- What is Manufacturing ERP?
- Key Types of Manufacturing ERP Systems
- Discrete Manufacturing ERP
- Process Manufacturing ERP
- Mixed-Mode Manufacturing ERP
- Make-to-Order / Engineer-to-Order ERP
- Make-to-Stock ERP
- Understanding ERP Deployment Methods
- Cloud ERP
- On-Premise ERP
- Hybrid ERP
- Benefits of Implementing ERP in Manufacturing Processes
- Accurate Data and Real-Time Insights
- Enhanced Quality Control and Regulatory Compliance
- Optimized Inventory Management
- Increased Operational Efficiency
- Cost Savings
- The Challenges Manufacturing Enterprises Face without ERP Systems
- Lack of Integration
- Limited Visibility and Decision-Making
- Manual Processes and Inefficiencies
- Poor Inventory Management
- Inefficient Production Planning
- Inadequate Compliance and Traceability
- How ERP Systems Improve Manufacturing Operations
- Streamlined Production Planning
- Streamlined Production Planning
- Optimized Inventory Management
- Integrated Supply Chains
- Optimized Operational Efficiency
- Is Manufacturing ERP Necessary for All Kinds of Companies?
- Process Manufacturing Companies
- Assembly Manufacturers
- Make-to-Order (MTO) and Engineer-to-Order (ETO) companies
- High-Volume and Mass Production Companies
- Multi-site and Global Manufacturers
- Contract Manufacturers
- How Can Businesses Develop a Robust Custom Manufacturing ERP System?
- Assess Business Requirements
- Hire a Reliable ERP Software Development Firm
- Evaluate Implementation Options
- Prepare for Implementation
- Execute the Implementation
- Get Post-Implementation Support
- How Can Appinventiv Help to Mitigate These Challenges?
- Data Migration Excellence
- Development and Integration Proficiency
- Process Customization
- Conclusion
- FAQs
In the dynamic realm of business, manufacturing enterprises encounter numerous challenges in effectively managing their operations. From overseeing the supply chain to tracking finances, the intricate nature of manufacturing processes necessitates a comprehensive solution capable of enhancing efficiency and streamlining operations.
This is precisely where Enterprise Resource Planning (ERP) software emerges as a game-changing tool for manufacturers worldwide. By integrating multiple facets of a company’s operations into one cohesive system, ERP software for manufacturing enterprises revolutionizes how manufacturers operate on a global scale.
The global ERP software market has witnessed significant growth in recent years. In 2022, its market size reached an impressive valuation of $54.76 billion. According to experts, this upward trend is projected to continue with a compound annual growth rate (CAGR) of 11.0% from 2023 to 2030. This data highlights the increasing recognition and adoption of ERP systems, particularly within the manufacturing industry.
Manufacturing ERP software development is now indispensable for enterprises. As stated by Mantas Vilkas in his book, Organizational Models for Industry 4.0, currently about 43% of organizations use ERP systems as they efficiently handle copious amounts of data generated by various processes.
So, here in this article, we will explore how ERP for manufacturing enterprises enhances operations and boosts efficiency. It delves into the key manufacturing ERP software features and functionalities designed specifically for the manufacturing sector.
But first, let’s start with the basics!
What is Manufacturing ERP?
Manufacturing ERP (Enterprise Resource Planning) constitutes a specialized software system devised exclusively to cater to the requirements and complexities of the manufacturing industry. It encompasses an all-inclusive suite of integrated applications and modules that empower manufacturers with efficient management and optimization of their operations.
Manufacturing resource planning software development encompasses a range of functionalities and features designed to meet the unique requirements of manufacturing processes. ERP solutions for manufacturing seamlessly integrates diverse aspects of a manufacturing enterprise, including production planning, inventory management, supply chain management, shop floor control, quality control, financial management, and more. By consolidating these functions within a centralized system, manufacturing ERP software solutions facilitate smooth data flow and efficient coordination across departments.
Key Types of Manufacturing ERP Systems
Manufacturing ERP systems come in various types, each designed to address specific production needs and workflows. From discrete to process manufacturing, selecting the right system can streamline operations and boost overall efficiency. Here are some of its key types:
Discrete Manufacturing ERP
Discrete manufacturing ERP is specifically tailored for industries that produce distinct items, like electronics, automotive parts, or machinery. These systems manage work orders, assembly lines, and detailed Bills of Materials (BOMs).
Process Manufacturing ERP
Ideal for industries such as food, chemicals, or pharmaceuticals, these ERPs focus on formulas and recipes, emphasizing batch production, compliance, and quality control.
Mixed-Mode Manufacturing ERP
Designed for manufacturers using both discrete and process methods, it is perfect for companies with diverse production needs or hybrid workflows.
Make-to-Order / Engineer-to-Order ERP
Built for custom and project-based manufacturing, these systems support personalized products, complex specifications, and engineering-driven production cycles.
Make-to-Stock ERP
Best for manufacturers who produce goods based on demand forecasts, this type of ERP focuses on inventory planning, scheduling, and maximizing production efficiency.
Understanding ERP Deployment Methods
Choosing the right ERP deployment method is a critical step in ensuring a successful implementation. Each approach offers unique benefits and considerations, depending on your organization’s size, goals, and technical infrastructure. Let’s have a look at those.
Cloud ERP
Cloud-based ERP solutions offer flexibility and scalability, allowing businesses to access their systems remotely. This deployment method reduces the need for costly on-premise infrastructure, providing businesses with real-time data, automatic updates, and enhanced collaboration across teams.
On-Premise ERP
On-premise ERP deployment offers complete control over data and system customization, making it ideal for businesses that require a tailored approach. With this method, organizations can manage their own servers and security, ensuring compliance with strict regulations and unique business needs.
Hybrid ERP
Hybrid ERP deployment offers the advantages of both cloud and on-premise systems, enabling businesses to keep critical data and processes on-site while leveraging cloud capabilities for scalability and cost efficiency. This model provides flexibility and is ideal for organizations looking for a balanced approach to data management and system performance.
Benefits of Implementing ERP in Manufacturing Processes
Implementing ERP systems in manufacturing streamlines operations, enhances data accuracy, and improves overall efficiency. Implementation of ERP in manufacturing processes offers a series of benefits, including:
Accurate Data and Real-Time Insights
Centralizing data within an ERP system ensures consistent and precise information across the organization. This provides real-time access to critical data, enhancing decision-making, improving forecasts, and allowing for better monitoring of production performance.
Enhanced Quality Control and Regulatory Compliance
ERP systems include comprehensive quality management features that monitor and control production processes. They ensure compliance with industry standards and regulations, support traceability, and help maintain high quality and regulatory adherence.
Optimized Inventory Management
ERP solutions offer advanced inventory management capabilities, including real-time stock tracking, automatic reorder points, and demand forecasting. This helps balance inventory levels, minimize overstock and shortages, and enhance the efficiency of the supply chain.
Increased Operational Efficiency
ERP systems automate and integrate key manufacturing functions such as order processing, production planning, and supply chain management. This reduces manual tasks, speeds up workflows, and reduces errors, ultimately boosting overall productivity and operational efficiency.
Cost Savings
ERP systems contribute to significant cost reductions by streamlining processes and managing resources more effectively. They reduce redundancies, decrease manual effort, and optimize resource use, leading to lower operational costs and improved profitability.
Also Read: How Much Does it Cost to Build a Manufacturing Analytics Software
The Challenges Manufacturing Enterprises Face without ERP Systems
Manufacturing without the use of ERP solutions can create various difficulties that hinder operational efficiency and overall business success. Some of the significant challenges worth noting include:
Lack of Integration
Manufacturers often face difficulties due to a lack of integration in their operations. Without an ERP system, they resort to using separate systems for different functions like production planning, inventory management, and financials. As a consequence, data silos are formed, leading to manual data entry and ineffective communication between departments. ERP manufacturing results in errors, delays, and reduced visibility into overall operations.
Limited Visibility and Decision-Making
In manufacturing operations, a significant amount of data is generated from various sources. However, without an ERP solution, accessing and analyzing this data can be time-consuming and challenging. Manufacturers often face difficulties obtaining real-time visibility into crucial information like inventory levels, production status, and financial performance. As a result, making informed decisions becomes hindered and responding promptly to changing customer demands or market conditions becomes difficult.
Manual Processes and Inefficiencies
In manufacturing environments where ERP solutions are absent, manual processes and paper-based systems prevail. These outdated methods are prone to errors, consume a significant amount of time, and rely heavily on paperwork. Consequently, they give rise to inefficiencies, delays, and increased administrative costs. Moreover, the reliance on manual processes obstructs opportunities for automation and hampers the effective scaling of operations.
Poor Inventory Management
When manufacturers don’t have an integrated ERP system, they encounter difficulties in effectively managing their manufacturing inventory. This leads to inaccurately tracked inventory levels, resulting in either stock outs or excess inventory. Moreover, the absence of real-time visibility into inventory can cause production delays, increased carrying costs, and missed sales opportunities.
Inefficient Production Planning
Manufacturing companies that do not employ ERP solutions for operations often face challenges with inefficient production planning and scheduling. In the absence of a centralized system, coordinating production activities becomes arduous, leading to suboptimal resource allocation, extended lead times, and increased costs.
Inadequate Compliance and Traceability
Inadequate compliance and traceability pose significant challenges for businesses that do not utilize an ERP system. Without this system in place, the task of tracking and documenting quality control measures, managing regulatory requirements, and ensuring product traceability becomes manual and prone to errors. This raises concerns about potential non-compliance issues and customer dissatisfaction for manufacturers.
How ERP Systems Improve Manufacturing Operations
ERP software for manufacturing enterprises plays a crucial role in enhancing their operations. It achieves this by streamlining processes and improving efficiency. Let’s explore some key ways in which ERP software for manufacturing industry brings massive improvement to operations:
Streamlined Production Planning
Streamlined Production Planning
In the manufacturing industry, effective production planning holds immense significance. It relies on efficient resource utilization and accurate scheduling to ensure smooth operations. To streamline this crucial process, manufacturers can rely on the manufacturing ERP system development process.
As an example, Ford Motor Company implemented an ERP system to integrate various aspects of its production process, including supply chain management, inventory control, and production planning. With real-time visibility into inventory levels and material availability, Ford optimized its production schedules, reduced bottle necks, and ensured timely deliveries.
Optimized Inventory Management
Manufacturers recognize the significance of efficient inventory management for maintaining optimal stock levels, minimizing costs, and avoiding inventory shortages or surpluses. ERP software for the manufacturing industry offers comprehensive features to handle inventory by enabling real-time visibility, tracking stock movements, and automating reordered points. With accurate inventory data, manufacturers can make well-informed decisions pertaining to procurement, production, and order fulfillment.
3M, for example, adopted an ERP solution to improve operational efficiency and supply chain management. With the ERP system in place, 3M could accurately monitor inventory levels and automate the reordering process. This approach enabled 3M to reduce carrying costs while ensuring that essential materials were always available for production. As a result, downtime was reduced, productivity improved.
Integrated Supply Chains
An efficient supply chain management enables seamless coordination with suppliers, reduces lead times, and enhances overall operational efficiency. In this regard, manufacturing ERP system development plays a crucial role by integrating supply chain processes. They allow businesses to collaborate effectively with suppliers, monitor order statuses in real-time, and track shipments effortlessly.
Additionally, ERP systems play a pivotal role in streamlining procurement processes. They facilitate seamless communication with suppliers while also offering valuable insights into supplier performance. These advantages not only help mitigate human errors but also minimize delays and ensure the prompt delivery of materials.
Optimized Operational Efficiency
Efficient supply chain management allows for seamless coordination with suppliers, reduces lead times, and improves overall operational efficiency. For instance, Lockheed Martin, a renowned global aerospace and defense company, integrated ERP software development into its manufacturing processes. This strategic move aimed to optimize their supply chain and production operations.
By utilizing the ERP system, real-time data on materials status, production schedules, and supplier performance became readily available. Consequently, Lockheed Martin was able to make informed decisions and enhance collaboration with suppliers. The result? A streamlined supply chain management system that led to significant cost reductions and improved delivery times.
[Also Read: Cloud ERP Integration: Costs, Types, Benefits]
Is Manufacturing ERP Necessary for All Kinds of Companies?
ERP software for Manufacturing enterprises play a crucial role in supporting companies across diverse sectors involved in manufacturing operations. There are several types of companies that can experience significant advantages of ERP-based manufacturing software development. These include:
Process Manufacturing Companies
Manufacturing ERP software simplifies the management for process manufacturers. It helps them handle complex recipes/formulations, track batch production, maintain quality control standards, ensure compliance with regulations, manage ingredient traceability, and optimize production schedules. Additionally, it offers assistance with inventory management, supplier management, and financial control.
For example, The COFCO Coca-Cola company, a prominent player in the beverage industry, relies on SAP ERP Central Component (ECC) for its manufacturing operations. This comprehensive suite of core components enables Coca-Cola to efficiently manage various aspects of its business. From financial management and sales, to production planning and human resources, these components ensure seamless coordination across departments and enhance productivity. By leveraging the capabilities of ERP, Coca-Cola streamlines operations and ensures the delivery of high-quality products and services to its customers.
Assembly Manufacturers
Manufacturing ERP systems offer a multitude of benefits to assembly manufacturers. One notable example is Boeing, a renowned aerospace company, which harnessed the power of manufacturing ERP software to streamline their intricate production processes. Given the complex nature of their assembly lines and the vast number of components involved, Boeing recognized the need for a robust ERP system to optimize inventory management, track production schedules with precision, and ensure timely deliveries of their aircraft.
In addition to these critical functions, ERP systems play a crucial role in streamlining operations for assembly manufacturers by facilitating efficient production planning, managing bills of materials (BOM), tracking component availability, optimizing production schedules, coordinating sub-assembly processes seamlessly, and ensuring accurate order fulfillment. Furthermore, ERP software proves invaluable in tasks such as inventory control, warranty tracking, and after-sales service management.
Make-to-Order (MTO) and Engineer-to-Order (ETO) companies
Manufacturing ERP software development provides comprehensive support to MTO and ETO companies. It effectively manages customer orders, tracks project timelines, coordinates production activities, handles engineering changes, and facilitates seamless communication across departments. By optimizing production resources and handling supply chain complexities, this software ensures the on-time delivery of customized products.
High-Volume and Mass Production Companies
Manufacturing ERP software supports high-volume and mass-production companies by assisting in various essential functions. These include production scheduling, capacity planning, demand forecasting, material requirements planning, quality control, and lean manufacturing practices.
By leveraging these capabilities, the software enables businesses to reduce production costs, enhance productivity levels, maintain consistent product quality standards, and achieve economies of scale.
Multi-site and Global Manufacturers
Manufacturing companies operating across multiple locations or on a global scale encounter various challenges in their operations, including managing facilities, coordinating activities, and ensuring data consistency. To tackle these complexities, the implementation of manufacturing ERP systems offers centralized control and real-time visibility throughout different locations, ultimately enhancing coordination and efficiency.
Contract Manufacturers
Manufacturing ERP software development helps contract manufacturers enhance operational efficiency. One notable example is Foxconn, a leading contract manufacturer in the electronic devices industry. They relied on robust manufacturing ERP solutions to effectively manage their contract manufacturing activities across various electronic devices. These solutions offered comprehensive features such as handling multiple customers, tracking specific requirements for each customer, managing production orders, overseeing sub-contracting activities, and providing valuable insights into cost analysis and profitability for individual contracts. By leveraging ERP software, contract manufacturers can streamline their operations, boost customer satisfaction levels, and ensure the efficient execution of projects.
How Can Businesses Develop a Robust Custom Manufacturing ERP System?
Building a custom manufacturing ERP system involves various critical steps. From assessing precise requirements to planning and executing the implementation, companies must pay heed to every step to build a successful ERP system.
Assess Business Requirements
To start, it is important to carefully assess your company’s specific needs and expectations in relation to a manufacturing ERP system. This evaluation should consider factors such as the size of operations, required functionalities, integration needs, and budget constraints.
Hire a Reliable ERP Software Development Firm
Prioring to hiring an ERP development company for manufacturing, businesses should conduct a thorough investigation. This involves considering factors like the company’s track record, previous projects, industry experience, features, scalability options, customization opportunities, and support services.
Evaluate Implementation Options
When evaluating implementation options, one should consider different deployment methods. These options comprise on-premises, cloud-based, or hybrid solutions. The choice depends on control, costs, scalability, and data security.
Prepare for Implementation
To ensure effective implementation, a collaborative effort between the business and the hired development firm is essential. The first step involves working together to develop a comprehensive plan that encompasses stakeholder engagement, project milestones, data migration, training initiatives, and change management processes.
Execute the Implementation
The implementation needs to be executed by following the detailed plan. It is essential to work closely with the ERP development company throughout the process, ensuring system configuration, data migration, training, testing, and integration with other systems are properly handled.
Get Post-Implementation Support
The process of executing the system and providing support after its implementation involves various stages. These include conducting final testing, launching the system, monitoring performance, getting ongoing support and training, addressing any arising issues, and establishing mechanisms for continuous improvement.
How Can Appinventiv Help to Mitigate These Challenges?
Appinventiv, a leading custom manufacturing ERP software development service provider, possesses the necessary expertise to address the challenges associated with building and implementing manufacturing ERP. Let’s explore how Appinventiv can assist in overcoming these hurdles:
Data Migration Excellence
Data migration expertise is a specialty of Appinventiv. We have proven proficiency in managing intricate data migration processes. With the utilization of robust methodologies and cutting-edge tools, we ensure a seamless and precise transfer of data from legacy systems to the new Manufacturing ERP. This approach minimizes disruptions and mitigates any potential issues with data integrity.
Development and Integration Proficiency
Appinventiv specializes in designing and developing ERP systems that seamlessly integrate with existing systems. With our extensive experience in developing interfaces and data exchange protocols, we ensure efficient integration with accounting software, inventory management systems, and CRM systems. This enables smooth data flow and seamless system interoperability.
Process Customization
Appinventiv recognizes the significance of aligning the ERP system with unique business processes. We demonstrate expertise in custom manufacturing ERP software to meet specific business requirements, effectively balancing standardization and flexibility.
For instance, one success story highlighting our capability is the ERP solution we built for IKEA. This ERP solution enables walk-in customers to access the store’s product catalogs right from store-erected tablet panels. This two-fold solution not only offers customers an in-store catalog solution but also uses their information as a marketing asset. This level of customization helps businesses like IKEA streamline their operations and deliver a personalized experience to customers.
Conclusion
Manufacturing ERP software development is crucial in the manufacturing industry. It helps streamline operations, maximize efficiency, and tackle challenges like resistance to change, data migration, integration issues, and more. By embracing custom ERP development for manufacturers, businesses can optimize production planning, improve inventory management, enhance supply chain coordination, and boost operational efficiency. Ultimately, adopting Manufacturing ERP is vital for companies striving to remain competitive and achieve sustainable growth in today’s dynamic market.
Connect with our experts to develop a custom ERP solution now.
FAQs
Q. What is an ERP system in manufacturing?
A. In manufacturing, ERP software serves multiple purposes. It aids in production planning, inventory management, supply chain coordination, quality control, financial management, and overall operational streamlining. Its implementation leads to enhanced efficiency and productivity.
Q. How does ERP software in manufacturing work?
A. ERP software in manufacturing operates by integrating different business functions into a centralized system. This centralization allows for real-time data sharing and analysis, streamlining processes, and facilitating efficient coordination across departments. The end result is improved productivity and better decision-making capabilities.
Q. What is the manufacturing ERP software development cost?
A. The cost of developing an ERP software for manufacturing enterprises can vary significantly. Typically, it ranges from $20,000 to $350,000 or even more. It is crucial to note that the final price depends on various factors, including project complexity, required modules, and the location of the Enterprise software development company. Connect with our experts to get precise cost estimates for your project.
Q. What is the difference between a manufacturing ERP and standard ERP?
A. A manufacturing ERP is tailored to the specific demands of production environments, focusing on areas like inventory control, production scheduling, and quality management. It integrates directly with manufacturing processes to enhance efficiency and resource use. Conversely, a standard ERP system provides general functionalities for diverse industries, including finance, HR, and sales, but may not include the specialized tools required for effective manufacturing management.
Q. What are some of the key features of manufacturing ERP?
A. Manufacturing ERP systems typically include features such as:
- Production Planning & Scheduling
- Inventory & Supply Chain Management
- Bill of Materials (BOM) Management
- Quality Control & Compliance
- Shop Floor Control
- Demand Forecasting
Integration with Finance & HR
Q. What are some of the top examples of ERP software?
A. Here are some of the leading ERP solutions used in manufacturing and other industries:
- SAP S/4HANA: A robust, enterprise-grade ERP widely used in large-scale manufacturing.
- Oracle NetSuite: A flexible, cloud-based ERP suited for growing manufacturers.
- Microsoft Dynamics 365: Offers modular solutions for manufacturing, operations, and finance.
- Infor CloudSuite Industrial (SyteLine): Designed specifically for complex manufacturing needs.
- Epicor ERP: A strong choice for mid-sized manufacturers with industry-specific capabilities.
- Odoo: Odoo is an open-source ERP with customizable modules for manufacturing and inventory.
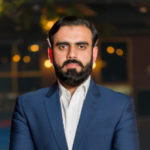
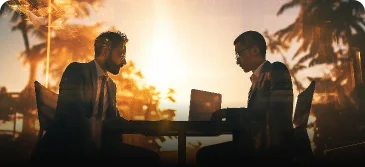
- In just 2 mins you will get a response
- Your idea is 100% protected by our Non Disclosure Agreement.
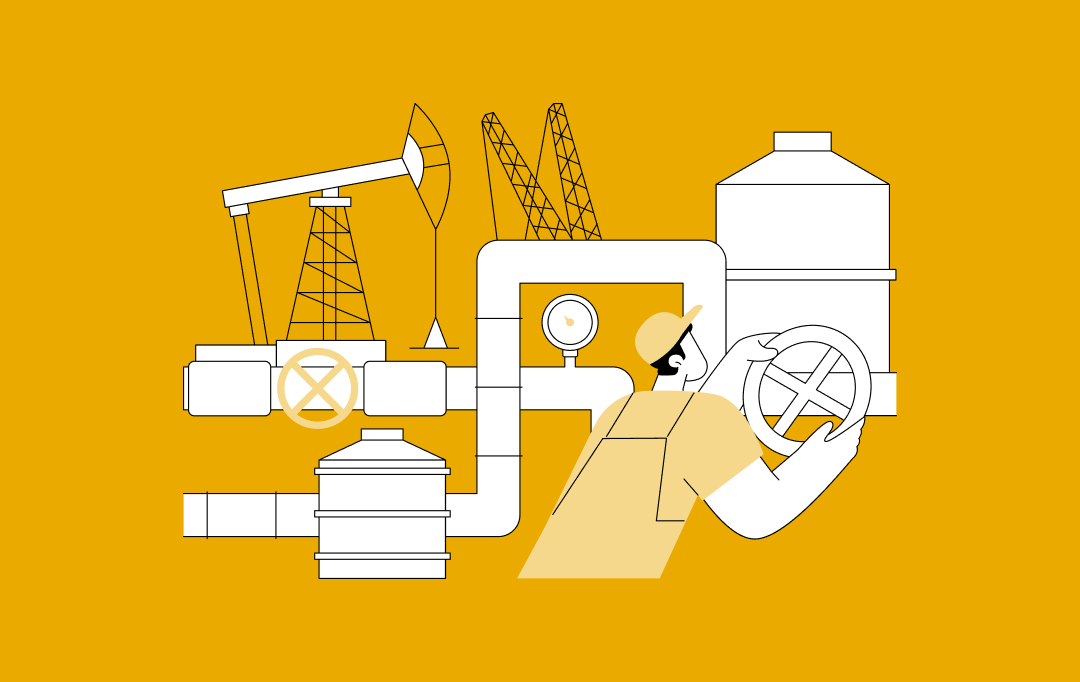
Oil and Gas ERP Software Development: Features, Benefits, Process, Integration and more
The oil and gas industry operates in a complex and volatile environment. It involves oil and gas exploration, extraction, drilling, production, and transportation. Consequently, the industry faces several challenges, such as fluctuating market demands, stringent regulatory requirements, and the constant pressure to reduce greenhouse gas emissions. Notably, oil and gas production, transport, and processing contribute…
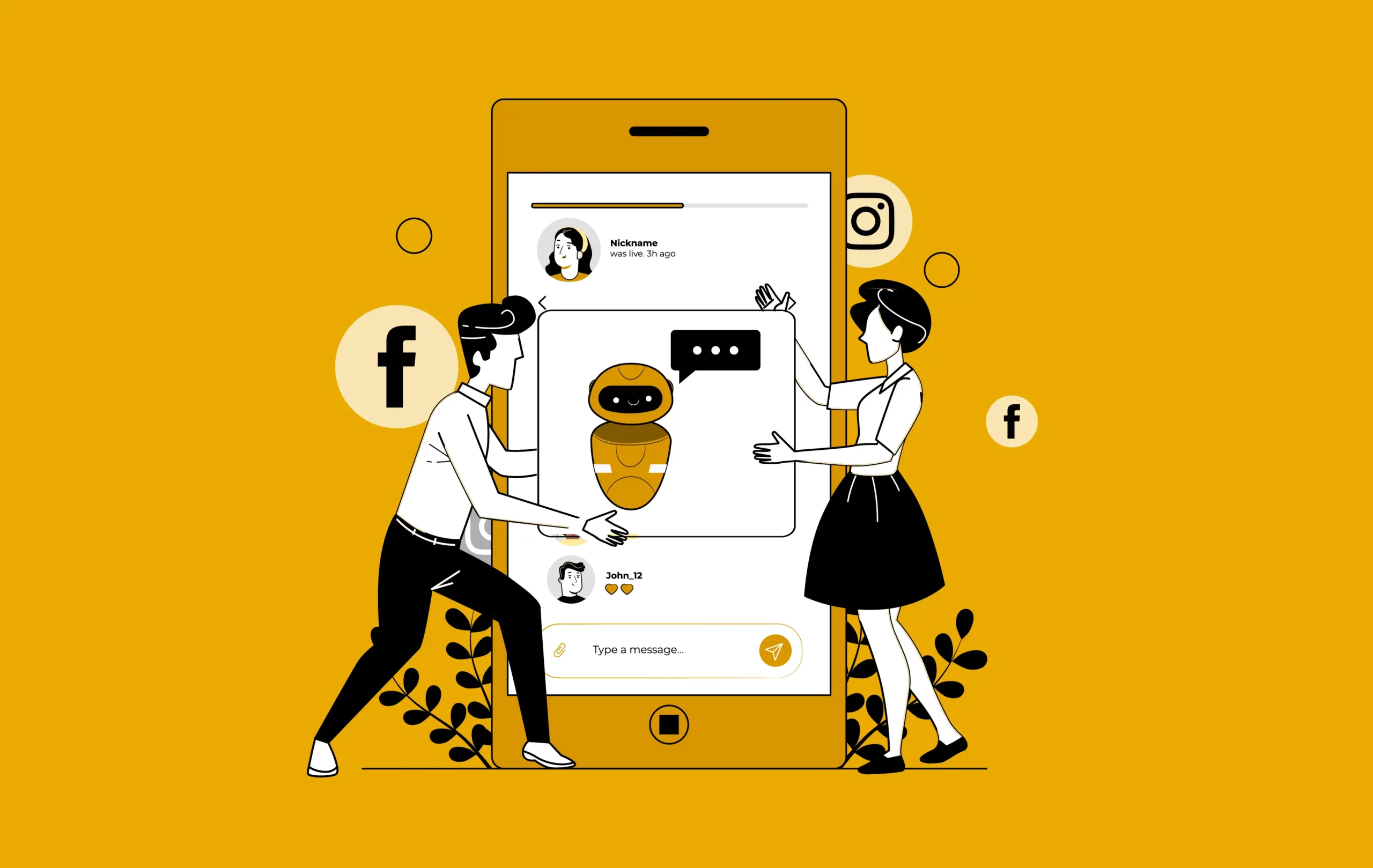
How ERP AI Chatbots Are Reshaping Enterprise Workflows
Key takeaways: ERP AI chatbots turn slow, manual ERP tasks into instant, automated actions. Real-time data, voice commands, and multi-system access make ERP chatbots a game changer. Leading brands like H&M, Unilever, and PepsiCo are already leveraging ERP AI chatbots. AI chatbots improve user adoption by simplifying complex ERP navigation. Challenges like integration, scalability, and…
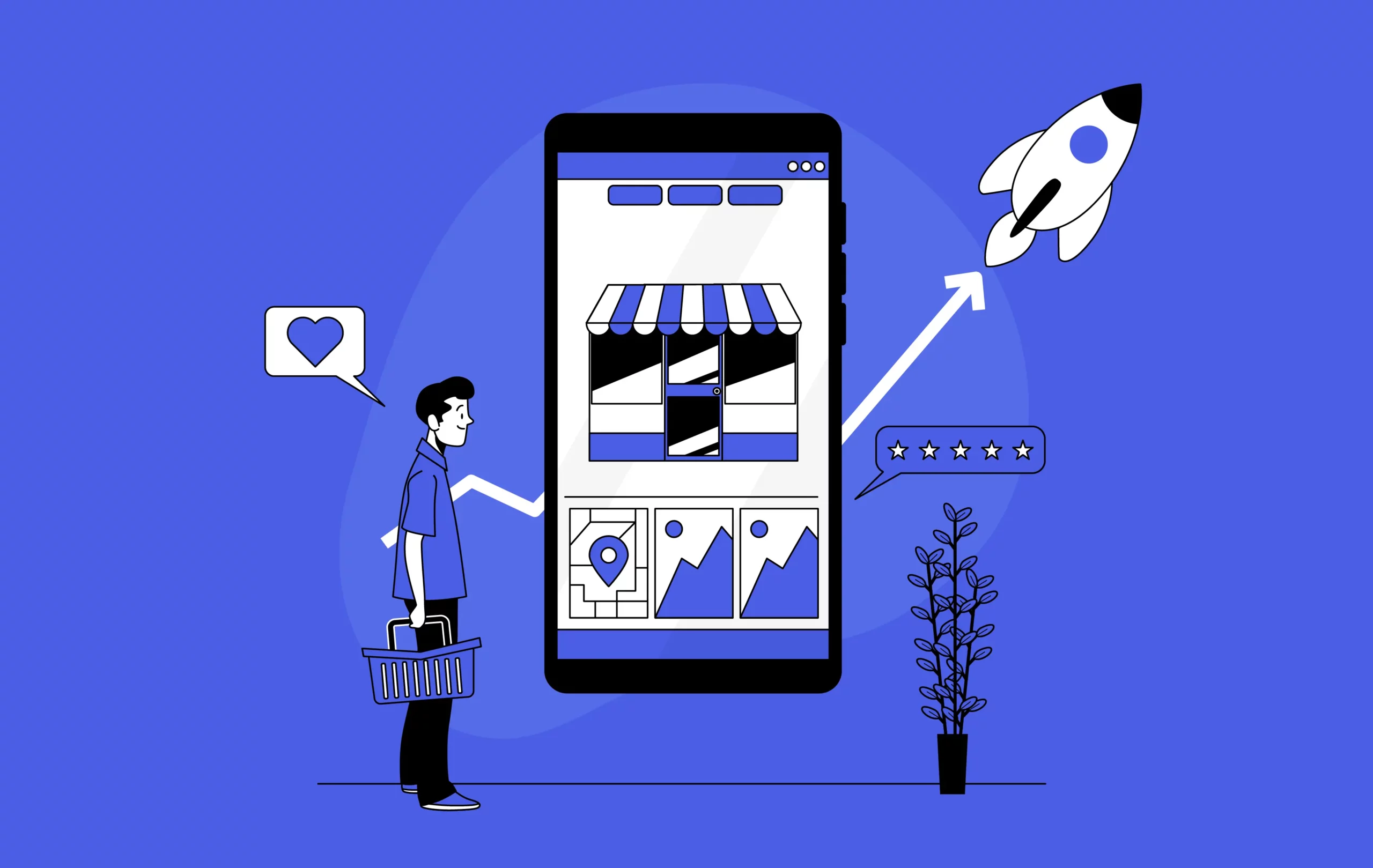
How ERP eCommerce Integration Can Help Scale Your Business to New Heights
Operating an eCommerce business is a complex process that requires effective management of multiple interconnected components. This includes various activities such as planning and allocation of resources, inventory management, internal communications, etc. What makes eCommerce operations even more challenging is that each area often operates within separate systems, having its unique set of processes. Thus,…