- The Game-Changing Benefits of Digital Twin Technology in Modern Construction
- Improved Project Planning and Design
- Enhanced Construction Accuracy
- Real-time Monitoring and Management
- Increased Operational Efficiency
- Better Risk Management and Mitigation
- Cost Savings and Resource Optimization
- Use Cases of Digital Twins in Construction
- Construction Site Management and Safety
- Facility Management and Maintenance
- Asset Tracking and Management
- Sustainability and Energy Efficiency
- Smart Cities and Infrastructure Development
- Real-world Examples of Digital Twins in Construction
- Key Technologies Driving Implementation of Digital Twins in the Construction Industry
- Embrace Building Information Modeling (BIM)
- Adopt Drones for Site Surveys and Monitoring
- Implement IoT for Smart Construction
- Utilize Augmented Reality (AR) for Project Visualization
- Harness AI to Improve Project Outcomes
- Digital Twins in Construction: Future Trends and Innovations
- Harness Appinventiv’s Expertise for Cutting-Edge Digital Twin Solutions
- FAQs
In the construction industry, where projects are increasingly complex and timelines are tight, the need for advanced tools that enhance precision and decision-making is greater than ever. With rising demands for sustainability, efficiency, and cost control, companies are turning to innovative solutions to stay ahead. One such groundbreaking technology is the digital twin—a virtual replica of a physical asset that evolves alongside the real-world structure.
This sophisticated tech provides continuous, real-time data and insights, empowering construction teams to predict potential challenges, streamline processes, and ensure that every aspect of the project is meticulously managed from start to finish. Utilizing digital twin technology, construction companies enhance project outcomes by improving precision and efficiency, while also reducing costs and potential risks.
As per the Markets and Markets report, the digital twin market is projected to soar from $10.1 billion in 2023 to $110.1 billion by 2028, with a remarkable CAGR of 61.3% during this period. Numerous companies have begun integrating digital twin technology into their ecosystems. This data highlights significant opportunities for the construction industry to invest in digital twin solutions and reap substantial gains.
Here’s an in-depth exploration of how digital twins in construction are transforming the industry. Let’s uncover the essential benefits fueling this advancement.
Transform your business operations into a powerhouse of efficiency and innovation, driving unparalleled growth in a booming market
The Game-Changing Benefits of Digital Twin Technology in Modern Construction
Adopting digital twins in construction can give companies a competitive edge by driving innovation, improving project precision, and leading advancements in the field. Let’s dive into how digital twin technology in construction can transform operations and deliver substantial benefits.
Improved Project Planning and Design
Digital twins in construction allow teams to create highly detailed virtual models that reflect every aspect of the proposed build. This advanced modeling enables the simulation of different scenarios, helping identify potential design flaws and optimizing structural elements before construction begins.
By visualizing the project in its entirety, stakeholders can make more informed decisions, reducing the likelihood of costly design changes later on.
Enhanced Construction Accuracy
With digital twins, construction accuracy is significantly improved by providing a continuous, real-time comparison between the physical build and the digital model. This alignment ensures that the construction process stays true to the original design, minimizing deviations and errors. The ability to detect and correct discrepancies early on reduces the need for rework, saving time and resources while maintaining the integrity of the project.
Real-time Monitoring and Management
Digital twins in construction offer real-time visibility into every phase of the process, allowing project managers to monitor site conditions, track equipment and workforce performance, and adjust schedules as needed.
This real-time data integration helps in identifying and resolving issues promptly, ensuring that the project stays on track and within budget. Additionally, this continuous oversight enhances communication among stakeholders, fostering a more collaborative and efficient working environment.
Increased Operational Efficiency
By leveraging data from various sources, digital twins in construction streamline the process, enabling better coordination between different teams and automating routine tasks. This integration reduces delays caused by miscommunication or manual errors, allowing for smoother workflows and faster project completion.
The ability to analyze performance data in real-time also helps in optimizing resource allocation, ensuring that all aspects of the construction process are running at peak efficiency.
Better Risk Management and Mitigation
Digital twins construction is invaluable for proactive risk management, as they allow for the simulation of various construction scenarios to identify potential hazards before they occur. This predictive capability enables teams to develop effective mitigation strategies, reducing the likelihood of delays, accidents, or cost overruns.
By having a comprehensive understanding of possible risks, project managers can implement safety measures/software and contingency plans, enhancing overall project resilience.
Cost Savings and Resource Optimization
The use of digital twins in construction leads to significant cost savings by improving planning accuracy, reducing rework, and optimizing the use of materials and labor. By accurately predicting resource needs and identifying inefficiencies, digital twins help minimize waste and ensure that every dollar spent contributes to the project’s success.
Over the long term, these optimizations lead to a more sustainable construction process, reducing both the financial and environmental impact of building projects.
Use Cases of Digital Twins in Construction
Digital twins are revolutionizing the construction industry by providing highly detailed, real-time virtual replicas of physical assets and processes. These advanced models offer unparalleled insights and control over various aspects of construction, leading to more efficient, safer, and sustainable outcomes.
Construction Site Management and Safety
Digital twin construction is used to replicate the site in a virtual environment. This enables project managers to monitor site activities remotely, assess real-time site conditions, and simulate potential safety hazards. They can then implement immediate corrective actions based on the insights derived from the digital twin.
Facility Management and Maintenance
Facility managers use digital twins in construction to monitor building systems, such as HVAC, lighting, and security, by mirroring them in a virtual environment. This allows them to track performance in real-time, schedule maintenance activities based on actual usage data, and ensure that the facility operates within optimal parameters.
Asset Tracking and Management
Construction teams leverage digital twins to track the location, condition, and usage of assets like machinery, vehicles, and materials. The virtual model helps manage logistics, schedule maintenance, and allocate resources more effectively by providing an up-to-date view of asset status.
Sustainability and Energy Efficiency
Engineers and architects use digital twins in construction to model and simulate the energy performance of a building throughout its lifecycle. By adjusting variables in the digital twin, they can explore different design options and operational strategies to enhance energy efficiency and reduce environmental impact.
(Also read: How AI, IoT, and AR/VR Technologies are Helping Companies Achieve their Sustainability Goals)
Smart Cities and Infrastructure Development
Urban planners harness the potential of digital twin construction to model and manage infrastructure projects, from roads and bridges to utilities and public spaces. These virtual models enable the simulation of various scenarios, such as traffic flow or utility demand, helping planners optimize the design and operation of urban systems before physical implementation.
(Also read: The Role of IoT in Building Smart Cities – 10 Applications and Use Cases)
Real-world Examples of Digital Twins in Construction
Here are some real-life examples of how Digital Twin technology in construction empowers teams to overcome limitations, enhance efficiency, and achieve exceptional results. Let’s explore!
Bouygues Construction’s Smart Building Projects
Bouygues Construction has been leveraging digital twin technology in several of its smart building projects across Europe. By creating digital replicas of buildings, the company can monitor energy efficiency, optimize maintenance schedules, and improve occupant comfort.
For example, in the construction of the French Ministry of Defense’s new headquarters, Bouygues used a digital twin to ensure that the building met stringent security and energy efficiency requirements. This digital twin continues to be used for ongoing facility management, making it a vital tool in maintaining the building’s performance and sustainability.
Siemens’ Digital Twin for Singapore
Siemens created a digital twin for the city of Singapore to simulate urban environments. This digital twin allows for better planning and management of infrastructure projects, optimizing traffic flow, energy distribution, and environmental sustainability.
Royal BAM Group
Royal BAM Group, a prominent leader in construction and engineering, has adopted digital twin technology across various commercial and residential projects. This innovative approach involves creating detailed virtual replicas of physical buildings, which significantly enhances design accuracy by allowing for precise validation and adjustments before actual construction begins. During the construction phase, digital twins enable real-time tracking of progress, helping project managers monitor schedules and address potential delays promptly.
These real-world examples highlight how digital twins are being used to improve efficiency, safety, and sustainability in construction projects around the globe.
Key Technologies Driving Implementation of Digital Twins in the Construction Industry
Implementing digital twin strategies in construction involves adopting innovative technologies and processes that enhance efficiency, productivity, and overall project success. Here are six key approaches:
Embrace Building Information Modeling (BIM)
BIM allows for detailed 3D modeling and simulation of construction projects, enhancing planning, collaboration, and decision-making. To maximize the role of digital twins in construction, integrate them into your project workflows to visualize designs, detect clashes early, and manage construction timelines efficiently.
Adopt Drones for Site Surveys and Monitoring
Drones provide accurate aerial data and real-time monitoring, significantly enhancing site safety and project management. By integrating digital twins with drones in construction, you can conduct detailed topographic surveys, continuously monitor project progress, and gather valuable insights. This combination facilitates timely and informed decision-making, leading to more efficient and effective construction processes.
Implement IoT for Smart Construction
Digital twin technology in construction leverages IoT to create virtual replicas of physical construction sites. By integrating IoT sensors, you can monitor equipment usage, track environmental conditions, and manage resources more efficiently. This real-time data feeds into the digital twin, allowing for precise analysis and optimization. The result is reduced downtime, improved project outcomes, and a more connected, intelligent construction environment.
Utilize Augmented Reality (AR) for Project Visualization
Augmented Reality (AR) and Digital Twin technology create a powerful synergy in construction. Digital Twins offer a virtual replica of the project, providing real-time data and simulations. When AR overlays this digital model onto the physical site, it enhances visualization and understanding. This integration allows stakeholders to see how digital data interacts with the real world, improving communication and decision-making.
During site inspections, AR can display real-time updates from the Digital Twin, helping to spot discrepancies and ensure alignment with the planned design.
Together, AR and digital twins in manufacturing and construction sector streamline project management, making it easier to visualize, analyze, and resolve issues efficiently.
Harness AI to Improve Project Outcomes
Artificial Intelligence (AI) and digital twin technology can transform the construction industry by working together to enhance project outcomes. AI algorithms analyze data from the digital twin to predict potential issues such as delays, cost overruns, and maintenance needs.
By leveraging predictive analytics, AI can provide insights into how different factors will impact the project, allowing for better planning and decision-making. This synergy not only helps foresee and address potential challenges but also optimizes project execution and lifecycle management, leading to increased efficiency and reduced risks.
Digital Twins in Construction: Future Trends and Innovations
Digital twins are evolving rapidly, pushing the boundaries of what’s possible in the construction industry. Here are some cutting-edge trends and innovations poised to reshape the future:
Quantum Computing Integration
The advent of quantum computing is set to revolutionize digital twins by exponentially increasing their computational power. This will enable the simulation of highly complex scenarios that traditional computing struggles to handle, such as the real-time dynamics of large infrastructure projects or the interaction between multiple variables in smart cities.
Sentient Digital Twins
The concept of “sentient” digital twins is emerging, where digital twins evolve from passive replicas to active, self-learning entities. These advanced twins can autonomously adapt to changing conditions, make real-time decisions, and even optimize construction processes without human intervention. This could lead to a future where construction projects are self-managed to a significant extent.
Multi-Domain Digital Twins
Future digital twins will not be confined to a single domain but will integrate multiple disciplines, such as structural engineering, environmental science, and logistics. This cross-domain integration will create a holistic view of construction projects, allowing for more comprehensive analysis and better-informed decision-making.
Biophilic and Eco-Sensitive Simulations
With sustainability becoming a core focus, digital twins will increasingly incorporate biophilic and eco-sensitive designs. This trend will allow architects and builders to simulate how natural elements, like green walls or solar panels, interact with the environment, promoting designs that enhance occupant well-being and minimize environmental impact.
5D+ BIM Integration
Moving beyond traditional 4D BIM (Building Information Modeling), the future will see the adoption of 5D, 6D, and even 7D BIM, where digital twins integrate time, cost, sustainability, and facility management data. This multidimensional approach will provide unprecedented insights, allowing for the optimization of every aspect of a construction project, from design through to post-occupancy management.
Cognitive Digital Twins for Autonomous Construction
Cognitive digital twins, equipped with AI that mimics human cognition, are emerging. These twins will not only simulate and predict but also understand and reason about construction projects. They will enable autonomous construction machinery to perform tasks with minimal human oversight, from earthmoving to complex installations, transforming the construction site into an almost fully automated environment.
These future-focused trends underscore the potential of digital twins to not only revolutionize construction processes but also to create a more resilient, sustainable, and inclusive built environment. As these innovations come to fruition, they will redefine the possibilities of construction in the coming decades. Furthermore, digital twin in automotive industry as well as other industries will elevate their operational approach and experience the growth.
Harness Appinventiv’s Expertise for Cutting-Edge Digital Twin Solutions
Appinventiv is a premier construction software development company that specializes in creating robust, scalable, and customized software solutions tailored to the unique needs of the construction industry.
Our development approach focuses on a deep understanding of your project requirements, enabling us to design and deliver software that enhances project management, streamlines operations, and improves overall productivity.
We leverage the latest technologies, including AI and IoT, to integrate real-time data and predictive analytics into your construction processes. With a commitment to quality, security, and innovation, Appinventiv ensures that your software solutions are built to drive long-term success and efficiency in a competitive industry.
Contact us, and we’ll support you through every stage of your digital twin development process in construction.
FAQs
Q. What is an example of a digital twin in the construction industry?
A. An example of a digital twin in the construction industry is the virtual model of a building or infrastructure project that mirrors its physical counterpart in real-time.
For instance, during the construction of a smart building, sensors are embedded throughout the site, and the data they generate is used to create and update the digital twin. This allows for monitoring construction progress, simulating different scenarios, and optimizing operations.
Q. What is digital twin in construction?
A. A digital twin in construction is a virtual representation or exact digital replica of a physical asset, such as a building, bridge, or even an entire city. It integrates real-time data from various sources, such as sensors, BIM models, and IoT devices, to create a dynamic and interactive simulation of the asset. These digital replicas allow project teams to gain immersive access to critical building information, enabling faster collaboration, improved workflows, and optimized decision-making throughout the construction process.
Q. Why are digital twins important in construction?
A. Digital twins are crucial in construction because they address many industry challenges, such as low productivity, high error rates, and inefficient workflows. By providing real-time insights and simulating potential scenarios, digital twins reduce issues, minimize RFIs (Requests for Information), and enable predictive maintenance. They also enhance collaboration among stakeholders, streamline processes between contractors and trades, and improve overall project performance. When integrated with BIM, digital twins can help reduce costs, boost profitability, and increase the chances of winning competitive bids.
Q. How much does it cost to build a digital twin in construction?
A. The cost to build a digital twin construction software varies widely depending on the project’s scale, complexity, and the technology involved. For a mid-range project, you can expect costs to range from $40,000 to $450,000, covering advanced sensors, software, and continuous data integration. The overall cost is also influenced by factors such as the level of detail, data sources, and ongoing maintenance.
Q. What is a digital building twin?
A. A digital building twin is a virtual replica of a physical building that mirrors its structure, systems, and operations in real-time. It integrates data from various sources like IoT sensors, BIM models, and historical records to provide a comprehensive view of the building’s performance. This digital twin can be used for monitoring energy usage, optimizing HVAC systems, ensuring safety compliance, and planning renovations or expansions.
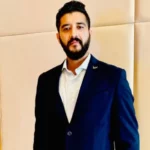
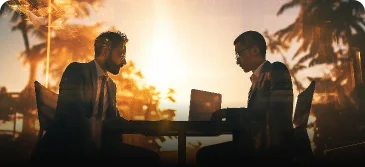
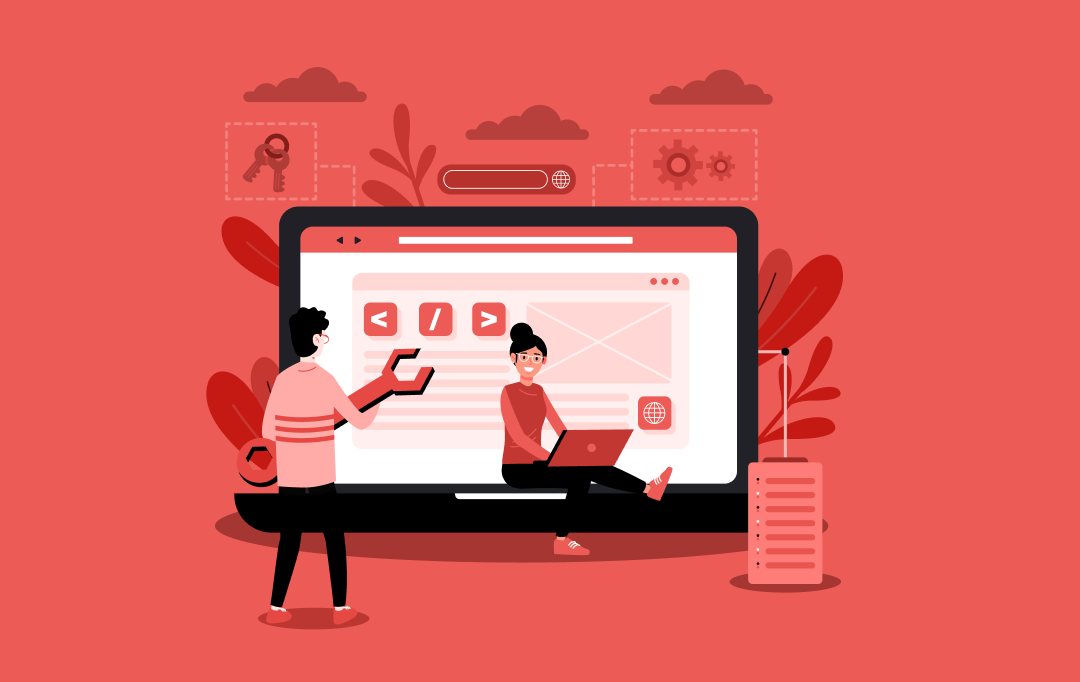
Custom Development or White Label Solutions: Which is Right for Your Business?
Key takeaways: 77% of companies are prioritizing digital transformation; the right tech approach is crucial for staying competitive. Custom development offers tailored solutions for unique needs, flexibility, and long-term scalability. Whereas, white-label solutions provide quick market entry, cost-efficiency, and easy customization for standard needs. Appinventiv’s expertise helps you navigate custom development vs white-label to choose…
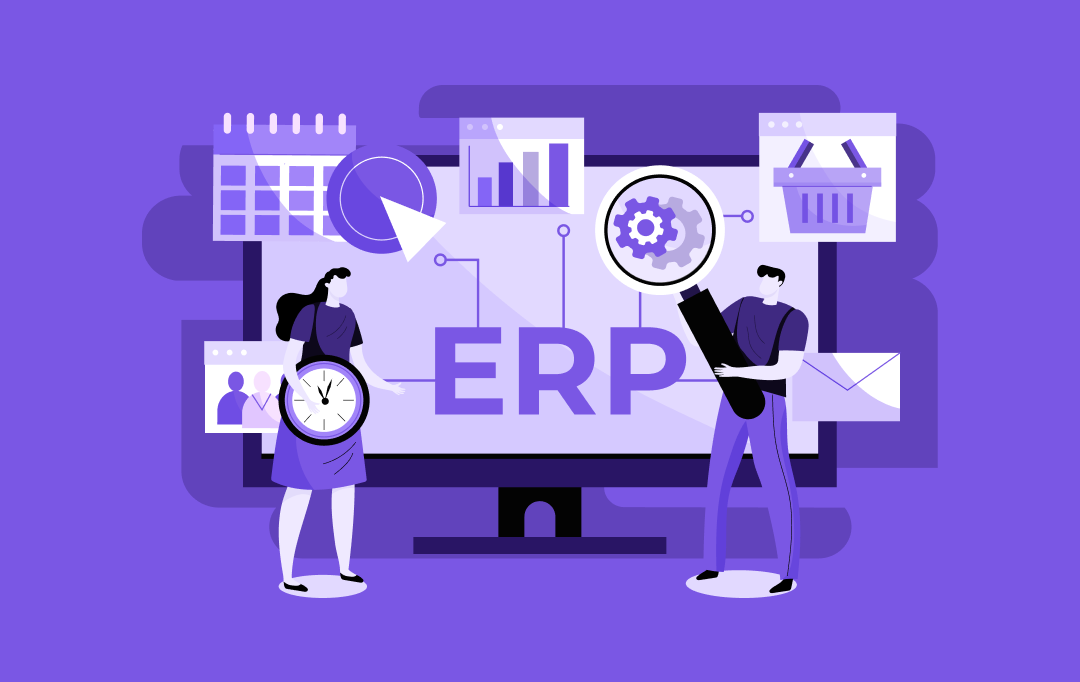
ERP Integration in Australia - Why It Is Essential and How to Do It Right
Key takeaways: ERP integration enables operational efficiency, reduced costs, and enhanced decision-making. Healthcare, finance, manufacturing, retail, and all the other sectors are benefiting from ERP integrations in Australia. While ERP integration can be costly, ranging from AUD 45,000 - AUD 450,000, it leads to significant long-term savings and scalability. Compliance with Australian regulations is critical,…
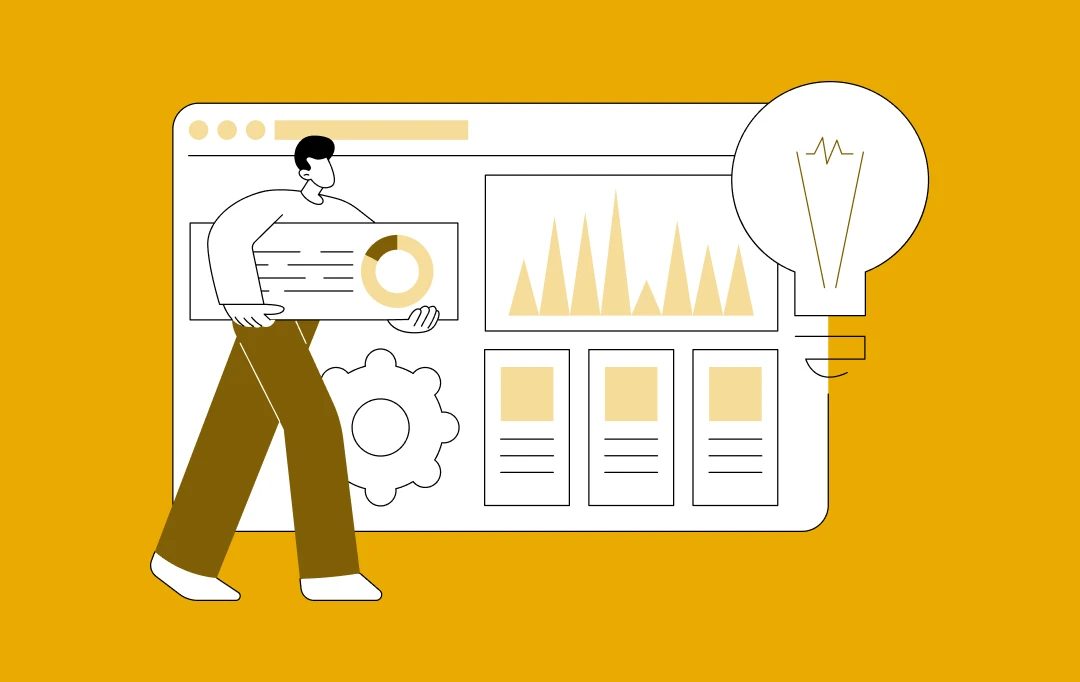
Predictive Analytics Software Development - Features, Benefits, Use Cases, Process, and Cost
Key Takeaways Predictive analytics helps businesses shift from “what has happened” to "what will happen," enabling proactive strategies rather than reactive ones. Real-time analytics and AI integration are driving the growth of predictive analytics, making it more accurate, accessible, and critical for business success. Custom predictive analytics solutions can enhance customer satisfaction, reduce costs, and…