digital twin evolves with your needs and advances in technology, continuously enhancing performance and efficiency.
Challenges in Adopting Digital Twin in the Automotive Industry
Businesses face several challenges when adopting digital twin technology, including concerns around privacy, data consent, and potential inequalities. Navigating these issues is essential to ensure that the technology is implemented responsibly and ethically.
Organizations must also address the broader implications of data security and the equitable distribution of the technology’s benefits to avoid exacerbating existing disparities.
Challenge – Maintaining data consistency
One of the major challenges in digital twins in the automotive industry is maintaining data consistency. Implementing Digital Twin technology in automotive design and manufacturing requires integrating complex data from various sources. This can lead to data inconsistency and quality issues, affecting the accuracy of the digital twin.
Solution
Businesses should invest in advanced data management systems and ensure standardized data collection processes across all departments. Regular audits and data validation protocols can be implemented to maintain data accuracy and consistency.
Challenge- Synchronization Delays
Creating real-time synchronization between the physical and digital twin models in automotive manufacturing is challenging due to delays in data processing and system latency.
Solution
To overcome this, businesses should deploy high-performance computing solutions and optimize network infrastructure to reduce latency. Edge computing can be introduced to process data closer to its source, enabling faster real-time updates.
Challenge– Initial Investment Barrier
The high initial investment cost for implementing Digital Twin technology, including hardware, software, and skilled professionals, can be a major barrier for many automotive manufacturers.
Solution
To tackle the high initial investment cost associated with implementing Digital Twin technology in the automotive industry, businesses can adopt a phased implementation approach. Begin with pilot projects to test the technology on a smaller scale, which allows for evaluation without a substantial initial outlay.
Utilizing cloud-based Digital Twin solutions can further reduce costs by eliminating the need for extensive hardware investments and offering scalable pricing models. Collaborating with technology providers who offer bundled solutions, including hardware, software, and expertise, can also help mitigate expenses.
Challenge– Cybersecurity Risk
Cybersecurity risks increase with the implementation of Digital Twin technology, as sensitive data on automotive designs and processes become vulnerable to cyber threats.
Solution
Manufacturers should implement robust cybersecurity protocols, including data encryption, multi-factor authentication, and continuous monitoring of networks for threats. Regular cybersecurity training for staff can also help in mitigating risks.
Challenge– Skilled Workforce Gap
The automotive industry is struggling with a shortage of professionals who possess expertise in both automotive manufacturing and Digital Twin technologies. This lack of skilled workers hinders companies from fully implementing and benefiting from advanced Digital Twin solutions, limiting their potential for innovation and efficiency.
Solution
Businesses should invest in upskilling their workforce by providing specialized training in digital twin technology. Partnering with educational institutions or technology providers for certification programs can also help fill the talent gap.
Challenge– Integration Complexity
Integrating
Integrating digital twin technology with existing legacy systems in automotive manufacturing can be challenging and time-consuming. This process often leads to compatibility issues and disruptions in ongoing operations.
Solution
To address this, businesses should adopt a hybrid integration strategy, allowing for a gradual transition while maintaining the functionality of legacy systems. Using middleware platforms to bridge the gap between old and new technologies can facilitate smoother integration. Additionally, conducting pilot projects before full-scale implementation can help identify and resolve compatibility issues early on, minimizing disruption.
Future of the Digital Twin in Automotive Industry
The global market for digital twin market size was valued at $2.2 billion in 2022 and is expected to grow to $34.6 billion by 2032, representing a CAGR of 32.6% from 2023 to 2032.
The future of digital twin technology in the automotive industry promises to revolutionize vehicle development, manufacturing, and operations. As this technology evolves, it will enable unprecedented levels of precision and efficiency.
Digital twins in automotive are transforming the industry by creating highly detailed virtual models of vehicles and production systems. These simulations will allow automakers to predict wear and tear, improve safety features, and refine performance metrics based on real-time data inputs from operational vehicles.
Furthermore, Sustainability will also be a key focus, with automotive digital twin technology optimizing energy usage in both vehicle manufacturing and operation. The future will see greater adoption of automotive digital twins to design energy-efficient electric vehicles and manage battery systems, contributing to a greener automotive industry. As digital twin technology becomes more advanced, it will become a cornerstone of the automotive industry’s push towards a more intelligent, efficient, and sustainable future.
Appinventiv’s Expertise in Digital Twin Technology for Automotive Design and Manufacturing
We are a leading automotive software development company dedicated to helping businesses elevate their approach. We enable businesses to fully harness the potential of Digital Twin technology, driving transformative results and unlocking significant benefits.
Our tailored solutions offer real-time simulation and digital replication, helping businesses optimize production lines, enhance design precision, and reduce time-to-market.
With a deep understanding of the automotive industry’s complexities, we develop software that seamlessly integrates into existing systems, driving operational efficiency and innovation. From advanced data analytics to predictive maintenance, our scalable, secure platforms ensure that automotive businesses stay competitive and future-ready in this rapidly evolving landscape.
With over 9 years of experience as a premier automotive software development company, Appinventiv has a proven track record of delivering cutting-edge solutions to global automotive leaders. Backed by a team of 1600+ experts, we combine industry knowledge with technological prowess to drive innovation in automotive design, manufacturing, and beyond.
Connect with us to experience the transformative power of digital twins in the automotive industry, and drive optimal outcomes by leveraging the latest innovations in the industry. Let us help you revolutionize your business with advanced technology and tailored solutions.
FAQs
Q. What is a digital twin in the automotive industry?
A. A digital twin in the automotive industry is a virtual replica of a physical vehicle, system, or component that is used to simulate, monitor, and analyze its real-world performance. This technology integrates data from sensors and IoT devices within a vehicle to create a real-time, dynamic model that mirrors the vehicle’s operations and lifecycle. Digital twins help automotive manufacturers streamline processes, enhance maintenance, and improve vehicle performance.
Q. How does a digital twin improve automotive product design?
A. Digital twins improve automotive product design and development by enabling engineers to simulate and test different design concepts in a virtual environment before physically building the vehicle. This allows them to analyze how changes will impact performance, durability, and safety, and to optimize the design accordingly. The real-time feedback and predictive analytics from the digital twin reduce prototyping costs, speed up development cycles, and lead to higher-quality and more efficient vehicle designs.
Q. How does a digital twin help improve vehicle maintenance and operational efficiency?
A. A digital twin improves vehicle maintenance by continuously monitoring a vehicle’s condition through real-time data from embedded sensors. This data allows for predictive maintenance, identifying potential issues before they lead to breakdowns.
By simulating the performance of different components, digital twins enable manufacturers and fleet managers to optimize repair schedules, reduce downtime, and improve overall vehicle longevity. This leads to enhanced operational efficiency by minimizing unexpected failures and ensuring vehicles are running at peak performance.
Q. What role does a digital twin play in the development of autonomous vehicles?
A. In the development of autonomous vehicles, a digital twin serves as a virtual testing ground, enabling manufacturers to simulate complex driving scenarios and interactions with the environment without the risks associated with physical testing. This helps developers fine-tune algorithms, sensors, and control systems in a safe, cost-effective manner. Additionally, digital twins allow for real-time analysis of the vehicle’s decision-making process and system performance, leading to more reliable, efficient, and safer autonomous driving solutions.
Q. How can digital twin technology enhance supply chain management in automotive manufacturing?
A. Digital twin technology enhances supply chain management by providing a real-time, holistic view of the entire production process. By creating digital replicas of manufacturing operations, logistics, and supplier networks, companies can simulate and predict potential bottlenecks, delays, or disruptions in the supply chain. This enables more accurate demand forecasting, improved inventory management, and better coordination between suppliers and manufacturers. Ultimately, digital twins improve operational efficiency, reduce costs, and enhance decision-making in supply chain management.
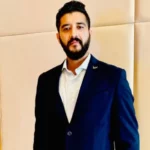
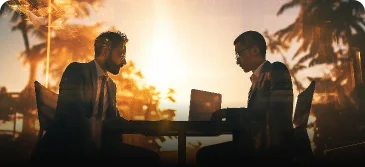
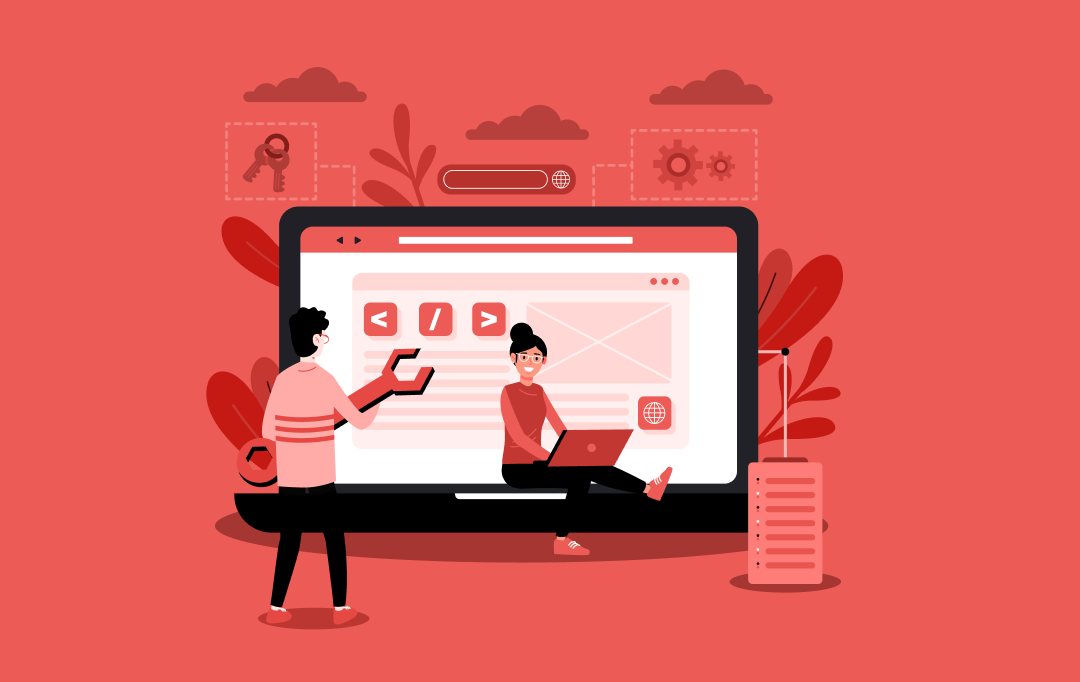
Custom Development or White Label Solutions: Which is Right for Your Business?
Key takeaways: 77% of companies are prioritizing digital transformation; the right tech approach is crucial for staying competitive. Custom development offers tailored solutions for unique needs, flexibility, and long-term scalability. Whereas, white-label solutions provide quick market entry, cost-efficiency, and easy customization for standard needs. Appinventiv’s expertise helps you navigate custom development vs white-label to choose…
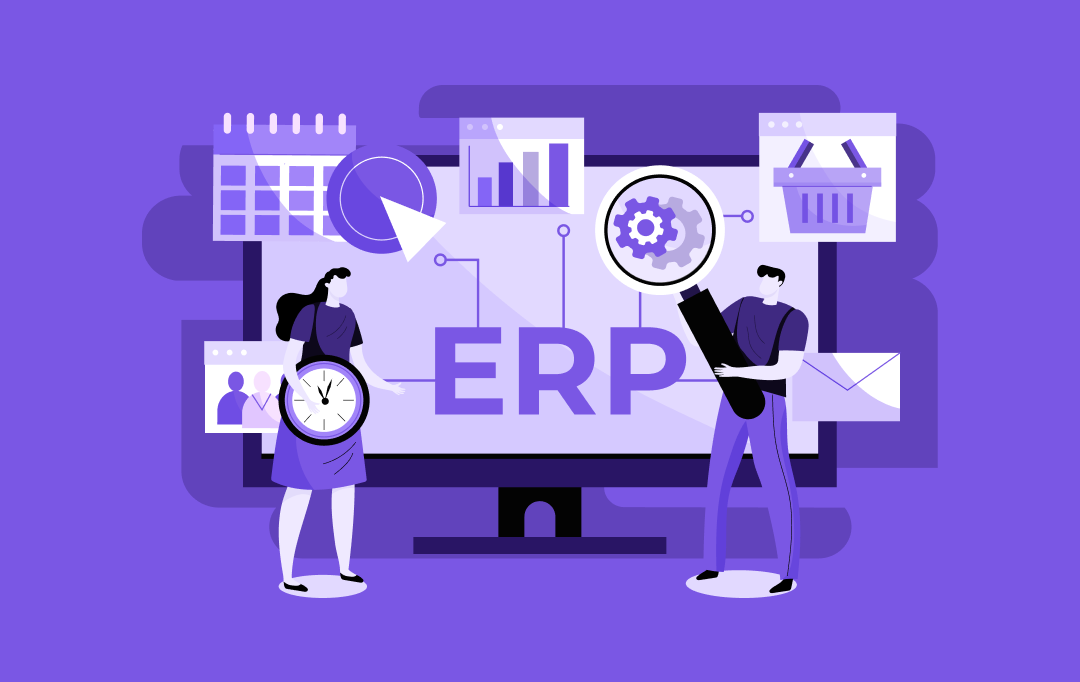
ERP Integration in Australia - Why It Is Essential and How to Do It Right
Key takeaways: ERP integration enables operational efficiency, reduced costs, and enhanced decision-making. Healthcare, finance, manufacturing, retail, and all the other sectors are benefiting from ERP integrations in Australia. While ERP integration can be costly, ranging from AUD 45,000 - AUD 450,000, it leads to significant long-term savings and scalability. Compliance with Australian regulations is critical,…
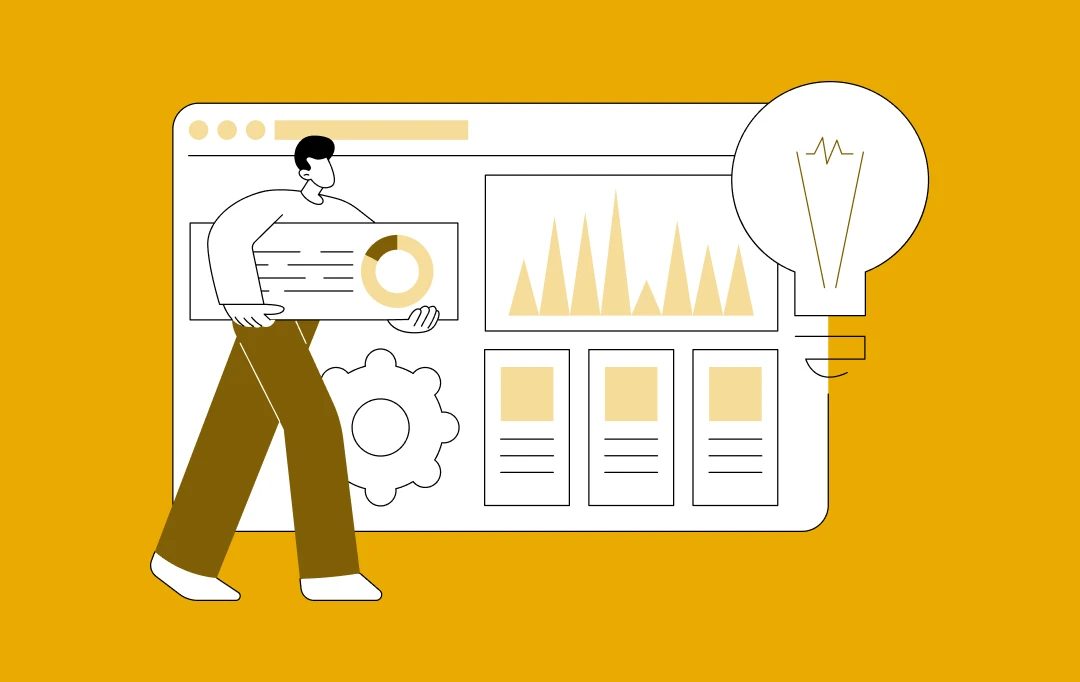
Predictive Analytics Software Development - Features, Benefits, Use Cases, Process, and Cost
Key Takeaways Predictive analytics helps businesses shift from “what has happened” to "what will happen," enabling proactive strategies rather than reactive ones. Real-time analytics and AI integration are driving the growth of predictive analytics, making it more accurate, accessible, and critical for business success. Custom predictive analytics solutions can enhance customer satisfaction, reduce costs, and…