- What is Digital Twin?
- Digital Twins Application in Aerospace
- Digital Twins in Aircraft Design
- Digital Twins in Aviation Maintenance
- Digital Twins For Enhancing Performance and Operations
- Real-World Digital Twin in Aerospace Examples
- Rolls-Royce's Use Digital Twins For Engine Monitoring and Maintenance
- Boeing's 787 Dreamliner Battery Safety Digital Twin
- Airbus' A350 XWB Performance Optimization
- Future of Digiltal Twins in Aerospace
- Bottomline
- FAQ’s
The aviation industry, like other sectors, plays a significant role in the economy of every country. Unfortunately, recent years have posed immense challenges for this industry, particularly in 2020 and 2021 during the COVID-19 crisis. Undoubtedly, the airline segment experienced a drastic downturn and incurred an enormous loss of $168 billion.
The aviation sector addressed challenges by embracing digital transformation as a solution. Companies within the industry recognized the benefits of investing in new technologies. These investments aimed to aid recovery and improve growth, efficiency, and safety.
Statista projects a remarkable increase in investment for digital transformation techniques and services. According to their projections, the investment is expected to grow from around $1.6 trillion in 2022 to $3.4 trillion by 2026. Within the aviation industry, a groundbreaking approach known as ‘Digital Twins’ has emerged as a powerful catalyst to address various challenges. This article explores the concept of digital twin in aerospace and its transformative role in aviation.
What is Digital Twin?
Digital twin in aerospace is at the forefront of innovation. It involves creating a virtual replica that mirrors physical objects, processes, or systems. This virtual model utilizes real-time or past data input and machine learning algorithms for analysis. By simulating various scenarios, it enables the prediction of system behavior. The insights gained from these simulations are conveniently presented through dashboards, reports, or visualization tools to inform decision-making effectively.
The aviation industry has greatly benefited from digital twin technology. These benefits of digital twin in aerospace include improved forecasting capabilities, advanced diagnostics, optimized fleet management, comprehensive lifecycle management, and enhanced overall operational performance. It is important to note that digital twins are particularly valuable in maintenance practices as they support scheduled, unscheduled, preventive, and predictive maintenance activities.
By identifying patterns and potential issues, proactive maintenance enables the reduction of aircraft downtime and improves operational efficiency. During the design stage, designers can utilize the digital twin’s virtual aircraft model to simulate various scenarios and experiment with new configurations before physically constructing prototypes. This approach helps to mitigate costs associated with physical testing and allows for more design iterations, fostering innovation and streamlining the aircraft design process.
Digital Twins Application in Aerospace
The aviation industry relies on digital twins due to the increasing complexity of modern airplanes. These technologically advanced aircraft incorporate cutting-edge features like avionics, fly-by-wire systems, and composite materials.
Digital replicas serve as invaluable tools for monitoring, analyzing, and optimizing the overall performance of contemporary planes. This efficient solution effectively addresses the challenges posed by these intricate technological advancements.
Through the use of virtual aircraft replicas, the aviation industry can enhance safety and performance. By implementing digital twins, engineers and decision-makers proactively monitor and maintain aircraft. This data-driven approach effectively minimizes risks while optimizing efficiency.
In addition, digital twin in aerospace offer a comprehensive and interconnected understanding of the condition, performance, and efficiency of aircraft. This is made possible by seamlessly integrating data gathered from various sensors and systems through IoT in aviation and data analytics. By providing real-time insights, this information empowers airlines and manufacturers with invaluable knowledge to make informed decisions and continually improve the aviation industry.
Digital Twins in Aircraft Design
Digital twin in aviation have made significant strides in aircraft design. These advancements have paved the way for virtual prototyping, optimized aerodynamics, improved structural enhancements, and more precise maintenance methods.
Virtual Prototyping
The digital twin in aerospace has revolutionized the aircraft design process by replacing time-consuming physical prototypes. These virtual replicas allow engineers to efficiently prototype and test their designs, utilizing advanced simulations to assess crucial aspects such as take-off, landing, and system response in various scenarios.
This approach offers rapid design iterations and minimizes costly modifications in later stages. As a result, it significantly accelerates the overall design process and enables the timely development of new aircraft.
Improved Efficiency and Performance
Aircraft fuel efficiency and performance heavily rely on aerodynamics. Engineers have the ability to utilize digital twin in aviation to simulate and optimize aircraft designs, with the ultimate goal of achieving maximum efficiency.
By conducting simulations, they can accurately identify areas of high drag and turbulence, enabling them to make precise adjustments that reduce drag, improve wing shapes, and enhance airflow control. This results in decreased fuel consumption and emissions and promotes the development of sustainable aircraft designs while pushing the boundaries of traditional testing methods.
Supported Architecture and Cost-Effective Supervision Techniques
Digital twins play a crucial role in maintaining the structural integrity of aircraft. Engineers rely on digital twins to analyze stress and fatigue by simulating manufacturing materials and components.
This enables them to accurately evaluate performance under various conditions and loads. By employing this data-driven approach, engineers can make well-informed decisions regarding materials and manufacturing processes. As a result, they strengthen the structure, enhance fuel efficiency, and reduce operational expenses.
By gathering and analyzing data from sensors on the aircraft, real-time monitoring becomes possible within the digital twin framework.
This valuable information is then used to strategize maintenance plans and detect potential issues early on, minimizing disruptions and optimizing maintenance schedules. As a result, overall maintenance costs are reduced as operational efficiency improves in the aircraft maintenance process.
Digital Twins in Aviation Maintenance
Digital twin in aviation is transforming aircraft maintenance. Through the utilization of predictive maintenance and real-time monitoring, these digital replicas play a pivotal role in reducing downtime, streamlining diagnostic processes, and optimizing repair activities.
Optimized Maintenance Schedules
Maintenance teams can use data from the digital twin in aerospace to analyze and optimize their maintenance schedules. This proactive approach empowers them to identify potential issues early, allowing for prompt replacement of parts when necessary. As a result, it helps prevent major failures and ensures uninterrupted aircraft availability to meet operational requirements.
Predictive Maintenance
Digital twins play a critical role in the field of predictive maintenance. With this, you can use real-time data and advanced AI algorithms to proactively identify potential issues within aircraft systems. By closely monitoring an aircraft’s performance and health through its digital twin, maintenance teams can swiftly detect signs of component degradation or future failures.
This proactive approach significantly mitigates the risk of unexpected breakdowns or costly disruptions, enabling timely and proactive maintenance and repair actions.
Real-time Monitoring
Maintenance teams have the ability to remotely monitor and analyze critical data on aircraft systems and components through digital twins. This advanced feature allows for real-time monitoring, facilitating immediate responses to important issues by providing instant access to diagnostic information.
By swiftly identifying and resolving underlying causes, it ensures efficient problem-solving. Additionally, the flexibility to make timely adjustments in maintenance procedures contributes to streamlined operations, ultimately enhancing overall reliability and operational efficiency in aircraft maintenance processes.
Also read: Digital Twins in Construction – Benefits, Use Cases, Implementation, and More
Digital Twins For Enhancing Performance and Operations
The use of digital twins enhances aircraft performance and operations, empowers pilots, and facilitates remote monitoring for improved operational efficiency.
Streamlining Pilot Training and Decision-Making
Digital twins are invaluable tools for pilot training and decision-making. They provide realistic and immersive flight simulators, allowing pilots to practice various scenarios and emergency procedures. These simulations enhance their skills, confidence, and ability to navigate challenging situations, proving highly beneficial.
Additionally, digital twins offer real-time data visualization that empowers pilots to make informed decisions during flights. This includes information on aircraft conditions, weather patterns, pre-planned flight paths, enabling prompt responses to changes and ensuring safe and efficient flights.
Optimizing Performance through Flight Data Analysis
Aviation experts employ digital twins to analyze extensive flight data and optimize aircraft performance. They create virtual prototypes of aircraft and their systems, closely monitoring various performance parameters and real-time flight data. This allows them to identify areas for improvement, resulting in optimized fuel consumption, reduced emissions, and enhanced overall aircraft efficiency. By utilizing digital twins for analyzing flight data, experts ensure that the aircraft operate at peak performance levels while adhering to strict safety standards.
Also read: AI-induced Resurgence for the Aviation Industry Amidst COVID-19
Digital Twins in Safety and Regulatory Compliance
In the aerospace industry, digital twins have become essential tools for enhancing safety and meeting rigorous regulatory standards. Aviation experts utilize advanced simulations and risk analysis to develop comprehensive virtual aircraft prototypes. These virtual models allow for evaluating various flight scenarios, identifying safety risks, and implementing effective risk mitigation strategies.
The aviation industry places utmost importance on compliance with strict legal regulations enforced by air travel authorities worldwide. In this regard, digital twins play a crucial role in assisting the industry to meet these rigorous compliance standards. Functioning as invaluable assets, they facilitate the monitoring and documentation of essential maintenance records and operational parameters. This capability effectively maintains a comprehensive virtual model of an aircraft’s flight, ensuring that all pertinent data is readily accessible for regulatory purposes.
The use of digital twins improves aircraft maintenance processes by simplifying them and reducing errors. This technology enables efficient planning of regular inspections, monitoring the lifespan of aircraft components, and facilitating timely repairs or replacements. By adopting this maintenance approach, the aviation sector ensures compliance and promotes enhanced safety and operational reliability.
Real-World Digital Twin in Aerospace Examples
Digital twins have gained immense popularity within the aviation industry, resulting in notable advancements and practical implementations across various operational areas. In aviation, digital twins are utilized to a great extent and have proven their efficacy in real-world scenarios. Here are some Digital twin in aviation examples that showcase how digital twins are applied within this industry:
Rolls-Royce’s Use Digital Twins For Engine Monitoring and Maintenance
Rolls-Royce, a prominent player in the aerospace industry, has revolutionized engine tracking and maintenance protocols by leveraging digital twins. This groundbreaking approach has set a new standard for the entire industry.
Rolls-Royce makes use of advanced digital twin in aerospace to replicate the behavior of their engines. They closely analyze performance data and predict potential irregularities or issues. By leveraging real-time data from integrated engine sensors, the digital twin in aviation acts as an early warning system. This proactive approach allows Rolls-Royce to schedule maintenance tasks accurately and efficiently, resulting in a significant reduction in unplanned downtime while also enhancing engine reliability and performance.
Rolls-Royce engineers can now remotely monitor and diagnose engine performance because of the utilization of digital twin in aviation. This technological advancement has accelerated the detection of potential problems and also facilitated swift and well-informed decision-making, ensuring seamless operations and optimal engine functionality.
Boeing’s 787 Dreamliner Battery Safety Digital Twin
Boeing utilized a digital twin in aviation to enhance the safety protocols of the 787 Dreamliner’s battery system. This proactive approach showcases a remarkable example of risk management in the aviation industry.
By employing digital twins in the case of the Dreamliner, Boeing closely monitored the behavior and performance of the aircraft’s battery system. This enabled real-time analysis to rapidly identify potential risks and enact necessary design changes, effectively reducing safety concerns related to the battery system. Embracing this proactive approach enhanced overall safety standards for the aircraft and mitigated potential safety incidents.
Incorporating digital twins into the design and development process had several benefits. Engineers and designers were able to identify and resolve potential problems early on, which ensured the highest levels of safety in the aviation industry. This dedication to safety is a hallmark of Boeing’s commitment. Additionally, such proactive measures minimized safety hazards, guaranteeing that the final design met strict safety standards. The use of digital twins explains how Boeing embraces advanced technology for safer aircraft production.
Airbus’ A350 XWB Performance Optimization
Airbus has improved the operational efficiency of its A350 XWB aircraft by employing digital twins. This innovative strategy has led to significant reductions in fuel consumption and emissions, thereby enhancing sustainability efforts.
Airbus employs digital twins to continuously monitor and analyze the real-time performance of their A350 XWB aircraft. By gathering data from various sensors and systems, they gain valuable insights into crucial operational factors including fuel consumption, engine efficiency, and overall aircraft performance. This extensive dataset assists Airbus in identifying areas for optimization, enabling informed decision-making based on data analysis to enhance overall performance.
Airbus utilizes data obtained through the digital twin to strategically modify their aircraft’s design, operation, and maintenance. These adjustments may include refining flight parameters, optimizing engine settings, and enhancing maintenance schedules. As a result, fuel consumption and emissions are significantly reduced, leading to improved efficiency and sustainability within the aerospace industry.
Airbus has improved efficiency, enhanced performance, and achieved significant cost savings by utilizing digital twins. This technological integration enables informed decision-making based on data analysis.
Future of Digiltal Twins in Aerospace
The aerospace industry is currently undergoing a significant transformation. Air force executives are increasingly embracing digital twin technology, as revealed by recent survey findings from Business Wire. An impressive 75% of these industry leaders express confidence in the potential benefits provided by digital twins. By utilizing large quantities of data from their existing offerings, these executives view digital twin technology in aerospace as an essential tool to address challenges within the aviation sector.
The survey findings reveal that these executives actively implement and evaluate digital twin technology. A significant number of them have smoothly integrated this advanced technology into their existing and future products and services, while others primarily use it for temporary aircraft testing.
To showcase the practicality of digital twin in aerospace industry, Vancouver International Airport (YVR) partnered with Unity’s Accelerate Solutions. Through this collaboration, they highlighted how YVR’s cutting-edge real-time 3D digital twin effectively addressed maintenance, sustainability, and safety concerns while minimizing operational disruptions. By providing employees with historical and real-time data, YVR’s digital twin enables them to explore different scenarios and optimize resource allocation. This aligns perfectly with the airport’s ambitious goal of achieving net-zero carbon emissions by 2030.
The convergence of confidence and practical implementation in the aviation industry suggests a promising future for digital twin technology in aerospace. This development has the potential to enhance efficiency, sustainability, and create an unparalleled travel experience.
Bottomline
The aviation industry has been completely transformed by digital twin technology. This revolutionary innovation has greatly improved aircraft performance, maintenance, and safety, making them more efficient and sustainable. The potential of digital twin in aerospace industry to drive efficiency and sustainability positions them as a critical player in shaping the future of aviation.
Are you searching for tailored digital solutions to enhance your aviation business? Look no further than Appinventiv, your trusted aviation software development company. Our expertise in the industry will help take your aviation technology to new heights.
FAQ’s
Q. What is digital twin in aerospace industry?
A. In the aerospace industry, a digital twin serves as a virtual replica of a physical aircraft or system. It encompasses real-time or historical data and plays an essential role in monitoring, analyzing, and optimizing aircraft performance. The utilization of digital twins enables companies to enhance operational efficiency and implement improved safety measures.
Q. What is an example of a digital twin?
A. Rolls-Royce adopts digital twin technology as a remarkable illustration. This innovative approach empowers them to oversee engine performance, streamline maintenance procedures, and accurately anticipate potential issues. By digitally replicating the behavior of their engines, Rolls-Royce effectively schedules maintenance tasks, resulting in enhanced dependability and reduced downtime.
Q. What role does a digital twin play in enhancing aircraft safety?
A. A Digital Twin in Aerospace plays a crucial role in enhancing aircraft safety by combining real-time monitoring and predictive maintenance. It proactively identifies and resolves potential issues, effectively preventing critical failures from occurring.
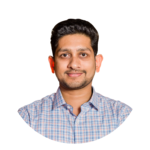
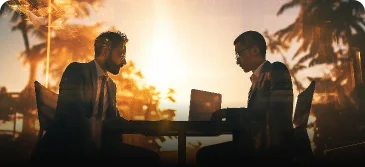
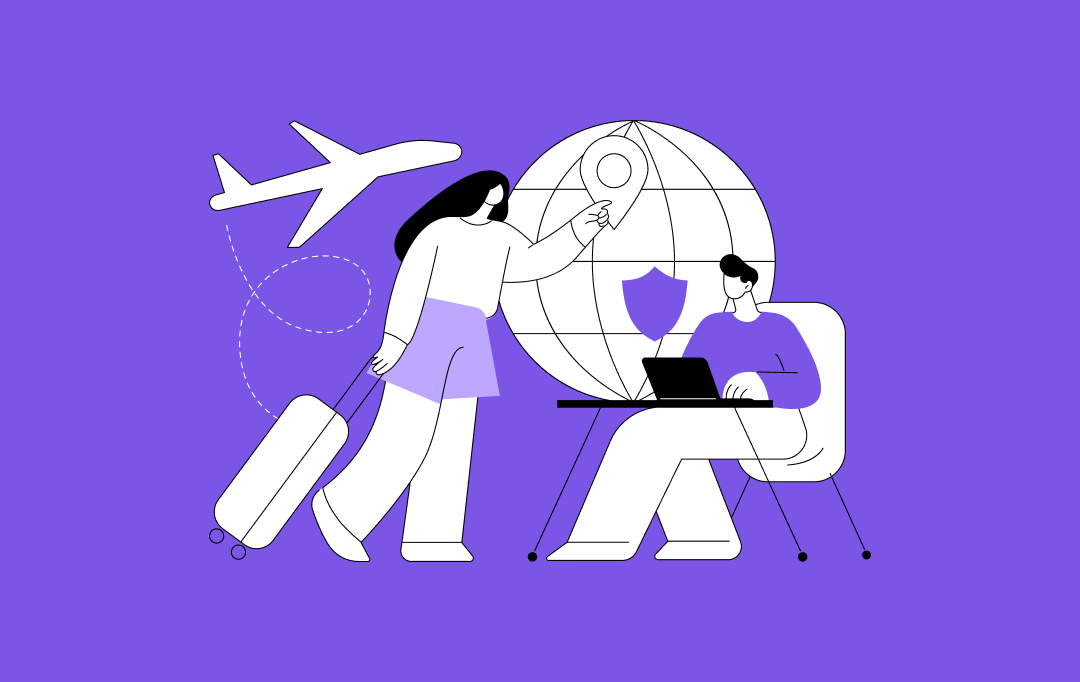
How Airlines Use Data Analytics for Enhanced Operational Efficiency - 10 Use Cases and Benefits
In today’s competitive airline industry, leveraging data analytics is not just an advantage but a necessity. Airlines face numerous challenges including fluctuating fuel costs, stringent regulatory requirements, and high customer expectations, all of which demand smarter, data-driven decision-making to enhance operational efficiencies and maintain profitability. Data analytics offers powerful solutions by enabling airlines to process…
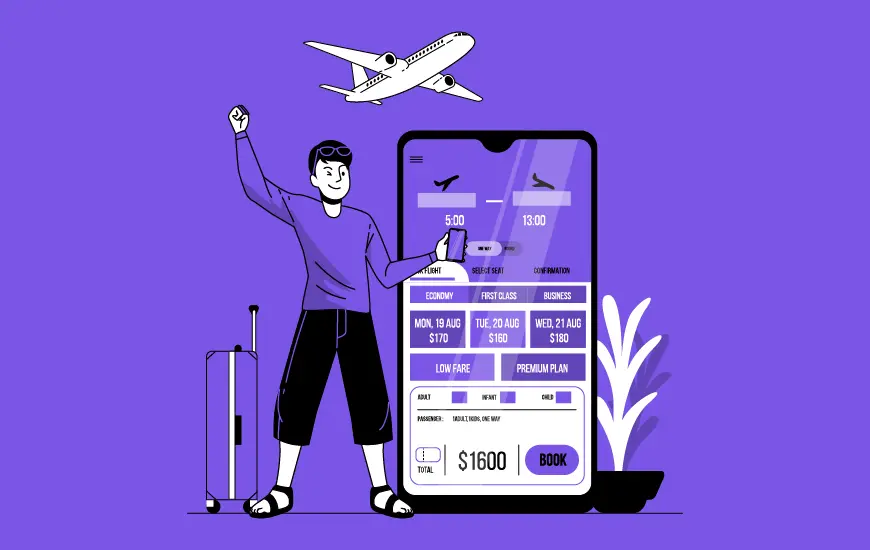
Flight Booking App Development Cost: Everything You Need to Know
As per recent reports, there are approximately 6.6 billion active smartphone users globally, making mobile apps ubiquitous in today's digital ecosystem. The exceptional revenue generated by these mobile apps has made them an important aspect of modern business. Interestingly, flight booking apps are also gaining instant popularity in the travel and tourism industry, whose market…
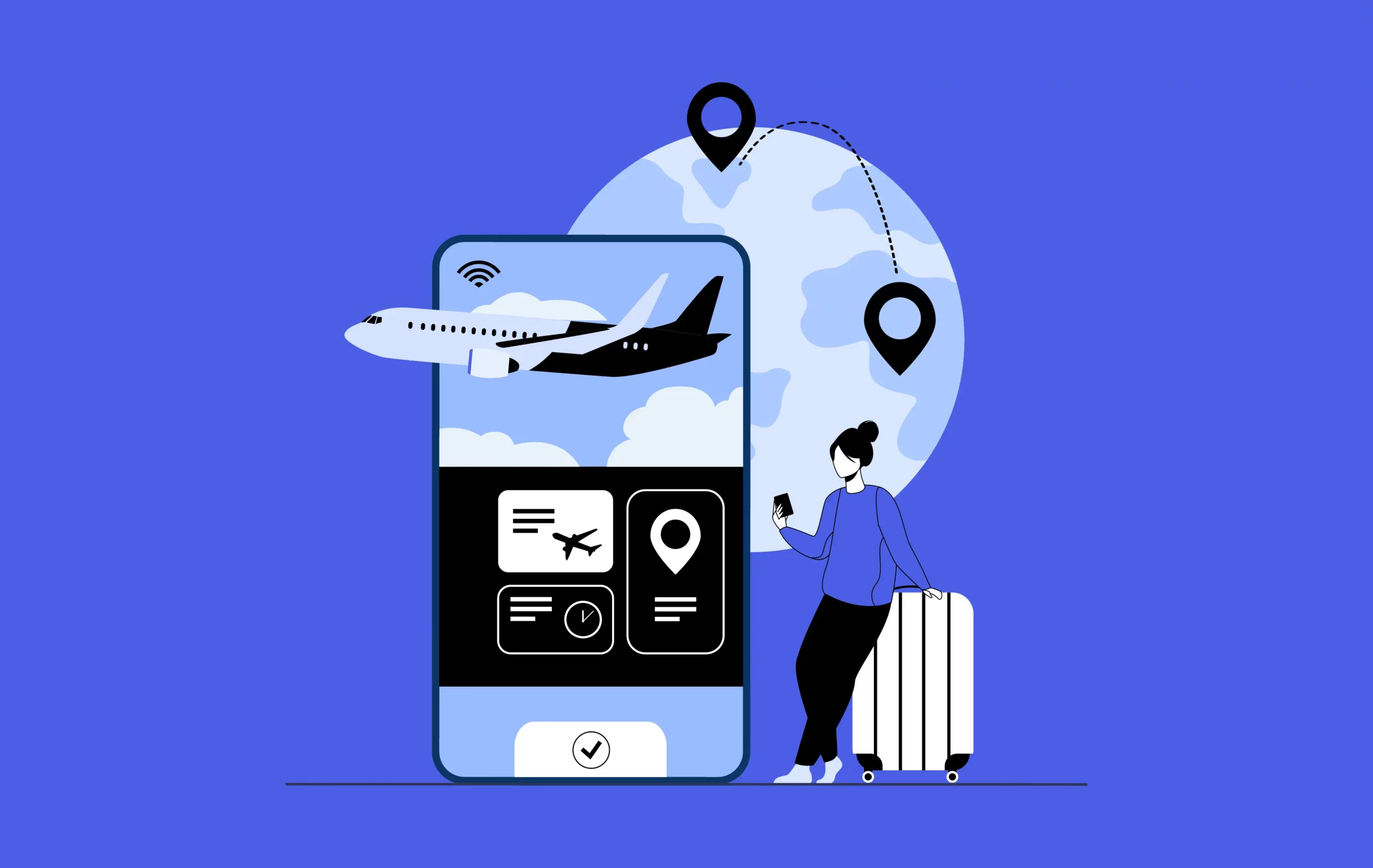
How Departure Control System in Airline Can Help in Cost Optimization
Imagine a situation where you had to visit five different counters to board a flight - all in a timeframe when you were late to the airport, and the flight was about to depart in 15 minutes. The reason why this scenario can only be a figment of our imagination in most scenarios is because…